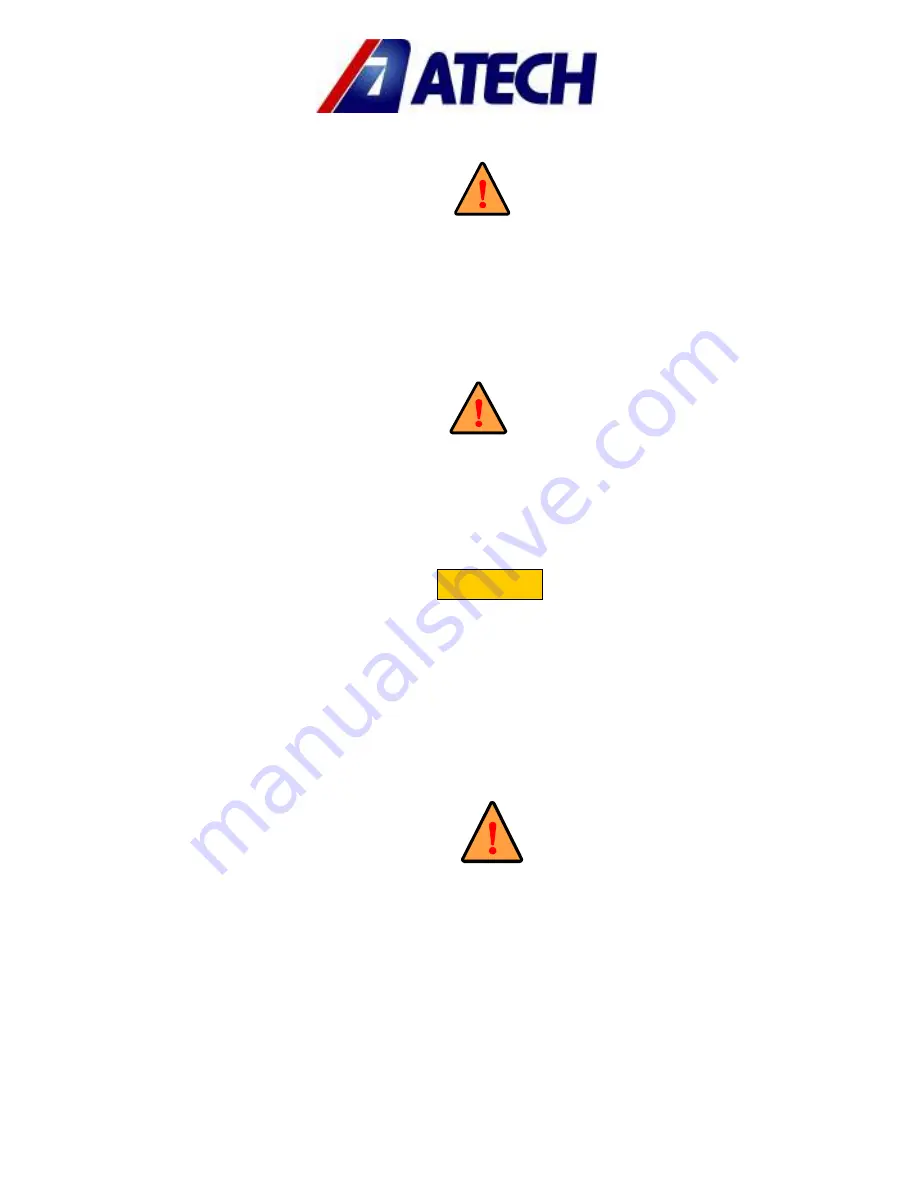
16
Operating and Safety Instructions
7.1.15 The router bit and triple drill unit should be moved down only after the regular
rotation has been reached.
8. CHANGING THE ROUTER BIT AND DRILL BITS
8.1
If it becomes necessary to replace the router bit for any reason, follow the following
order for replacement:
8.1.1
Unplug the machine
8.1.2
With the 2 wrench keys 14 and 17 loosen the router bit holder by turning the bolt of
the router bit holder in counter clockwise direction. Remove the router bit from its holder.
Insert the new router bit into the holder, and tighten the bolt with the wrench keys.
NOTE: Ensure that the router bit is fixed properly.
8.1.3
Check the router bit before using it. The router bit has to be inserted into the holder
properly. Don't use damaged router bits with improper function. Operate the machine for
at least 30 seconds to be sure that the router bit has been inserted and fixed correctly.
8.2 CHANGING THE TRIPLE DRILL BITS
8.2.1
Unplug the machine.
8.2.2
Loosen the screw on the connection of the triple drilling unit’s drill shaft with a 3 mm
hexagonal key. Replace the drill bit, and tighten the screw.
NOTE: Ensure that the drill bit is tightened properly.
CAUTION!