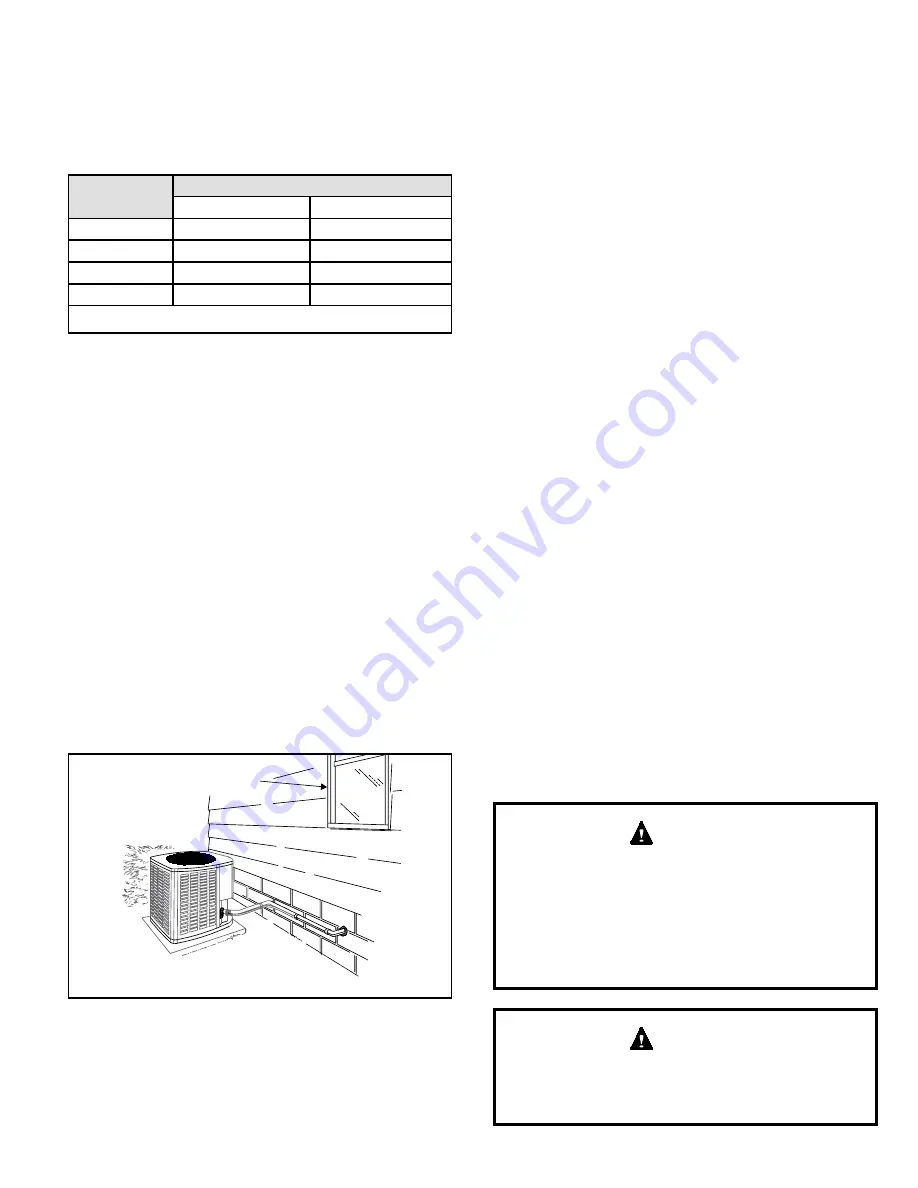
507607-03
Issue 1827
Page 5 of 23
Line Set Isolation
The following illustrations demonstrate procedures that
ensure proper refrigerant line set isolation. Figure 7 shows
how to install line sets on horizontal runs. Figure 8 shows
how to make a transition from horizontal to vertical. Figure
9 shows how to install line sets on vertical runs.
Table 2. Refrigerant Line Set Diameters (in.)
Model
16 SEER
Liquid Line
Suction Line
24
3/8
3/4
36
3/8
7/8
48
3/8
7/8
60
3/8
1-1/8
For lines longer than 50 ft., refer to long line set guidelines.
Brazing Connection Procedure
1. Cut ends of refrigerant lines square (free from nicks or
dents). Debur the ends. The pipe must remain round;
do not pinch end of line.
2. Before making line set connections, use dry nitrogen
to purge the refrigerant piping. This will help to prevent
oxidation and the introduction of moisture into the
system.
3. Use silver alloy brazing rods (5% or 6% silver alloy
for copper-to-copper brazing or 45% silver alloy for
copper-to-brass or copper-to-steel brazing) which are
rated for use with R410A refrigerant.
4. Remove the Schrader core assemblies before brazing
to protect them from damage due to extreme heat.
Replace the cores when brazing is complete.
5. Remove light maroon washers from service valves
and shield light maroon stickers to protect them during
brazing. Wrap a wet cloth around the valve body and
copper tube stub to protect it from heat damage.
Install unit away
from windows
Two 90° elbows installed in lineset
will reduce lineset vibration
Figure 6. Outside Unit Placement and Installation
6. Braze the line set to the service valve. Quench the
joints with water or a wet cloth to prevent heat damage
to the valve core and opening port. The tube end must
stay bottomed in the fitting during final assembly to
ensure proper seating, sealing, and rigidity.
7. Install the thermal expansion valve which is sold
separately and which is approved for use with R410A
refrigerant in the liquid line at the indoor coil (see
Refrigerant Metering Device section).
Refrigerant Piping
If the 4SCU16 LS unit is being installed with a new indoor
coil and line set, the refrigerant connections should be
made as outlined in this section. If an existing line set and/
or indoor coil will be used to complete the system, refer
to this section as well as the section that follows entitled-
Flushing Existing Line Set and Indoor Coil.
If this unit is being matched with an approved line set
or indoor coil which was previously charged with R-22
refrigerant, the line set and coil must be flushed prior to
installation. If the unit is being used with an existing indoor
coil which was equipped with a liquid line which served as
a metering device (RFCI), the liquid line must be replaced
prior to the installation of the 4SCU16 LS unit.
Field refrigerant piping consists of liquid and suction lines
from the outdoor unit (sweat connections) to the indoor coil
(flare or sweat connections).
Select line set diameters from Table 2 to ensure that oil
returns to the compressor. Size vertical suction riser
to maintain minimum velocity at minimum capacity.
Recommended line length is 50’ or less. Table 2 shows
the diameters for line sets up to 100’ although vertical lift
applications and trapping requirements need to be reviewed
for line sets over 50’; refer to long line set guidelines.
Installing Refrigerant Line
During the installation of an air conditioning system, it is
important to properly isolate the refrigerant line to prevent
unnecessary vibration. Line set contact with the structure
(wall, ceiling, or floor) may cause objectionable noise when
vibration is translated into sound. As a result, more energy
or vibration can be expected. Close attention to line set
isolation must be observed.
When flushing existing line set and/or indoor coil, be
sure to empty all existing traps. Residual mineral oil can
act as an insulator, preventing proper heat transfer. It
can also clog the thermal expansion valve, reducing
system performance and capacity. Failure to properly
flush system as explained in these instructions will void
warranty.
CAUTION
If ANY refrigerant tubing is required to be buried by state
or local codes, provide a 6 inch vertical rise at service
valve.
CAUTION