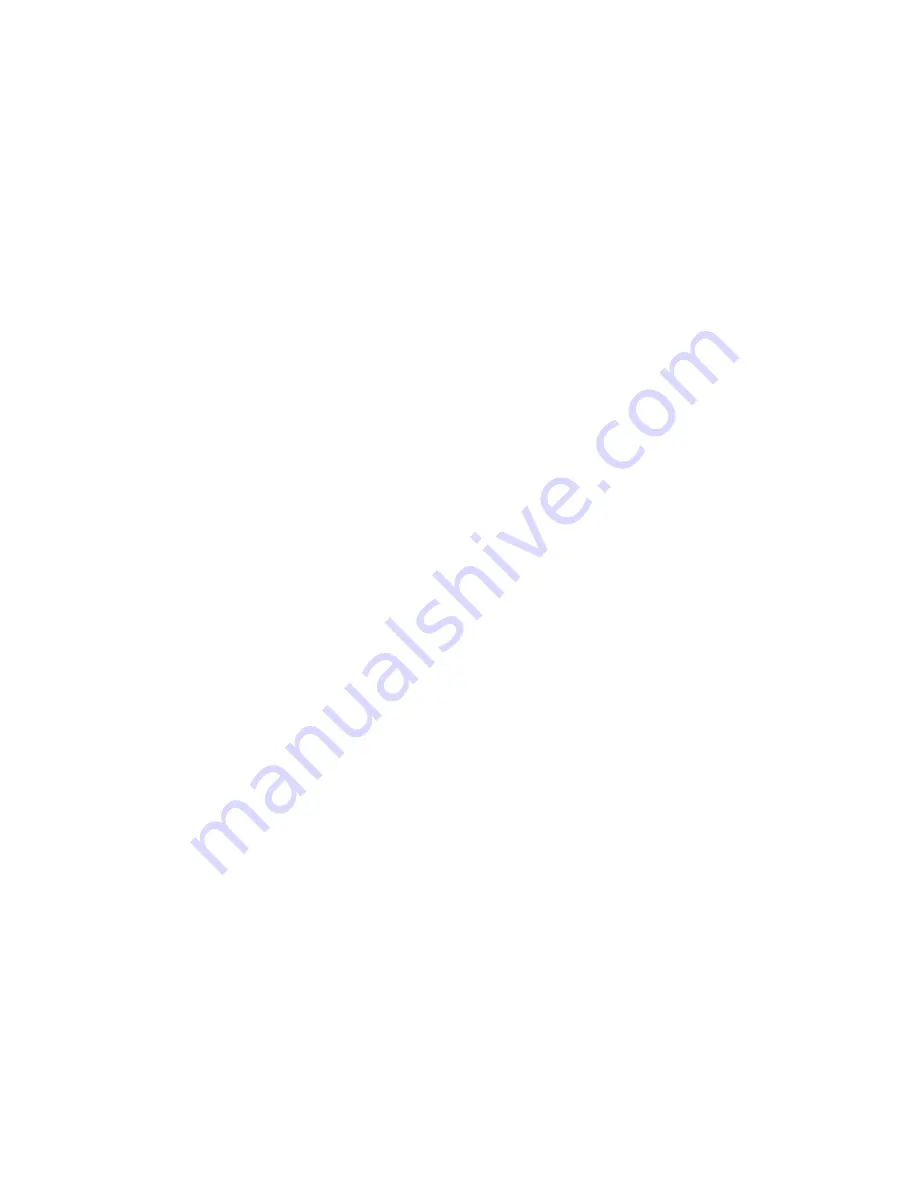
M103
85
5
DISASSEMBLY/ASSEMBLY INSTRUCTIONS
_
Assemble end plate (47) to rotor, aligning hole in end plate
with roll pin in cylinder. NOTE: Press on inner race of bearing.
_
Assemble nut (38) to end plate (41) and torque to 9 -- 12 ft lbs.
Be sure rotor turns without binding.
AUXILIARY GEARING
_
Pack bearings and lubricate gears liberally with ARO 33153
grease upon assembly.
_
Assemble one gear, with two bearings (52), to spindle, secur-
ing with shaft (51).
_
Assemble sun gear, where applicable, and opposite gear to
spindle, securing with shaft (51).
_
Rotate open portion of snap ring 90
_
from either shaft.
_
Assemble bearings (50) to spindle, pressing on inner race of
bearings.
_
Gearing assembly should contain approximately 1/4 oz. (7 g)
of grease.
_
Assemble spindle and components into ring gear (57).
DRIVE GEARING
_
Pack bearings and lubricate gears liberally with ARO 33153
grease upon assembly.
_
Assemble one gear, with two bearings (52), to spindle, secur-
ing with shaft (51).
_
Assemble sun gear, where applicable, and opposite gear to
spindle, securing with shaft.
_
Rotate open portion of snap ring 90
_
from either shaft.
_
Gearing assembly should contain approximately 1/4 oz. (7 g)
of grease.
_
Assemble one bearing (65) into ring gear (64), pressing on
outer race of bearing. NOTE: Assemble bearing with shielded
side toward gears.
_
Assemble spindle and components into ring gear.
_
Assemble paired spacers (66) and bearing (65) into ring gear.
_
Assemble auxiliary gearing to drive gearing.
_
Assemble spacer (49) and motor assembly to auxiliary gear-
ing.
_
Thread adapter (79) into spindle and slide motor and gearing
into housing (7), aligning key groove in ring gear (64) with slot
in housing. Remove adapter (79).
_
Lubricate ‘‘O’’ rings (2) and wiper (3) and assemble into hous-
ing (1).
_
Assemble housing (7) into housing (1) from the rear.
_
Assemble key (75) into slot in housing (7), long leg of key up-
ward. NOTE: Short leg of key to be flush with o.d. of housing
(7).
_
Assemble seal (76) to lock nut (77) and assemble lock nut to
housing (7) -- LEFT HAND THREAD. Do not tighten lock nut
(77).
_
Assemble torque arm (73) to housing (7), aligning slot with
key (75).
_
Push housing (7) toward the rear of the tool.
_
Assemble cap screw (34) to control rod (37), but do not tight-
en.
_
Orient cylinder (6) and components with housing (1), aligning
feed tube (98) with hole in housing.
_
Push piston (11) all the way forward in cylinder (6) and secure
piston to housing (7) using cap screw (13). Do not tighten cap
screw (13).
_
Push housing (7) and piston (11) toward the back of the tool
while sliding cylinder (6) into position.
_
Align components, then tighten cap screw (13).
_
Pull control rod (37) back and assemble adjustment screw
(20) into position.
_
Assemble adjustment screw (21) to bracket (28) and as-
semble gasket (16) and end cap (17) to cylinder (6), securing
adjustment screws.
_
Secure end cap with four cap screws (18). Do not tighten.
_
Tighten lock nut (77) securely -- LEFT HAND THREAD.
NOTE: If lock nut is not tight enough, motor and gearing could
spin in housing, due to high torque.
_
Assemble nut (78) to lock nut (77) -- LEFT HAND THREAD.
_
Assemble adapter (79) to gearing spindle.
_
Align bracket (35) with adjustment screws (20 and 21).
NOTE: Adjustment screw (20) is to be free in hole in bracket
(35) and collar (23) on adjustment screw (21) is to clear brack-
et (35).
_
Tighten cap screws (18 and 34).
_
Assemble nose housing (84) to housing (1), securing with
cap screws (4).
_
Assemble cover (80) and end cap (81) to tool, securing with
screw (83).
_
Assemble cover (33) to tool, securing with screws (30).
PISTON AND HYDRAULIC CHECK DISASSEMBLY
_
Clamp tool in a smooth face vise, clamping on square portion
of handle (140).
_
Remove screw (83), releasing cover (80) and end cap (81).
_
Loosen screws (30), releasing cover (33).
_
Loosen four cap screws (4). Twist nose housing (84) clock-
wise and remove from tool.
_
Remove four cap screws (18), releasing end cap (17) and
gasket (16). Remove adjustment screws (20 and 21).
_
Remove cap screw (34) at front end of tool and pull control rod
(37) and bracket (35) from housing (1).
_
Remove cap screw (13).
_
Remove cylinder (6), including piston (11), feed tube (98) and
components. NOTE: Do not remove ‘‘O’’ rings (96) unless
damage is evident.
_
Remove piston (11) from the rear end of cylinder (6).
_
Remove retaining ring (101), releasing feed tube (98) from
piston (11). NOTE: Do not remove set screw (97).
_
Remove two screws (29), releasing bracket (28).
_
Unthread and remove swivel fitting (124)(toward front of tool)
and tube (126) from housing.
_
Loosen cap screw (27).
_
Unthread and remove swivel fitting (124) from control assem-
bly (127).
_
Loosen set screws in control assembly (127) and remove
control assembly from hydraulic check (129).
_
Remove retaining ring (128), releasing hydraulic check (129).
_
Remove cap screw (95), releasing spring (93) and spool (92).
NOTE: Do not remove valve sleeve (90) unless damage is ev-
ident.
_
Remove retaining rings (143), releasing screens (142) and
muffler pads (141).
_
NOTE: Do not remove logic assembly (135) or valve assem-
bly (137).
PISTON AND HYDRAULIC CHECK ASSEMBLY
_
Lubricate ‘‘O’’ ring (138) and assemble ‘‘O’’ ring and handle
(140) to housing, securing with cap screws (139).
_
Assemble muffler pads (141) and screens (142) into handle,
securing with retaining ring (143).
_
Lubricate ‘‘O’’ rings (89) and assemble to grooves in valve
sleeve (90).
_
Assemble valve sleeve (90) into housing (1).
_
Lubricate ‘‘O’’ rings (91) and assemble to grooves in spool
(92).
_
Assemble spool (92) and spring (93) into valve sleeve (90).
_
Lubricate ‘‘O’’ ring (94) and assemble to cap screw (95).
_
Assemble cap screw (95) to housing (1), securing spool and
spring.
_
Assemble bracket (35) to control rod (37), securing with cap
screw (34).
_
Assemble control rod (37) into housing (1).
_
Push housing (7) toward the rear of the tool.
_
Assemble cap screw (34) to control rod (37), but do not tight-
en.
_
Lubricate ‘‘O’’ ring (15) and assemble backup rings (14) and
‘‘O’’ ring (15) to groove in piston (11). NOTE: ‘‘O’’ ring to be lo-
cated between backup rings.
Summary of Contents for FA072A
Page 15: ...M103 85 15 ...
Page 16: ...PN 49999 133 ...