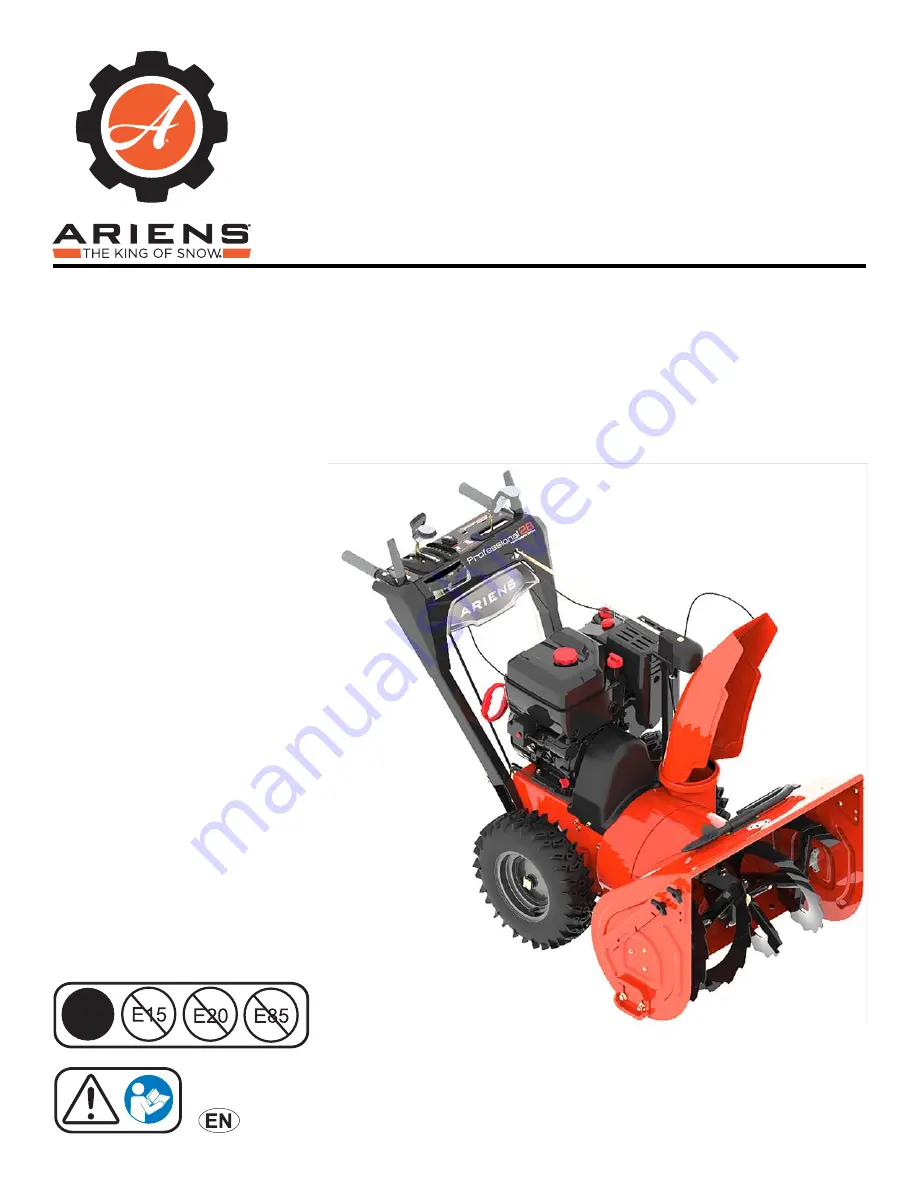
Professional Series Sno-Thro
With Hydrostatic Drive
05136630B • 12/18
ENGLISH
Models
926060 – Pro 28 RapidTrak
(SN )
926068 – Pro 28 EFI
(SN )
926069 – Pro 32 RapidTrak
(SN )
926070 – Pro 36 EFI
(SN )
926334 – Pro 32 12V CE
(SN )
926336 – Pro 28 EFI CE
(SN )
926337 – Pro 28 EFI CE Track
(SN )
926338 – Pro 28 EFI CE RapidTrak
(SN )
E10
®
Service Guide