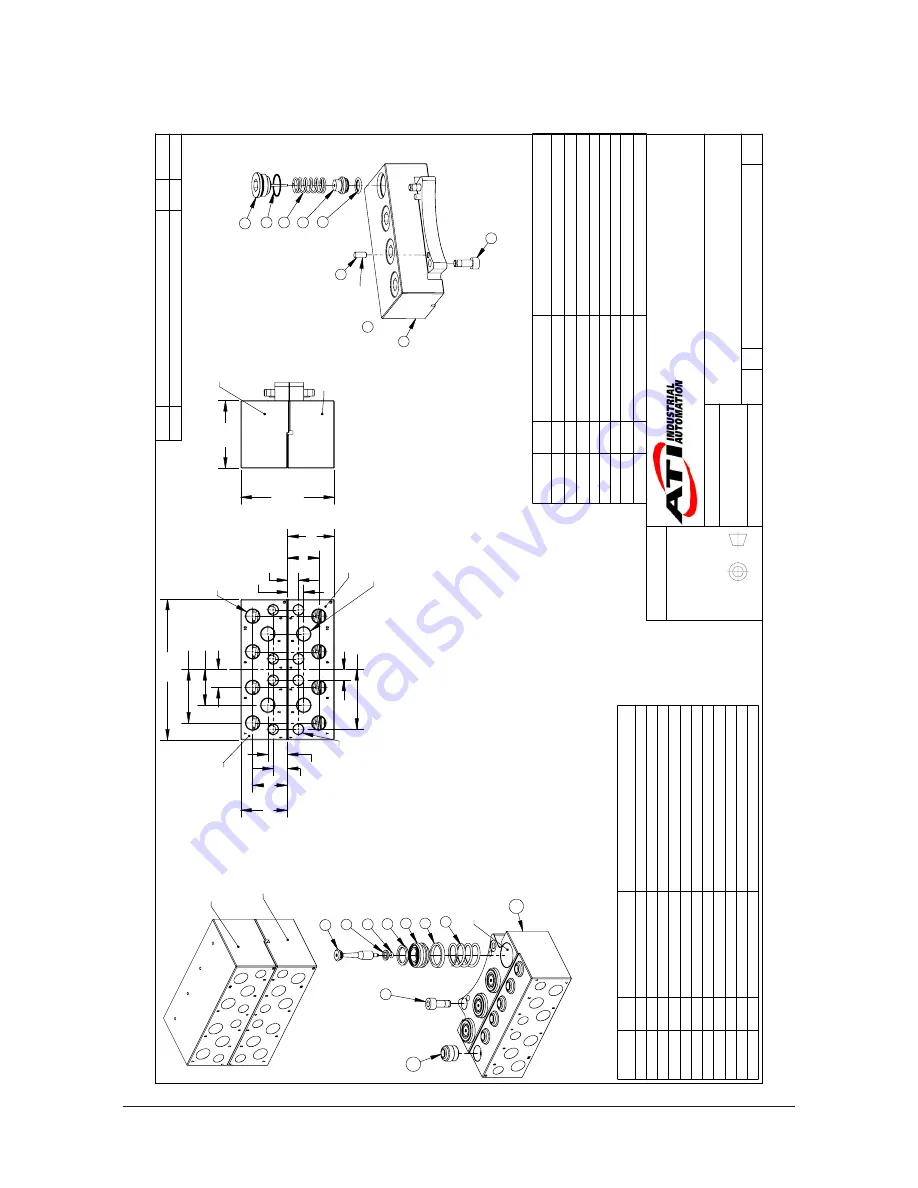
Manual, Fluid/Air, FS2
Document #9620-20-D-FS2-04
Pinnacle Park • 1031 Goodworth Drive • Apex, NC 27539 • Tel: 919.772.0115 • Fax: 919.772.8259 •
D-14
8. Drawings
3rd ANGLE PROJECTION
9121-FS2-M Master
9121-FS2-T Tool
9
3
1
8
2
7
10
5
Magnalube
Magnalube
Magnalube Bores
Magnalube After Installation
4
Magnalube
11
Note
4.
/ 45 in-lb
Note
3.
/ 10 in-lb
8
2
6
5
1
7
3
Magnalube
30 in-lb
Magnalube
4
Note
4.
/ 45 in-lb
NOTE: Dowel on Master side
is balloon
6
125.4
15.9 Typ.
47.6 Typ.
31.8 Typ.
9.5 Typ.
53.2 Typ.
12.7
17.5
31
9.5
14.3
27.8
41.7
41.6
9121-FS2-M
Master
9121-FS2-T Tool
G1/4 Checked Ports (4 Master / 4 Tool)
G1/4 Through Ports (2 Master / 2 Tool)
G1/8 Through Ports (4 Master / 4 Tool)
60.3
83.5
Coupled Approx.
9121-FS2-T Tool
9121-FS2-M Master
Note: Service Kit 9120-F1-T-Kit Contains (1) each of items 1,
2, & 6
Note: Service Kit 9120-F2-M-Kit Contains (1) each of items 1,
2, 3, & 7
Notes: Materials of Construction:
Housings & Springs - Stainless Steel
1.
Valve Components - Stainless Steel, PVC, Nitrile & Viton Rubber
2.
Replacement stem contains pre-applied thread locker. Use Loctit
e 7649
3. primer and Loctite 222 if reassembling with original st
em.
Replacement screw contains pre-applied thread locker. Use Locti
te 7649
4. primer and Loctite 242 if reassembling with original sc
rew.
Guidelines for Operation:
Maintain pH near neutral.
5.
Minimize particle count & size.
6.
Keep mating surfaces clean and free of debris.
7.
Rev.
Description
Initiator
Date
02
ECO 14748: Added Notes 3 & 4 to Materials of Construction.
TBC
9/26/2016
ITEM NO.
QTY.
PART NUMBER
DESCRIPTION
1
4
3410-0001065-01
O-Ring 14MM X 2MM Buna
2
4
3410-0001068-01
Mini U-Cup Seal 18mm ID x 22mm Buna
3
4
3410-0001183-01
O-Ring 6MM X 2MM Buna D90
4
4
3410-0001397-01
O-Ring, 2mm ID x 1.5mm W, Viton, D75
5
2
3500-1066016-21A
M6-1 x 16mm SHCS, SS, Pre-Applied
6
2
3540-0105010-21
5mm x 10mm Dowel Pin SST
7
4
3700-20-1459
SW-150A Master Fluid / Air Spring SS
8
4
3700-20-2994
Master Check Valve Piston, FA44
9
4
3700-20-2996
VALVE STEM, HIGH STRENGTH
10
1
3700-20-8620
FS2 Housing, Master
11
6
4010-0000021-01
1/4" NPT Rubber Bushing, Nitrile
ITEM NO.
QTY.
PART NUMBER
DESCRIPTION
1
4
3410-0001067-01
O-ring, 10mm x 2mm, Buna N, Dur. 90
2
4
3410-0001284-01
O-ring, .669OD x .047 wall, 70D, Buna-N
3
2
3500-1066016-21A
M6-1 x 16mm SHCS, SS, Pre-Applied
4
2
3540-0105010-21
5mm x 10mm Dowel Pin SST
5
4
3700-20-1457
SW-150A Tool Check Valve Piston
6
4
3700-20-1460
SPRING, F/A TOOL
7
1
3700-20-8621
FS2 Housing, Tool
8
4
9005-20-2267
F/A Plug Assembly, Tool, 3/8" Valves
B
1:2
1
1
REVISION
NOTES: UNLESS OTHERWISE SPECIFIED.
DO NOT SCALE DRAWING. ALL DIMENSIONS ARE IN MILLIMETERS.
DRAWN BY:
CHECKED BY:
D.Lawson-1/9/14
D.Swanson-1/10/14
TITLE
SCALE
SIZE
DRAWING NUMBER
PROJECT #
SHEET OF
9630-20-FS2
131203-2
02
PROPERTY OF ATI INDUSTRIAL AUTOMATION, INC. NOT TO BE REPRODUCE
D IN ANY
MANNER EXCEPT ON ORDER OR WITH PRIOR WRITTEN AUTHORIZATION OF A
TI.
1031 Goodworth Drive, Apex, NC 27539, USA Tel: +1.919.772.0115 Email: [email protected] Fax: +1.919.772.8259 www.ati-ia.com ISO 9001 Registered Company
FS2 Fluid/Air Module Customer Drawing