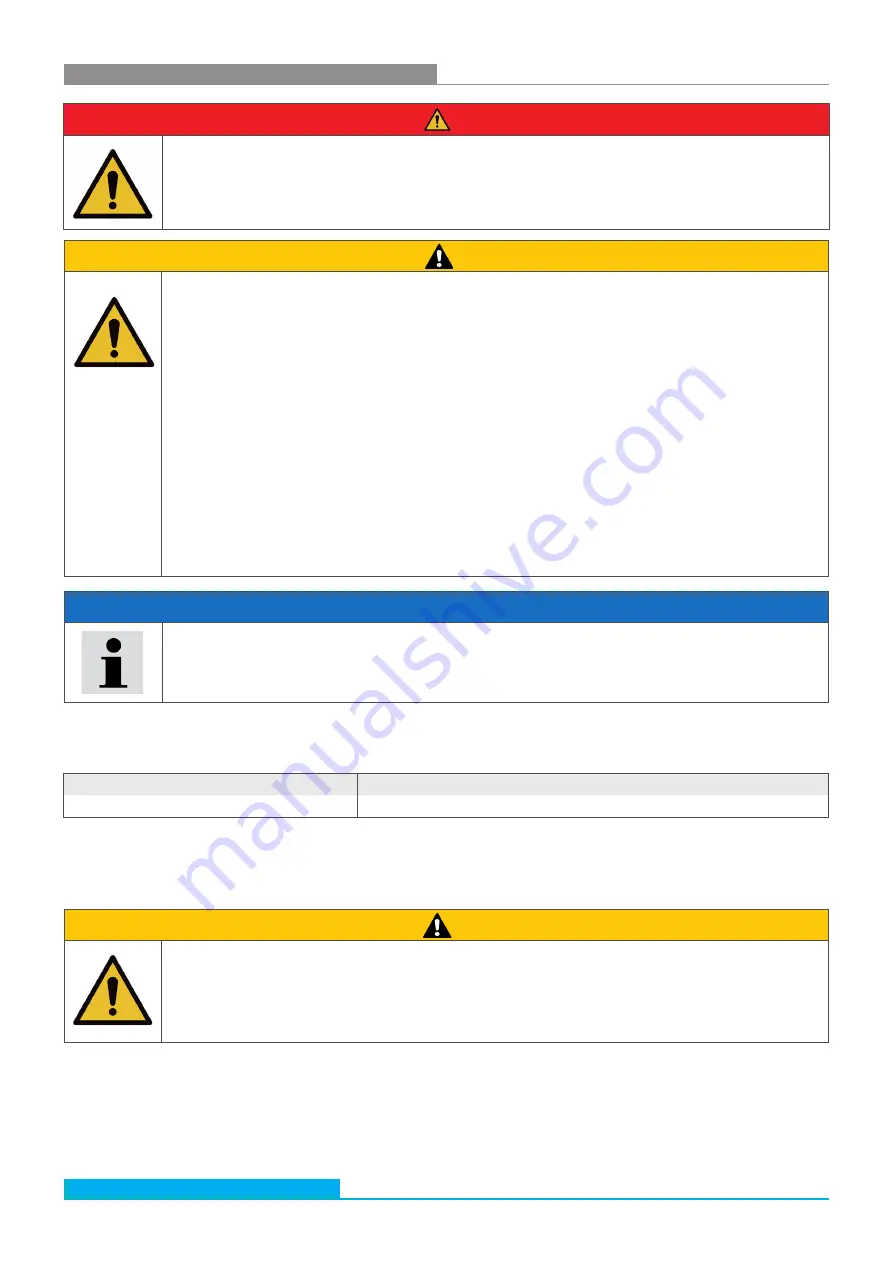
Subject to change · UMPCL 045_41733800 · 0321 · EN
Page 25
www.argo-hytos.com
CAUTION
Hydraulic oil spills
Environmental hazard / risk of slipping
›
Before maintenance and repair work, completely drain the unit.
›
In case of spills, cover the oil-covered surface immediately with an oil-binding medium.
›
Then immediately dispose of the oil-binding medium according to the national environmental regulations.
Ignition hazard
Risk of electrostatic charge by poorly conducting hydraulic fluid.
›
If the electrical conductivity of the hydraulic fluid is not known, please contact the manufacturer of the
hydraulic fluid.
Risk of burns
Contact temperatures according to DIN EN563 (3) and DIN EN13202 (4) may be exceeded during
operation.
›
Allow the filter to cool down before touching it.
11. Repair and maintenance
DANGER
Danger to life
Risk of electric shock
›
During repair work, turn off the unit and pull the mains plug.
NOTE
Impaired function by dirt ingress into the pump.
The function of the filter unit is no longer guaranteed.
›
During repair work, all parts coming in contact with the hydraulic medium, must be kept free of dirt and chips.
11.1 Maintenance overview
Except from the filter element, suction strainer, and OPCom screen protective elements the filter unit is maintenance-free.
Maintenance work
Maintenance interval
Checking / changing the filter element
Once the clogging indicator responds at a permissible viscosity.
11.2
Changing the filter element
1. Pump the filter element empty (see Chapter 10.2 "Filtering of liquids in the bypass flow", point 7).
2. Disconnect the off-line filter unit from the power supply and, if necessary, pull the mains plug.
CAUTION
Risk of burns
Contact temperatures according to DIN EN563 (3) and DIN EN13202 (4) may be exceeded during
operation.
›
Allow the filter unit to cool down before touching it.
Table 7: Maintenance overview