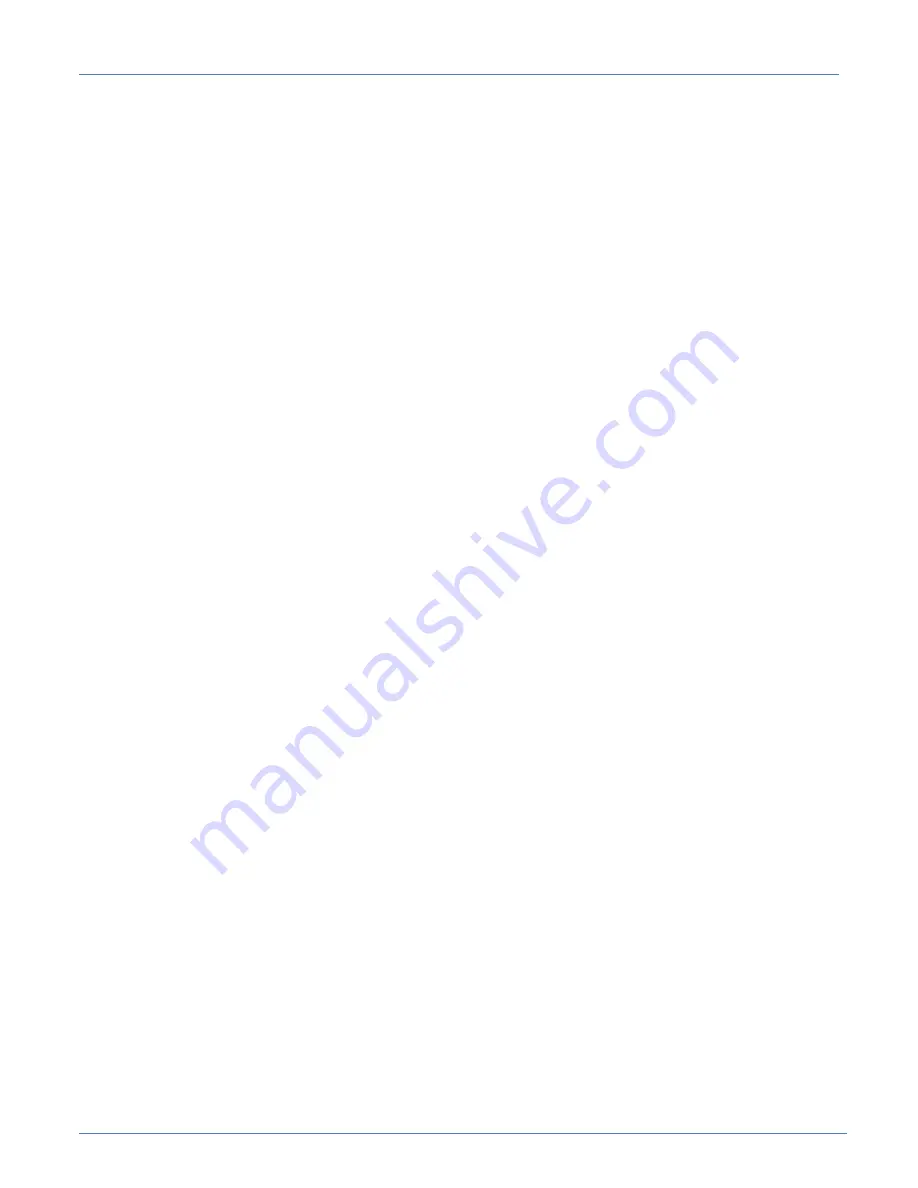
Technical Manual & Parts Lists
2
Liability
The machine should only be operated when in perfect working order, with due regard for safety and the
potential dangers, as well as in accordance with the Instruction Material. Faults and malfunctions
capable of impairing safety should be remedied immediately. We cannot accept any liability for personal
injury or property damage due to operator errors or non-compliance with the safety instructions
contained in this booklet. The risk rests exclusively with the end user.
The Instruction Material should always be kept near the machine so that it is accessible to all concerned.
The local, general, statutory and other binding regulations on accident prevention and environmental
protection must also be observed in addition to the Instruction Material. The operating staff must be
instructed accordingly. This obligation also includes the handling of dangerous substances and
provision/use of personal protective equipment.
The Instruction Material should be supplemented by instructions, including supervisory and notification
duties with due regard for special operational features, such as the organization of work, work
sequences, the personnel deployed, etc.
The personnel's awareness of the dangers and compliance with the safety regulations should be checked
at irregular intervals.
Choice and Qualification of Personnel
Ensure that work on the machine is only carried out by reliable persons who have been appropriately
trained for such work - either within the company, by our field staff or at our office - and who have not
only been duly appointed and authorized, but are also fully familiar with the local regulations. Work on
the machine should only be carried out by skilled personnel, under the management and supervision of a
duly qualified engineer.
This not only applies when the machine is used for production, but also for special work associated with
its operation (start-up and maintenance), especially when it concerns work on the hydraulic or electrical
systems, as well as on the software/serial bus system.
Training
Everyone working on or with the machine should be duly trained and informed with regard to correct
use of the safety equipment, the foreseeable dangers which may arise during operation of the machine
and the safety precautions to be taken. In addition, the personnel should be instructed to check all safety
mechanisms at regular intervals.
Responsibilities
Clearly define exactly who is responsible for operating, setting-up, servicing and repairing the machine.
Define the responsibilities of the machine operator and authorize him to refuse any instructions by third
parties if they run contrary to the machine's safety. This applies in particular for the operators of
machines linked to other equipment. Persons receiving training of any kind may only work on or with
the machine under the constant supervision of an experienced operator. Note the minimum age limits
permitted by law.
From
the
library
of:
Diamond
Needle
Corp
Summary of Contents for 1335MHB
Page 2: ...From the library of Diamond Needle Corp ...
Page 34: ...Technical Manual Parts Lists 29 From the library of Diamond Needle Corp ...
Page 36: ...Technical Manual Parts Lists 31 From the library of Diamond Needle Corp ...
Page 38: ...Technical Manual Parts Lists 33 From the library of Diamond Needle Corp ...
Page 40: ...Technical Manual Parts Lists 35 From the library of Diamond Needle Corp ...
Page 42: ...Technical Manual Parts Lists 37 From the library of Diamond Needle Corp ...
Page 44: ...Technical Manual Parts Lists 39 From the library of Diamond Needle Corp ...
Page 46: ...Technical Manual Parts Lists 41 From the library of Diamond Needle Corp ...
Page 48: ...Technical Manual Parts Lists 43 From the library of Diamond Needle Corp ...
Page 50: ...Technical Manual Parts Lists 45 From the library of Diamond Needle Corp ...
Page 52: ...Technical Manual Parts Lists 47 From the library of Diamond Needle Corp ...
Page 54: ...Technical Manual Parts Lists 49 From the library of Diamond Needle Corp ...
Page 56: ...Technical Manual Parts Lists 51 From the library of Diamond Needle Corp ...
Page 58: ...Technical Manual Parts Lists 53 From the library of Diamond Needle Corp ...
Page 62: ...Technical Manual Parts Lists 57 From the library of Diamond Needle Corp ...
Page 64: ...Technical Manual Parts Lists 59 From the library of Diamond Needle Corp ...
Page 66: ...Technical Manual Parts Lists 61 From the library of Diamond Needle Corp ...
Page 68: ...Technical Manual Parts Lists 63 From the library of Diamond Needle Corp ...
Page 70: ...Technical Manual Parts Lists 65 From the library of Diamond Needle Corp ...
Page 72: ...Technical Manual Parts Lists 67 From the library of Diamond Needle Corp ...