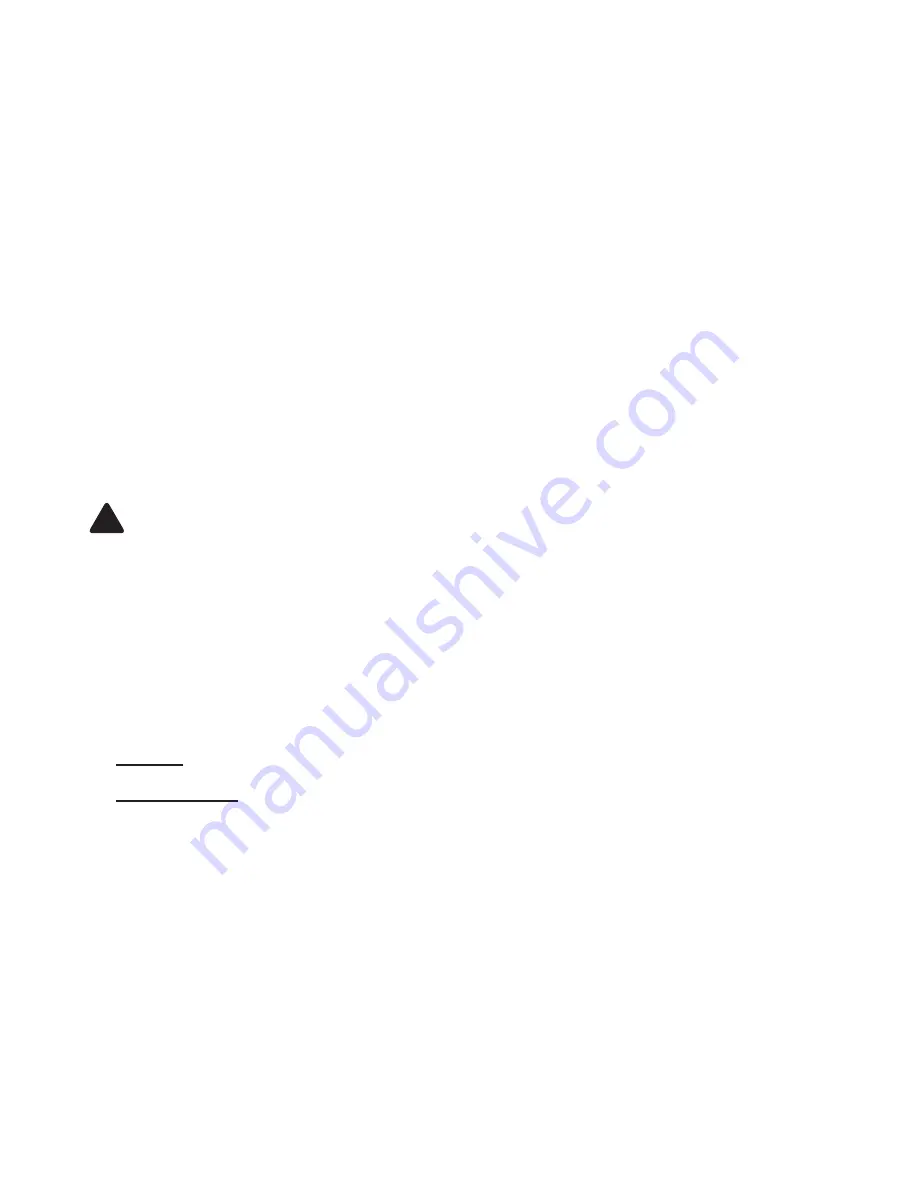
2
PREPARATION
Assembly
Insert handle into the handle fork. Tighten the bolt on handle fork to prevent accidental removal of handle while in
use.
Before Use
1. Verify that the product and application are compatible.
2. Before using this product, read the operator's manual completely and familiarize yourself thoroughly with the
product, its components and recognize the hazards associated with its use.
3. To familiarize yourself with basic operation, locate and turn the release valve (handle):
a.
Clockwise
until firm resistance is felt to further turning. This is the ‘
CLOSED
’ release valve position used to
raise
the saddle.
b.
Counter-clockwise
, but no more than 1/2 turn from the closed position. This is the ‘
OPEN
’ release valve
position used to
lower
the saddle.
4. With Ram Plunger fully retracted and release valve closed, pump the operating handle. If Ram Plunger responds
immediately, jack is ready for use. If jack does not respond, follow Bleeding/Venting Trapped Air instruction below.
5. Ensure that jack rolls freely. Raise and lower the unloaded saddle throughout the lifting range before putting into
service to ensure the pump operates smoothly. Replace worn or damaged parts and assemblies with authorized
replacement parts only.
Bleeding/Venting Trapped Air
With the release valve in the OPEN position (step 3b. above) and with saddle fully lowered, locate and remove the
cover plate, then remove the oil filler plug. Insert handle into handle fork and pump 6 to 8 full strokes. This will help
release pressurized air which may be trapped within the reservoir. Reinstall the oil filler plug and check operation.
SAFETY AND GENERAL INFORMATION
Save these instructions.
For your safety, read, understand, and follow the information provided with and on this
device before using. The owner and/or operator shall have an understanding of the device, its operating characteristics
and safety operating instructions before operating the equipment. The owner and/or operator shall be aware that use
and repair of this product may require special skills and knowledge. Instructions and safety information shall be read
to and discussed with the operator in the operator's native language, making sure that the operator comprehends
their contents, before use of this equipment is authorized. If any doubt exists as to the safe and proper use of this
device, remove from service immediately.
Inspect before each use.
Do not use if abnormal conditions such as cracked welds, damaged, loose or missing
parts are noted. Any equipment that appears damaged in any way, is found to be worn, or operates abnormally shall
be removed from service until repaired. If the equipment has been or is suspected to have been subjected to an
abnormal load or shock, immediately discontinue use until inspected by a factory authorized repair facility (contact
distributor or manufacturer for list of authorized repair facilities). It is recommended that an annual inspection be
made by an authorized repair facility. Labels and Operator's Manuals are available from the manufacturer.
PRODUCT DESCRIPTION
This Hydraulic Service Jack is designed to lift, but not support, one end of a vehicle. Immediately after lifting, loads
must be supported by a pair of appropriately rated jack stands. This Swift Lift service jack has a unique feature that
provides fast, no load lifts to the jacking point, at which time it lifts in approximately 1/4"~3/4" increments.
Never
use a hydraulic jack as a stand alone support device. After lifting, immediately support the lifted
vehicle with appropriately rated jack stands. Never place any portion of your body under the vehicle when
lifting or lowering.
!