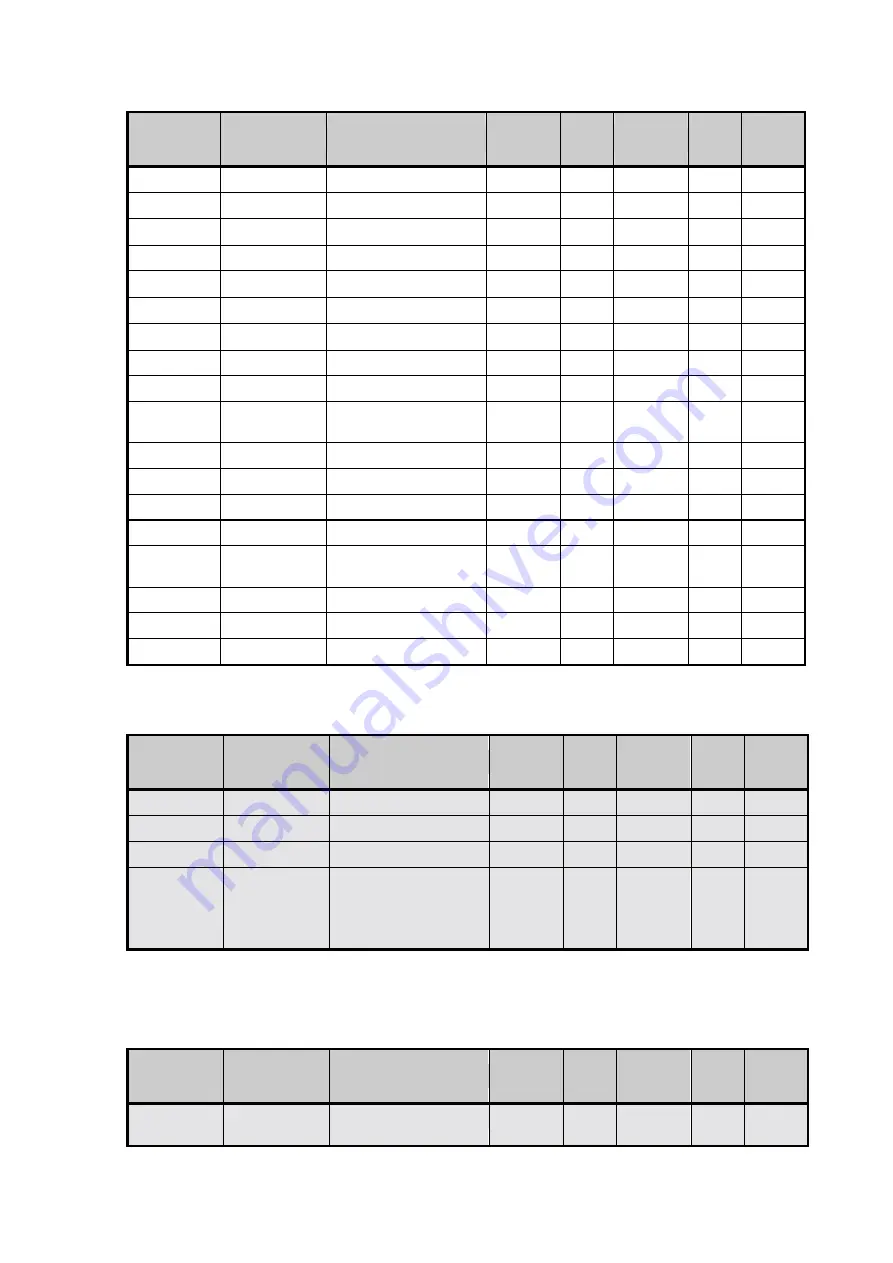
Communication P225/EN
CT/B11
MiCOM P225
Page 29/52
Address
Group
Description
Values
range
Step
Unit
Format
Default
value
037D
t RTD6 TRIP time delay
0 to 1000 1
1/10 sec
F1
0
037E
Thermistor 1 function
0-1
1
-
F24
0
037F
Thermistor 1 threshold
1-300
1
1/10 k
Ω
F1 1
0380
Thermistor 2 function
0-1
1
-
F24
0
0381
Thermistor 2 threshold
1-300
1
1/10 k
Ω
F1 1
0382
Thermistor 3 function
0-1
1
-
F24
0
0383
Thermistor 3 threshold
1-300
1
1/10 k
Ω
F1 1
0384
RTD7
function 0-1
1
- F24
0
0385
RTD7
ALARM
threshold
0-200
1
°C F1
0
0386
t RTD7 ALARM time
delay
0 to 1000 1
1/10 sec
F1
0
0387
RTD7 TRIP threshold
0-200
1
°C
F1
0
0388
t RTD7 TRIP time delay
0 to 1000 1
1/10 sec
F1
0
0389
RTD8
function 0-1
1
- F24
0
038A
RTD8
ALARM
threshold
0-200
1
°C F1
0
038B
t RTD8 ALARM time
delay
0 to 1000 1
1/10 sec
F1
0
038C
RTD8 TRIP threshold
0-200
1
°C
F1
0
038D
t RTD8 TRIP time delay
0 to 1000 1
1/10 sec
F1
0
038E to 038F
Reserved
-
1.8.6
Page 4 : Remote controls
Access in writing
Address
Group
Description
Values
range
Step
Unit
Format
Default
value
0400
Remote control Remote control word 1
0 to 31
1
-
F9
0
0401 à 0402
Reserved
0403
Remote control word 3
0-1
1
-
F9’
0
0404
Remote control word 2
Remote control of the
output relays – under
Maintenance mode only
0 to 63
1
-
F38
0
1.8.7
Pages 5 and 6 : Reserved
1.8.8
Page 7 : MiCOM P225 relay status word
Access for quick reading
Address
Group
Description
Values
range
Step
Unit
Format
Default
value
0700
Quick reading
byte
Quick reading byte
1
-
F23
0
Summary of Contents for MiCOM P225
Page 1: ...MiCOM P225 Motor Protection Relay Technical Guide P225 EN T B11...
Page 2: ......
Page 4: ...P225 EN T B11 Technical Guide Page 2 2 MiCOM P225 BLANK PAGE...
Page 5: ...Connection Diagrams P225 EN CO B11 MiCOM P225 CONNECTION DIAGRAMS...
Page 6: ......
Page 8: ...P225 EN CO B11 Connection Diagrams Page 2 12 MiCOM P225 BLANK PAGE...
Page 18: ...P225 EN CO B11 Connection Diagrams Page 12 12 MiCOM P225 BLANK PAGE...
Page 19: ...Technical Specifications P225 EN TD B11 MiCOM P225 TECHNICAL SPECIFICATIONS...
Page 20: ......
Page 55: ...User Guide P225 EN FT B11 MiCOM P225 USER GUIDE...
Page 56: ......
Page 109: ...Menu of the HMI P225 EN HI B11 MiCOM P225 MENU OF THE HMI...
Page 110: ......
Page 158: ...P225 EN HI B11 Menu of the HMI Page 48 48 MiCOM P225 BLANK PAGE...
Page 159: ...Maintenance P225 EN CM B11 MiCOM P225 MAINTENANCE...
Page 160: ......
Page 162: ...P225 EN CM B11 Maintenance Page 2 18 MiCOM P225 BLANK PAGE...
Page 178: ...P225 EN CM B11 Maintenance Page 18 18 MiCOM P225 PAGE BLANCHE...
Page 179: ...Communication P225 EN CT B11 MiCOM P225 COMMUNICATION...
Page 180: ......
Page 232: ...P225 EN CT B11 Communication Page 52 52 MiCOM P225 BLANK PAGE...
Page 233: ...Setting P225 EN SV B11 MiCOM P225 SETTING...
Page 234: ......
Page 250: ...P225 EN SV B11 Setting Page 16 16 MiCOM P225 BLANK PAGE...
Page 251: ...Installation Guide P225 EN IN B11 MiCOM P225 INSTALLATION GUIDE...
Page 252: ......
Page 254: ...P225 EN IN B11 Installation Guide Page 2 12 MiCOM P225 BLANK PAGE...
Page 265: ...Test Report P225 EN RS B11 MiCOM P225 TEST REPORT...
Page 266: ......
Page 268: ...P225 EN RS B11 Test Report Page 2 20 MiCOM P225 BLANK PAGE...
Page 287: ......