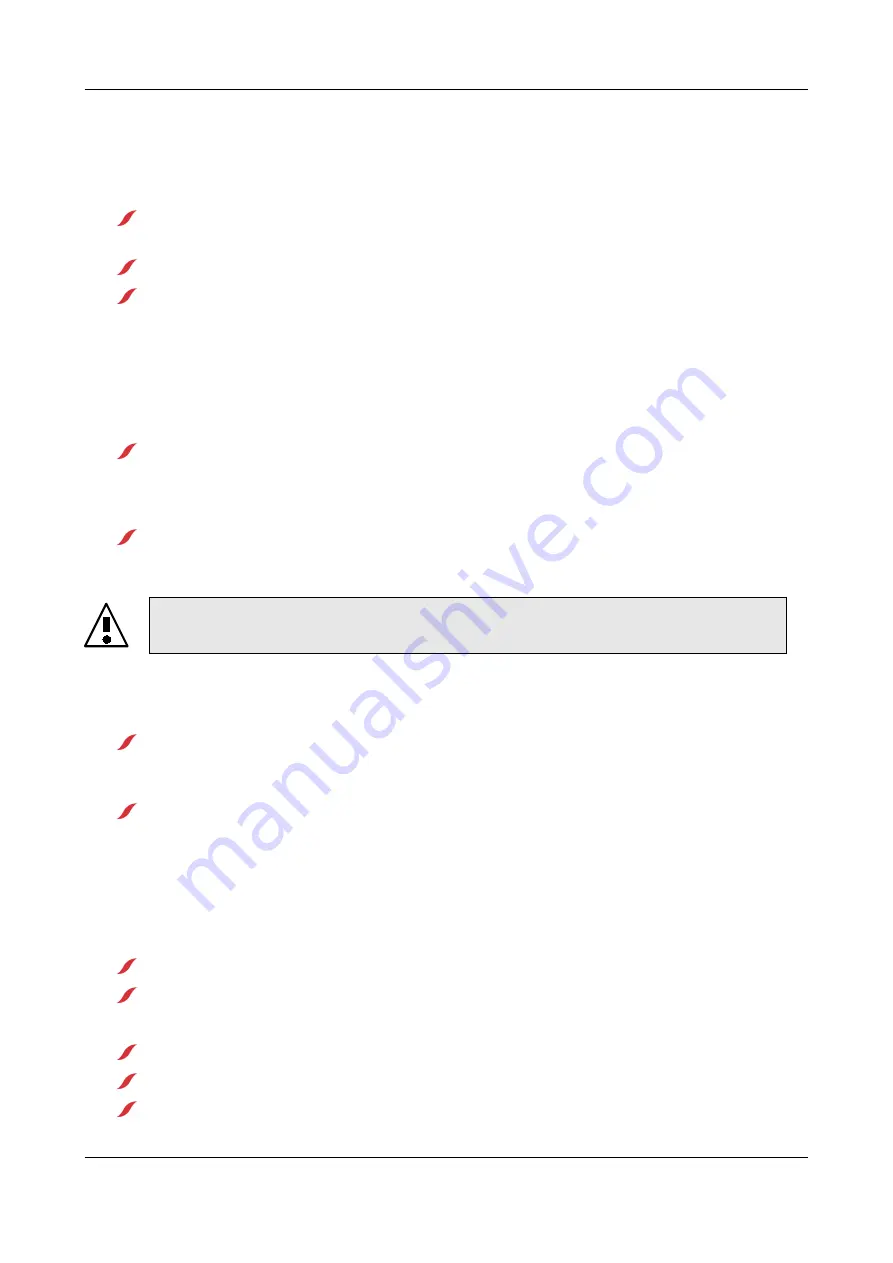
www.atestgaz.pl
Therefore regular calibration must be carried out to compensate the foregoing phenomenon. The
calibration must be performed only by authorized maintenance staff of the manufacturer with the
frequency is specified in the Calibration Certificate – see Table 10).
Please remember that the calibration should be carried out each time under the following circumstances:
when the deadline for a subsequent calibration is exceeded (the deadline is specified in the
Calibration Certificate or is indicated by the detector itself),
when the detector fails the functionality test or,
when the maximum limits for environmental impacts are exceeded.
Gas detectors manufactured by Atest Gaz are classified to the A category of instruments (see Appendix [10])
with respect to environments conditions for calibration.
When local conditions for calibration of gas detectors on site are not suitable the device must be taken out
from the plant and sent to the Atest Gaz office for calibration.
The detector calibration occurs digitally. It involves connecting a service device
a PC computer with appropriate software:
• to the control unit – a common data bus transfers data between detectors and the control unit,
• directly to the detector – when you open the cover,
or an Android device:
• directly to the detector – for devices with a Bluetooth radio interface (WI=BT) – see Section 4.5.
Execution of the calibration procedure needs a calibration kit and a specific reference gas
– see Table 13.
5.6.2.2 Calibration procedure
To calibrate gas detectors follow the procedure below:
to avoid undesired alarms when the detector responds to excessive concentration of reference
gas, switch the detector to be calibrated to the calibration mode – the calibration mode is
recognized by the control unit,
supply the calibration gas
• baseline (zero-air) gas (e.g. synthetic air or nitrogen),
• calibration (reference) gas (composition of reference gas depends on the gas to be detected
and the detector range)
to individual detectors one after another. Indications of the detectors are automatically recorded
by the supervising computer,
check and analyse the data acquired, apply a correction factor to each detector,
switch the calibration mode off.
During calibration the following is determined:
the degree of characteristics drift,
the degree of sinter contamination (measuring the response time T90),
the degree of sensor wear,
s. 20|27
User Manual: POD-064-ENG R05
Summary of Contents for ProGas 4
Page 1: ...POD 064 ENG R05 User Manual Gas Detector ProGas 4 Product code PW 017 PG4 X...
Page 45: ...www atestgaz pl Notes...
Page 46: ...www atestgaz pl Notes...
Page 47: ......