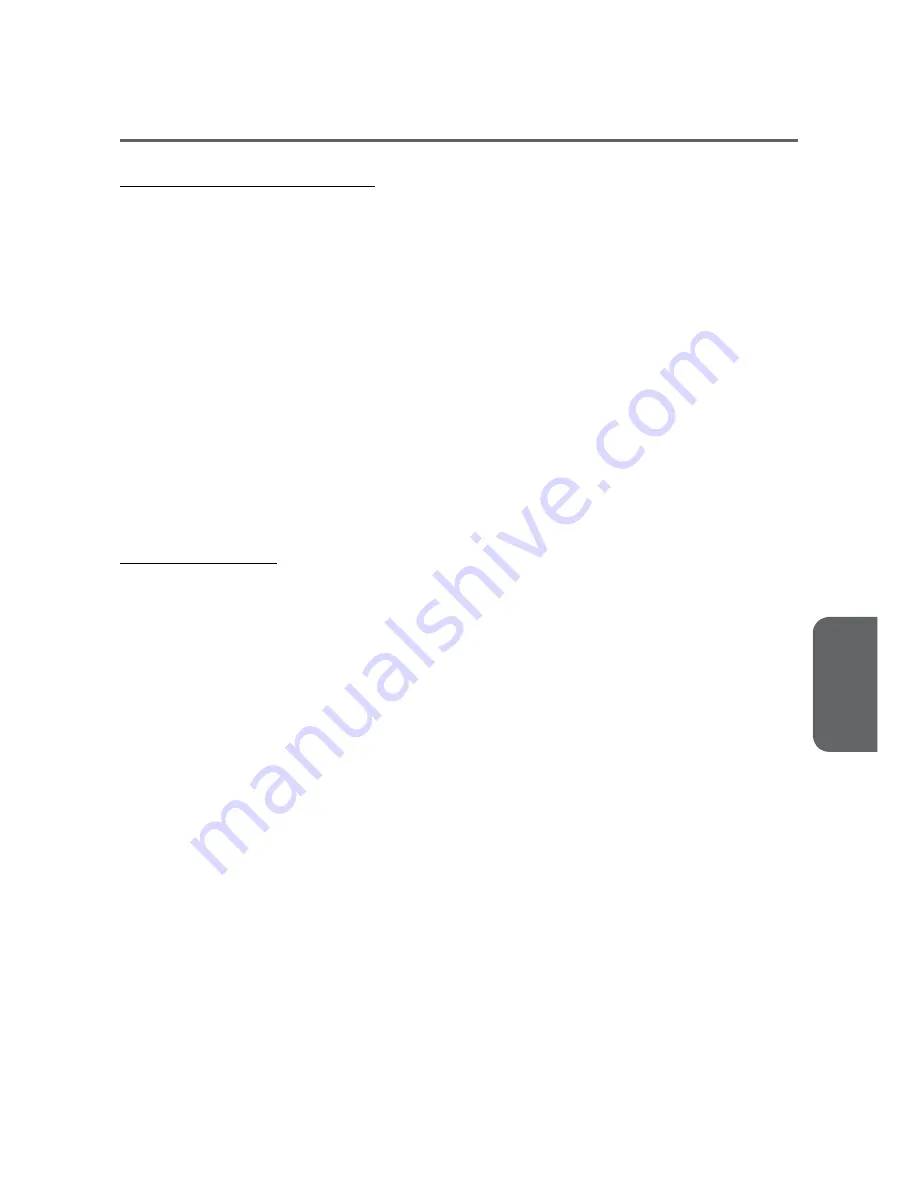
45
Preparation for Work - 2
Front and Rear Panel components :
1- Overload/temperature Warning led :
These leds light up when the machine cannot provide
output current sue to overheating. This situation is encountered when the ambient temperature
rises above 40°C and the duty cycle (operating efficiency) of the machine is exceeded. Leave
the machine on and wait until it cools off. The machine will be ready for operation again when
the lamp goes off.
2- Power indication Led :
Shows the On/Off state of the machine.
3- Welding Current Control Knob :
Adjusts the output current of the machine (welding amp. config).
4- TIG torch gas connection socket
5- Negative (–) Welding Cable Connection :
Welding current negative (–) output connection.
6- LIFT TIG-HF TIG (High Frequency TIG) selector switch
7- 2/4 trigger TIG and Coated electrode selector switch
8- ARc force (Coated electrode) and down slope (TIG) adjustment button
9- TIG torch trigger connection socket
10- Positive (+) Welding Cable Connection :
Welding current positive (+) output connection
1
1- On/Off switch :
Controls the main power input to the machine.
12- Gas hose connection socket
13- Input cable :
This machine is provided with a plugged input cord. Connect it to the mains.
TIG (GTAW) Welding :
The following actions need to be done before starting the welding procedures:
1- The TIG welding is generally carried out using the DC (–) pole. Connect the torch cable to the (–)
output of the machine (5) and the grounding clamp to the (+) output (10). Turn the connecter 1/4
turn clockwise after inserting in the plug with the guide pin on top. Attach the TIG torch gas hose
to the TIG torch gas hose socket (4). Make the connection between the gas cylinder regulator and
the gas hose connection socket (12). Connect the TIG torch trigger connector to the TIG torch
trigger plug (9) on the front panel of the machine.
2- Connect the work clamp to a clean place on the work piece free of paint or rust with the jaws in
complete contact.
3- Insert the mains cable to a suitable outlet.
4- Perform the following checks before starting the welding procedure:
a- Make sure that the welding machine is grounded securely.
b- Make sure that all contact surfaces, especially the contact between the clamp at the end of the
chassis cable and the work piece, are well secured.
c- Check that the welding cables are attached correctly.
d- The particles and sparks splashing around while Welding may cause a fire. Therefore, make
sure that no flammable materials are present in the welding area.
5- Turn on the On/Off switch (11).
6- Select the desired welding mode and trigger mode (6&7). The welding machine can operate in
the 2 trigger and 4 trigger TIG modes. In the TIG welding mode, Lift-TIG and High Frequency TIG
operations are available. In the Lift-TIG mode, a low-current short circuit is made by touching the
TIG torch to the work piece, then the TIG arc is formed while lifting the torch. In the HF mode, the
welding machine is ready for high frequency welding, hence the arc forms without touching the
TIG torch to the work piece.
8- Start welding observing the welding rules
Note: This welding machine may also be used for welding works with 2.5 and 4.0 mm diameter
welding electrodes with rutile and basic coating.
Current range for rutile and basic electrodes:
Ø 2.5 mm : 70 - 100 A Ø 3.2 mm : 100 - 140 A Ø 4.0 mm : 140 - 200 A
U
S
E
R
MAN
U
AL