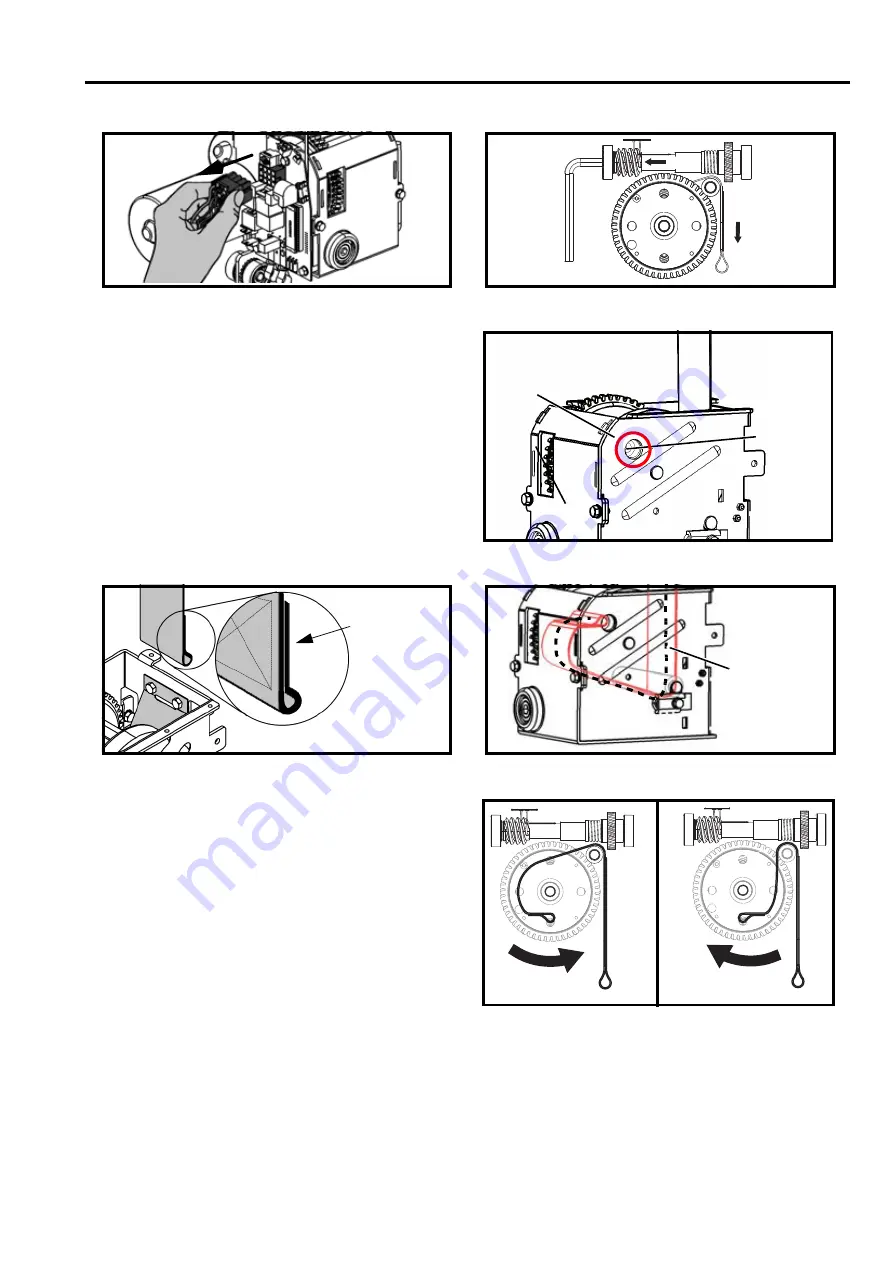
11
Service Procedures
00
1.
14
15
5.3
3
r
ev
. 8
b. Unwind the strap completely.
4)
Rotate the drum to align the strap bolt with the large
hole on the frame (see Fig. 13).
5)
Completely unscrew the strap bolt with a 6 mm Allen
key and remove the old strap.
FOR LIFTS EQUIPPED WITH LIMIT PLATE
(200.14070)
6)
Guide the new strap between the limit plate and the
plastic roller making sure to place the folded part
facing the limit plate (see Fig. 14 and Fig. 15).
7)
Align the loop of the strap with the hole of the
retaining bolt.
8)
Reinsert the bolt and tighten.
9)
Rewind the strap. Make sure it is in the correct
winding direction (see Fig. 16).
10) Grease the drum teeth with food-grade grease (refer
to “Parts List” manual for part number).
Fig. 11
Fig. 12
Fig. 14
Fig. 15
(a)
(b)
Fig. 13
Large
hole
Strap
bolt
Folded part
facing the
limit plate
Strap path
Fig. 16
Correct
Wrong
Summary of Contents for Maxi Sky 600
Page 1: ...Maxi Sky 600 Technical Manual 001 14155 33 rev 8 December 2017 ...
Page 26: ...26 ...
Page 41: ...Lift Dimensions Fig 71 41 ...
Page 46: ......