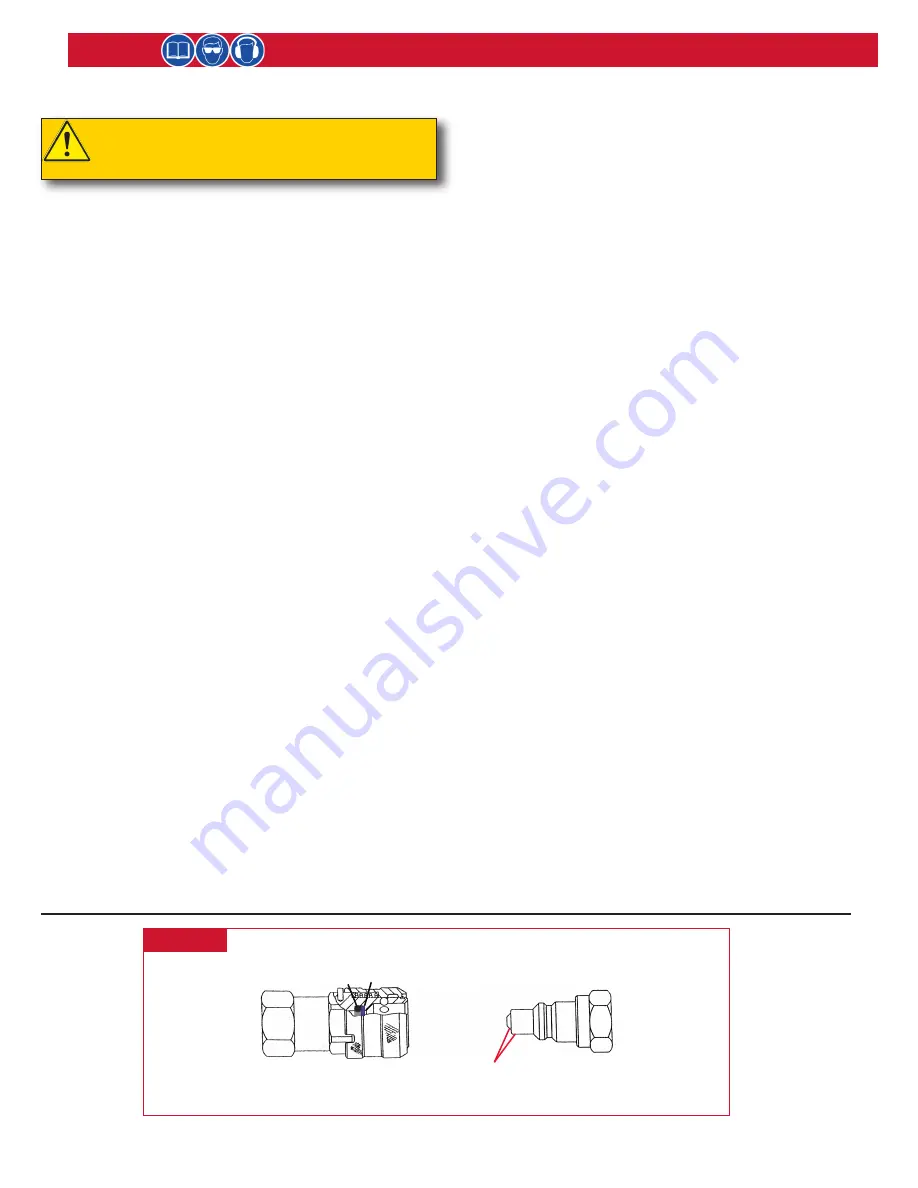
2480 & 2481 series Hydraulic Installation Tools (HK970)
9
Maintenance
GOOD SERVICE PRACTICES
The efficiency and life of an installation tool depends upon
proper maintenance and good service practices. Read this
entire page before proceeding with maintenance/repair.
Individual parts must be handled carefully and examined
for damage or wear. Replace parts where required. Always
replace O-rings and back-up rings when the tool is
disassembled for any reason.
Use proper hand tools in a clean well lit area for
maintenance and/or repair. Always be careful to keep dirt
and debris out of pneumatic and hydraulic systems. Only
standard hand tools are required in most cases. Where a
special tool is required, the description and part number
are given.
While clamping installation tool and/or parts in a vise, and
when parts require force, use suitable soft materials to
cushion impact. For example, using a half-inch brass drift,
wood block and/or vise with soft jaws greatly diminishes
the possibility of a damaged tool. Remove components in a
straight line without bending, cocking or undue force, and
reassemble tool with the same care.
Consult Troubleshooting section of this manual if a
malfunction occurs. Where a part number (P/N) is given,
HUCK sells that part.
FLUID MAINTENANCE
For fluid maintenance please refer to NAS 1638 class 9 or
ISO CODE 18/15 or SAE level 6
STANDARD SEALANTS AND LUBRICANTS
Coat hose fitting threads with a non-hardening TEFLON®
thread compound such as Threadmate™, which is available
from HUCK in a 4oz. tube as part number 508517.
Smear LUBRIPLATE® 130AA, or equivalent lubricant, on O-
rings and mating surfaces this prevents nicking/pinching
O-rings on any rough/tight spot and increases ease of
assembly. (LUBRIPLATE 130AA is available from HUCK in a
tube as part number 502723.)
SERVICE PARTS KIT
Service parts kit 2480KIT contains perishable parts for both
the 2480 and 2481 family of tools. For convenience, and as
experience indicates, keep extra kits (O-rings, back-up
rings, and other standard items) and tool parts on hand.
Inspect tool daily. Check hoses, fittings and disconnects for
leaks or damage.
Preventive Maintenance
SYSTEM INSPECTION
Operating efficiency of the tool is directly related to
performance of the complete system, including tool and
nose assembly, hydraulic hoses, control trigger assembly
and the Powerig® Hydraulic Unit. An effective preventive
maintenance program includes scheduled inspections of
the system to detect and correct minor troubles.
1. Inspect tool for external damage.
2. Verify that hoses and fittings, and trigger connections
are secure.
3. Inspect hydraulic hoses for signs of damage. Replace if
required.
4. Inspect tool, hoses, and Powerig Hydraulic Unit during
operation to detect abnormal heating, leaks or
vibration.
POWERIG® HYDRAULIC POWER SOURCE
Maintenance and repair instructions are in applicable
Powerig Hydraulic Unit Instruction Manual.
Tool and Nose Assembly Maintenance and Precautions
Whenever disassembled, and also at regular intervals
(depending on severity and length of use), replace all O-
rings and back-up rings. Spare Parts Kits should be kept on
hand. Inspect cylinder bore, piston and rod/extension, and
unloading valve for scored surfaces, excessive wear or
damage, and replace parts as necessary. On any assembly
with UNITIZED™ Jaws, clean all parts in mineral spirits or
isopropyl alcohol only. Under no circumstances should jaws
come in contact with other solvents. Also, do not let jaws
soak; dry the jaws immediately after cleaning. Dry other
parts before assembling. Urethane soaks up other solvents,
then swells up and becomes unusable. Use a sharp pointed
pick to remove embedded particles from the pull grooves
of the jaws.
CAUTION: Do not use TEFLON
®
tape on pipe
threads. Pipe threads may cause tape to shred
resulting in tool malfunction.
504438 O-ring
501102 Back-up Ring
110439
Female
Connector
110438
Male
Connector
Use a fine India stone to remove any nicks or burrs from
these areas to prevent damage to O-ring of Female Connector.
Figure 5