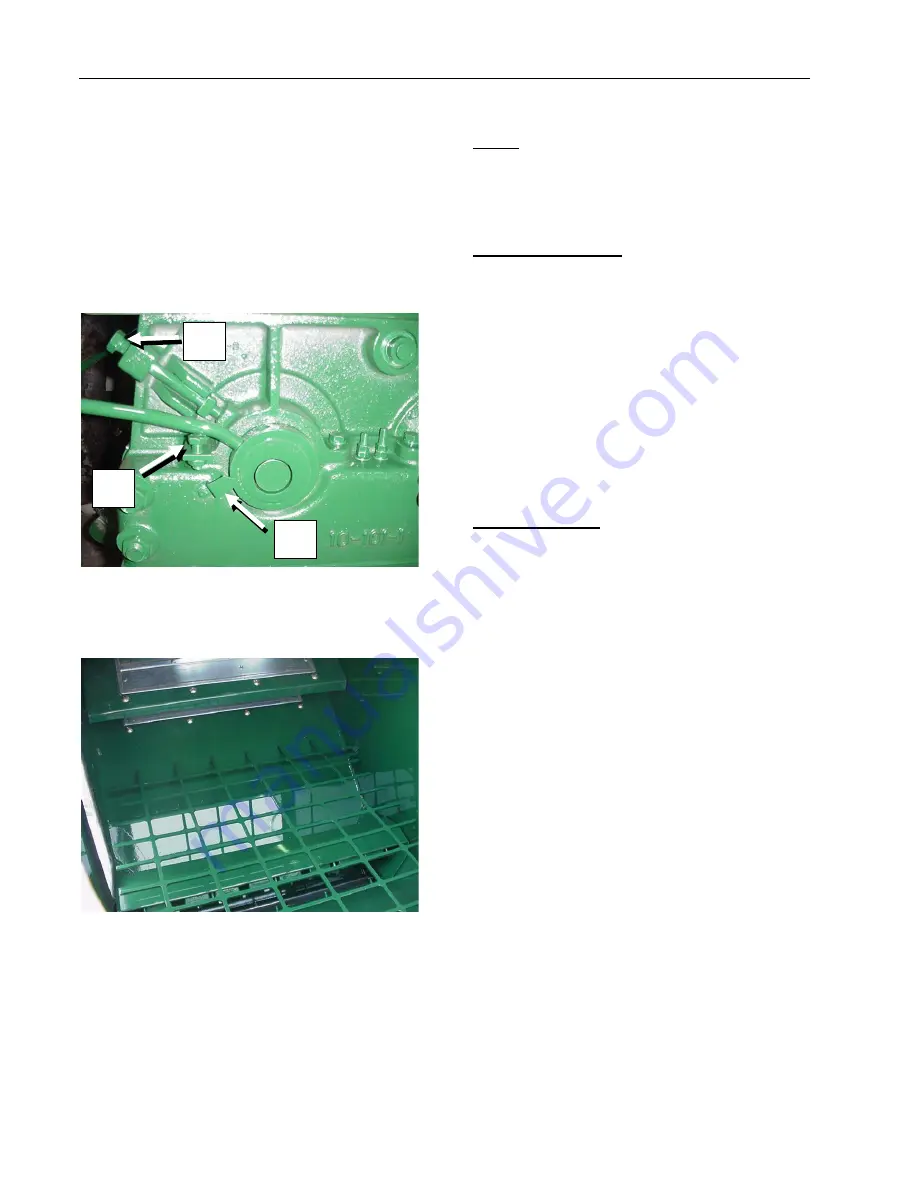
78
GRINDER MIXER ADJUSTMENTS
lock bolts when processing, otherwise the roll gap
will open and feed particle size will increase.
To check the roll gap, remove the 20 inch magnet
(See Figure 148) from the hopper throat. Using a
feeler gage, check the current roll gap with the
eccentric roll handle down on the stops and the
eccentric lock bolts snugged down. Be sure to
check the roll gap at the front and back of the rolls.
Also rotate the rolls to check several different
places on the roll diameter, as there may be 0.001
to 0.002 inch difference in the concentricity of the
rolls.
Figure 147 - Rollermill Housing Eccentric Bearing. A
- Eccentric Lock Bolts, B - Pointer Gauge, C - Stop
Bolts.
Figure 148 - Removing Magnet To Check Roll
Spacing.
To change the minimum roll gap, loosen the
eccentric lock bolts and pull the eccentric roll
handle up and out of the way. Loosen the jam nuts
on the 1/2 inch stop bolts (See Figure 149) and turn
both the front and rear stop bolts evenly, up for a
wider roll gap and down for a smaller roll gap. Lower
the eccentric roll handle to the stop bolts and re-
tighten the eccentric lock bolts. Re-check the roll
gap and repeat as necessary until the desired roll
gap is attained. Be sure to re-tighten the jam nuts
on the stop bolts when finished.
NOTE:
Rolls must not be set closer than 0.008 inch
gap. Never adjust the minimum roll gap setting with
the tractor PTO engaged. The rollermill rolls will be
severely damaged if they ever touch while the PTO
is engaged.
R
OLL
P
ARALLELISM
If the roll gap is different from front to back on the
rolls, the rolls are out of parallel and need to be
adjusted. This can occur from the eccentric roll
handle getting bent or twisted, or uneven roll wear
from not keeping the hopper full across the whole
width while processing. To adjust roll parallelism,
reset one stop bolt up or down. Be certain to push
down on each corner of the eccentric roll handle
when tightening the eccentric lock bolts to ensure
both sides of the handle are in contact with the
stops. The eccentric roll handle may have to be
twisted to accommodate an excessive stop bolt
adjustment.
R
OLL
S
CRAPERS
Roll scraper clearance needs to be monitored as
the rolls wear and should be adjusted after changes
in a minimum roll gap setting or when replacing
rolls. The main drive roll scraper should be set at
0.006 inch clearance and the eccentric roll should
be set at 0.050 inch clearance. Be sure the
minimum roll dap is set and the rolls locked in place
before setting the scrapers.
To adjust the roll scrapers, loosen the jam nuts on
the scraper adjustment bolts (See Figure 149). Turn
the adjustment nut clockwise to bring the scraper
closer to the roll. Turn the roll by hand while
adjusting the scraper. When the scraper contacts
the roll, back the adjusting nut off slightly until no
scraper to roll contract can be heard. On the
opposite side of the mill (front to back) turn the
adjustment nut on the same scraper until the
scraper contacts the roll. Back the adjustment nut
off slightly until no scraper to roll contract can be
heard. Recheck the side of the mill you started on
and repeat the procedure if further adjustment is
needed.
C
A
B
Summary of Contents for CATTLEMAXX 6105
Page 7: ...TABLE OF CONTENTS 5 ...
Page 14: ...12 INTRODUCTION Figure 5a Safety Decals ...
Page 22: ...20 PREPAIRING THE GINDER MIXER FOR OPERATION Figure 15 PTO Support ...
Page 27: ...OPERATION OF GRINDER MIXER 25 cleaned out Keep all bystanders away from the machine ...
Page 42: ...40 LUBRICATION Figure 70 Hammermill engaging pin shields removed for clarity ...
Page 49: ...SERVICE 47 Figure 96 Belt Removal Shields Removed For Clarity B C ...
Page 78: ...76 OPERATION OF CATTLEMAXX Figure 143 Hopper Inspection Window ...