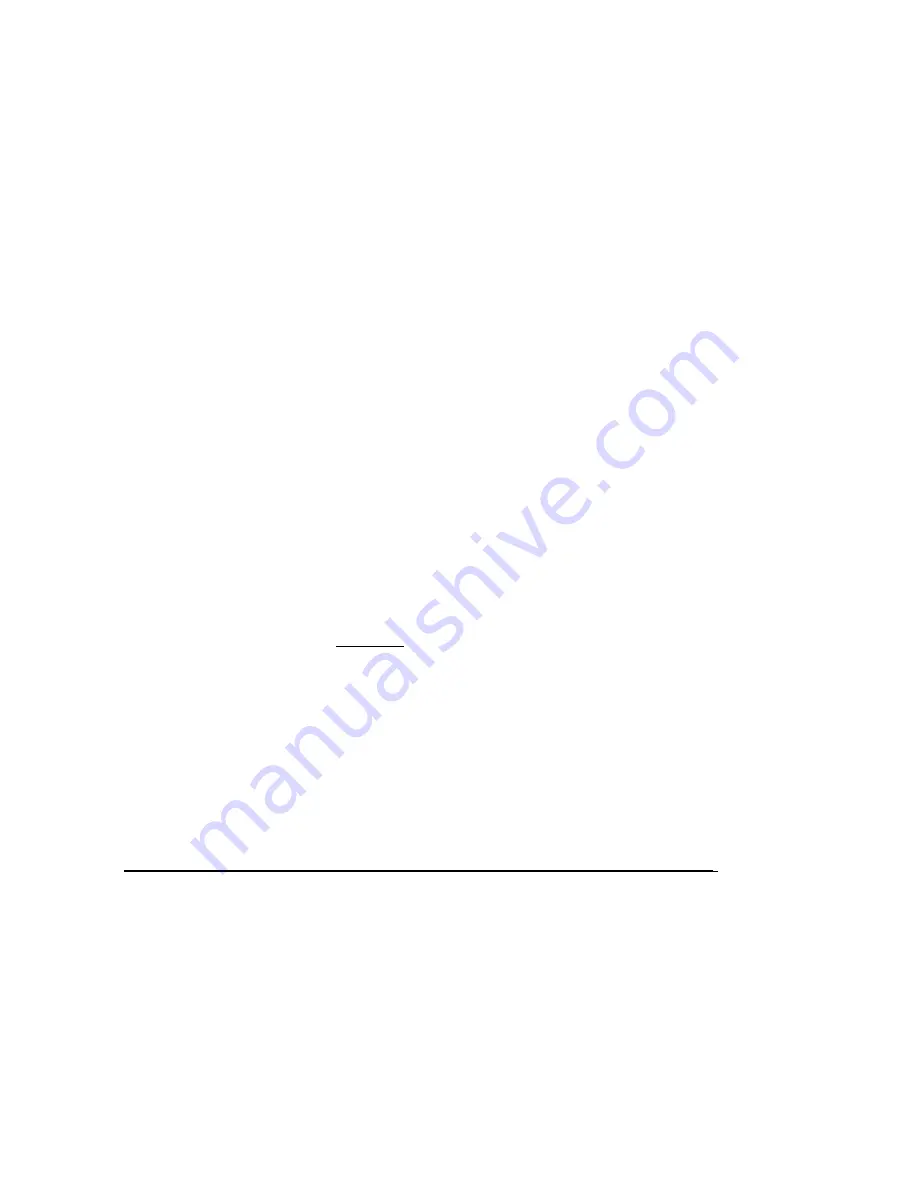
31
○
Other Software – There are many software packages that include aids to polar alignment that can be found
through a Google search. Some will work better than others. Do not be fooled into thinking that your
alignment is perfect simply because a piece of software told you so. Polar Alignment is, after all, entirely
a mechanical issue. Apart from “Pole Align Wizard”, we do not have experience with these other software
programs and cannot vouch for them or provide support.
●
Star Drift method
– Traditionally, this very time-consuming procedure has been regarded as the most accurate
method of polar alignment. However, if you are using the old method of drift alignment that employs stars near the
eastern or western horizon, you may encounter problems from atmospheric refraction, which will skew your alignment.
To obtain more accurate results, choose stars somewhere near the celestial equator due south or slightly east and
west, but not below 45 degrees elevation.
For portable setups, we believe that our GTO Quick Star Drift Method using the Meridian Delay Feature and a
Finderscope (found in the keypad documentation as noted above) is a much more practical approach in terms of
providing highly accurate alignment and still leaving enough time to actually get some imaging done. A permanent
observatory setup where long unguided exposures are taken may still benefit from a final tweaking using the traditional
star drift method (as modified by the 45 degree elevation recommendation above) or from a software enhanced variant
like the
PEMPro™
Pole Align Wizard that allows a CCD to measure and calculate the drift much faster than can be
done at the eyepiece.
●
DRIFT ALIGNMENT – R.A. CORRECTION METHOD
– Please see the Technical Support page of our website for
the instructions to this alignment technique. This will provide the highest precision of polar alignment with the least
amount of drift within 45 degrees of the zenith (where most imaging is done).
Note: This and the “Pole Align
Wizard” are the preferred alignment method when tweaking the RAPAS orthogonality.
Making Precise Altitude and Azimuth Adjustments
The mechanics of altitude and azimuth adjustment are relatively straightforward. In the discussion below, we will provide
some information and tips that will give you the greatest success with your 1100GTO regardless of the polar alignment
method you choose for determining the amount and direction of each adjustment. We’ll leave the choice of method up to
you. (Did we mention the GTO Quick Star-Drift Method?) We list the fine altitude adjustment first because our GTO Quick
Star-Drift Method begins with altitude. Many texts for the classic star-drift method begin with the azimuth adjustments.
When you made your rough alignment earlier, you loosened everything up, got the mount close, and then tightened
everything back down. Any minor shifting that occurred from locking things down tight was of no consequence since it
was a rough procedure. Now you are fine-tuning the alignment. Regardless of whether you start with altitude or azimuth,
begin the fine adjustment process with
everything
locked down as if you were already finished. Then, loosen only what is
required to make the adjustment, and loosen as little as possible. Your final adjustment should always be with everything
virtually, but not quite fully locked. It is may be helpful to use the technique of tightening the knobs a little more with each
new adjustment.
Fine Altitude Adjustment
Slightly loosen the four Altitude Lock Knobs, but do NOT loosen the polar axis pivot screws. Move the polar axis up or
down with the large Altitude Adjuster Knob located in the front of the polar axis assembly. If lowering the axis, you may
need to “help” the axis down if your lock knobs are somewhat tight. If you lower the axis, always be sure that the axis
remains in firm contact with the stainless steel thrust pad. Please refer to the illustrations earlier in this manual if you are
unsure about these parts.
Final adjustment should always be made pushing up in altitude.
One full turn of the altitude knob is approximately 0.6031 degrees (36.1 arcminutes).
Tips for Adjusting the Altitude
1. The mount’s polar axis is held in place between the two side plates. It is possible for the mount to shift slightly when the
locking knobs are fully tightened down after adjustment of the altitude angle. To prevent this shift, it is suggested that
the initial fine altitude adjustment be done with these knobs hand snugged, and as you approach the final adjustment
point, tighten the knobs, first to hand tight, and finally with a hex key after each small movement. As you converge on
the pole in altitude, each successively smaller adjustment is made against greater resistance from the ever tighter lock
knobs.
2. Approach the pole from below and try not to overshoot. If you accidentally move the axis too high and overshoot the
altitude angle, it is better to loosen the four lock knobs a bit, and bring the axis back down a very small amount before
proceeding back up with the knobs tightened up again. This way you are using the weight of the mount to insure a
solid connection to the altitude adjuster. The “captain’s wheel” design of the Altitude Adjuster Knob provides the neces-
sary leverage during the final “tweaking” adjustment phase when the locking knobs are quite tight.