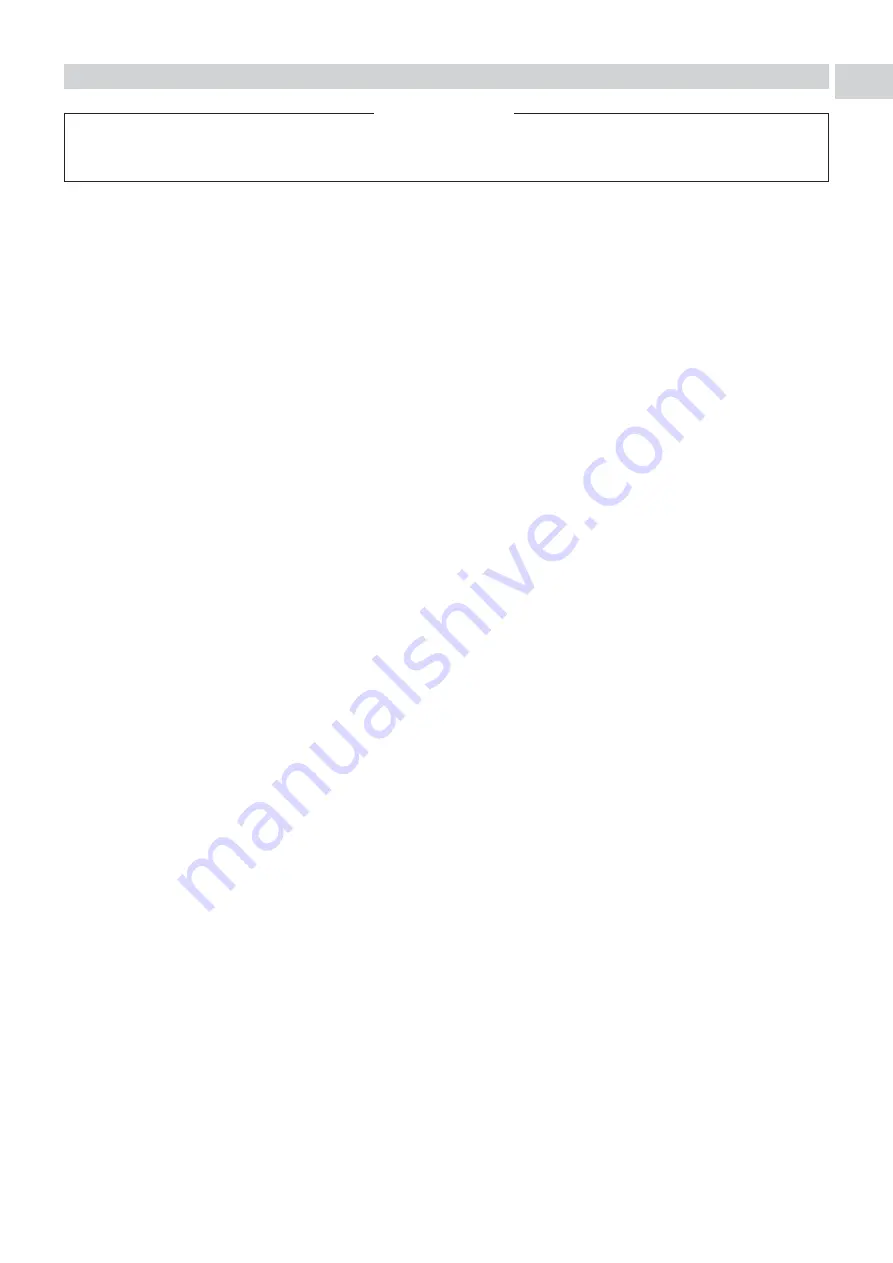
EN
29
7 - STARTING
Before carrying out any work on the installation, make sure that it is switched off and that access to it is
prevented.
Any work must be carried out by personnel qualifi ed and authorised to work on this type of unit.
IMPORTANT NOTE
7.1 - PRELIMINARY CHECKS
7.1.1 - HYDRAULIC CIRCUIT
• Hydraulic couplings correctly tightened.
• Hydraulic circuit operating correct:
- Air purge from circuits.
- Position of valves.
- Hydraulic pressure (1.5 to 2.0 bar).
•
Water-tight hydraulic circuit.
•
Water
quality:
- In order for the heat pump to operate under good conditions and provide optimum performance, it is
essential to ensure that the system’s water circuit is clean. If the water circuit becomes clogged, this
will signifi cantly affect the machine’s performance. The circuit must therefore be cleaned with suitable
products in compliance with current standards as soon as it is installed, both for new and renovation
work.
We recommend the use of products which are compatible with all metals and synthetic materials and
approved by offi cial bodies.
The water must adhere to the following characteristics:
- pH: 7 to 9.
- TH: 10 to 20°F.
- Dry material in suspension: < 2 g/l.
-
Granulometry: < 0.4 mm.
- Chloride: 50 mg/l maximum.
- Conductivity: 150 to 350 μS/cm
2
.
- Fibre: no fi bres.
Any disorder which may occur on our machines due to the poor quality of the fl uid in the installation will
not be covered by the warranty.
IMPORTANT:
If anti-freeze is added, use monopropylene glycol. A rate of 15 to 20% is required to avoid any risk
of corrosion.
Note:
The injection of antifreeze in the circuit must not be done at the pump suction of the unit and the
pump must not be used as a mixer. This is to prevent chemical alterations of the pump due to antifreeze
concentration.
7.1.2 - REFRIGERANT SYSTEM
• Check carefully for any leaks.
7.1.3 - ELECTRICAL SYSTEM
• The power cables are well fi xed to their connection terminals. Terminals that are poorly tightened may
cause overheating and malfunctions.
• The electric cables are well insulated from any sections of sheet metal or metal parts which could damage
them.
• The power cables and the low voltage cables (thermostat, probes) are properly separated.
• The unit is earthed.
7.1.4 - OTHER
• Overall good condition of the unit.
• No tools or other foreign objects inside the unit.