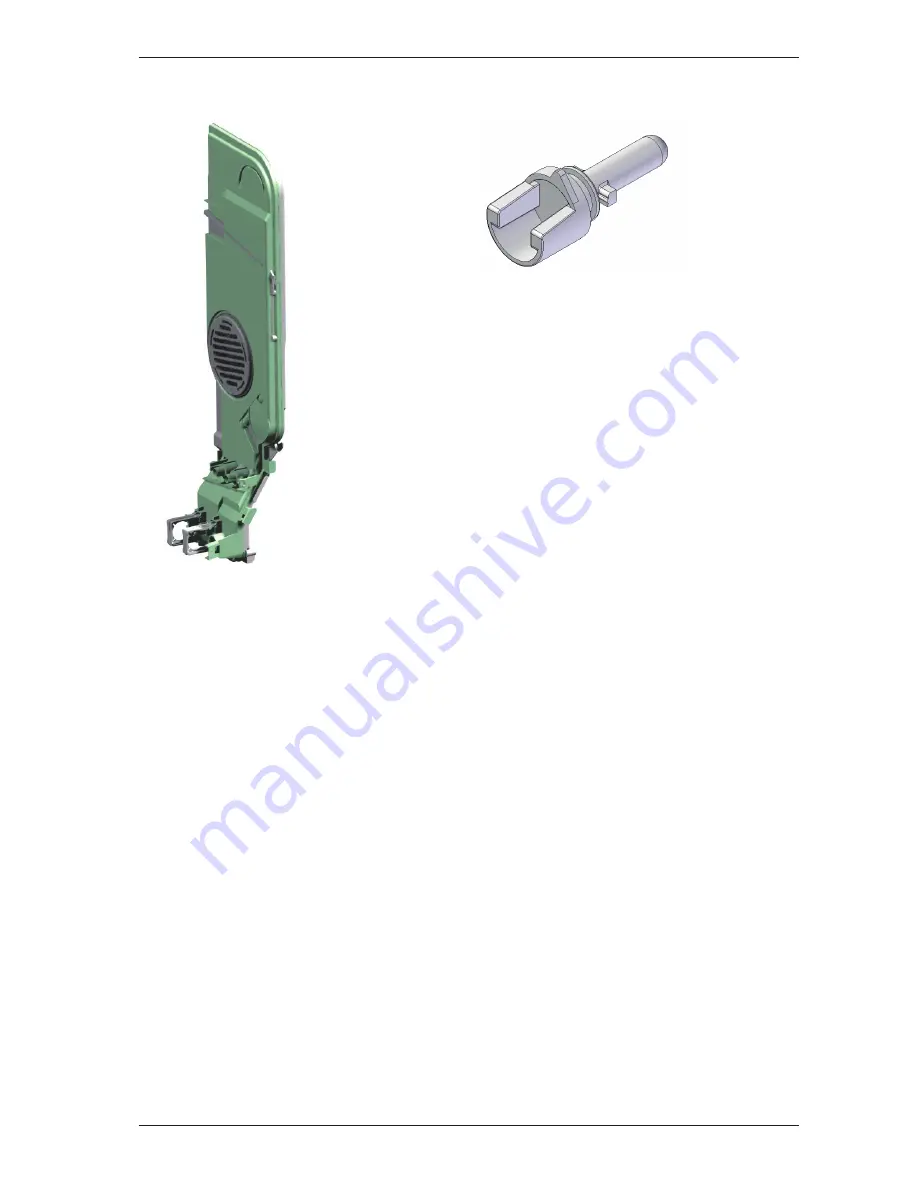
Service manual DW90
14
Component description
Air gap
The air gap is found next to the cleaning
compartment. It comprises channels through
which the incoming water flows into the
cleaning compartment. These channels also
contain an anti-backflow device and the
flow sensor through which the water passes.
Certain models are equipped with a water
pocket that collects water used for the water
softener (only machines with a water softener).
The air gap also works as a channel of air taken
in during the drying phase, as well as a pressure
relief for excess air when opening and closing
the door. On machines with Turbo Drying
Express (TDE) a lid is mounted on the inside
of the air gap. If there is condensation in the
kitchen interiors, make sure the lid is correctly
fitted.
Purpose:
To prevent dirty water from the
cleaning compartment being sucked back into
the water supply, and lead air to and from the
container.
Thermistor
The thermistor for temperature measurement
is located at the front edge of the bottom
drain. The thermistor measures and controls
the water temperature, which can be up to
70°C (158°F). If the thermistor short-circuits or
loses contact with the CU, or of the thermistor
does not register a temperature increase of
5°C (41°F) within 10 minutes of the element
being activated, the element is switched off and
a fault code is indicated. This is only indicated
in the service menu. The thermistor is of the
NTC type (Negative Temperature Coefficient),
i.e. its resistance decreases as temperature
increases.
Purpose:
To control the water temperature during
the dishwashing process.
Light
The light is a 5 W/12 V halogen bulb powered
by the control unit via a micro switch. The
lamp is activated when the door is opened
more than 5° and automatically deactivated
when the door has been open for more
than 30 minutes. The control unit features
protective components that limit the current
to the light in case of a short circuit or if a bulb
with too high a power rating is fitted. The
bulb can be replaced from inside the cleaning
compartment.
Summary of Contents for DW90 Series
Page 1: ...Service manual Dishwasher DW90...
Page 2: ...Service manual DW90 2...
Page 35: ...Service manual DW90 35 PERSONAL NOTES...
Page 38: ...Service manual DW90 38 PERSONAL NOTES...
Page 39: ...Service manual DW90 39 PERSONAL NOTES...
Page 40: ...We reserve the right to make changes www asko com...