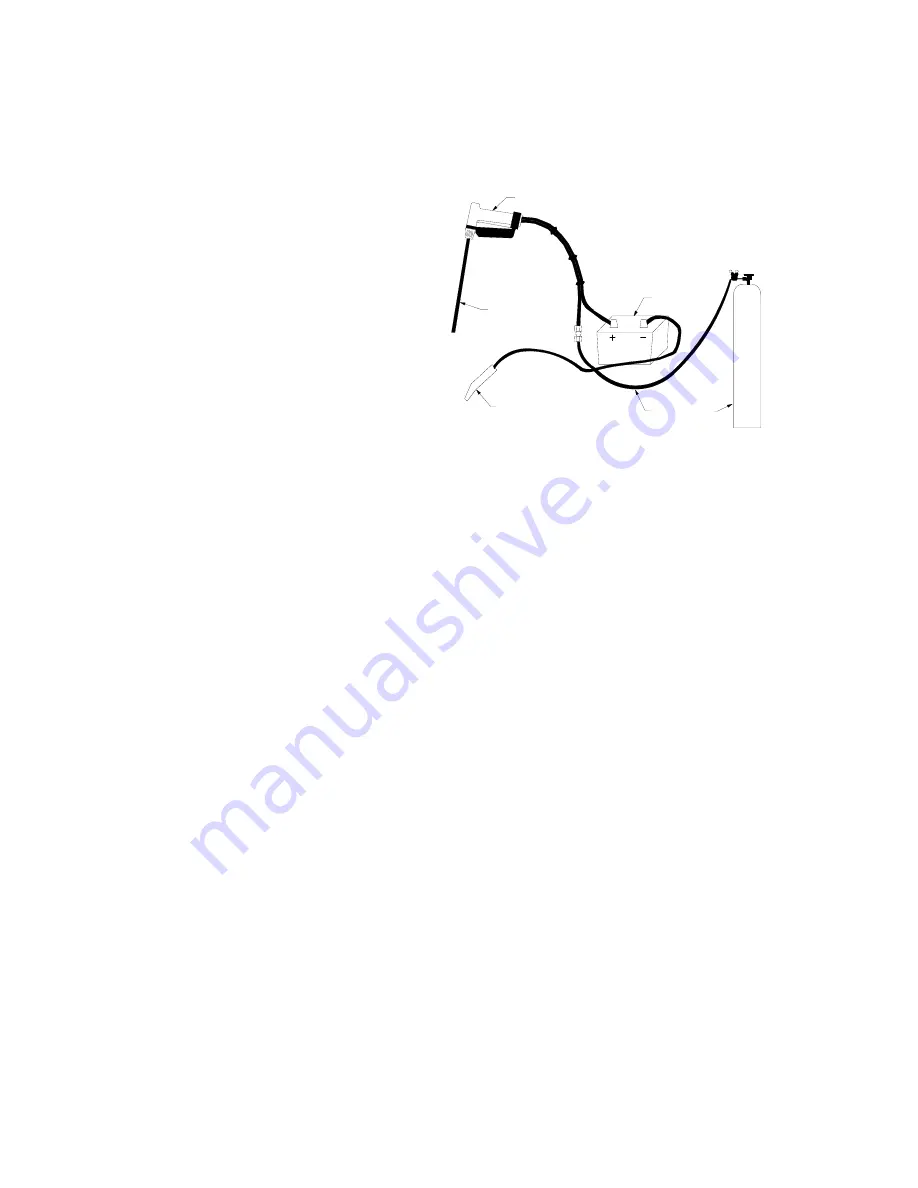
5
OPERATING
TECHNIQUES
Cutting Without Power
This is the most commonly used
method of cutting with this type of
equipment. To cut without power
connect the torch to either terminal of
a 12-volt battery or constant-current
welding power source. Connect the
striker or a strike plate to the other
terminal. If using a welding power
source, set output level for 100 amps.
Turn on the oxygen supply and adjust
the regulator to the proper working
pressure. Insert the cutting rod into
the collet and tighten the collet ring.
Tap the cutting rod on a hard,
ungrounded surface to seat the rod in
the torch. Depress the torch oxygen-
valve lever and check for oxygen
leaks around the collet ring. If
oxygen is leaking, repeat the
procedure until no oxygen is leaking.
Put the torch in one hand and striker
in the other. Depress the oxygen
lever and touch the cutting rod to the
striker. As soon as the rod is ignited,
remove the striker. Move the burning
rod to the workpiece and begin
cutting. The cutting rod should be
held at a 45
°
to 80
°
drag angle from
the workpiece surface. This angle
depends on the thickness and type of
material being cut. (See Section
"Important Process Variables",
Paragraph "Electrode-to-Work
Angle")
As the cut progresses, slight contact
should be made between the burning
rod tip and the workpiece. This
placement requires two motions: first,
inward towards the workpiece as the
rod is consumed, and second, in the
direction of the cut. Since there is no
electrical arc when cutting without
power, wear at least a #5 shade lens
for eye protection.
FIGURE 2 Cutting Without Power
Cutting With Power
Cutting with power or an electric arc
is done by connecting the torch to
one terminal and connecting a
welding ground clamp to the other
terminal of a CC welding power
source. The ground clamp is then
attached to the workpiece. Unlike
other processes, this process can use
a welding power source set for DCEP
(reverse polarity) or DCEN (straight
polarity). AC (alternating current)
power supplies can also be used
without affecting cutting performance.
Don't cut with power using a
constant-potential power source.
Insert the cutting rod into the collet
and tighten. Start the oxygen flow,
touch the rod tip to the workpiece,
and begin cutting. Again, as in
cutting without power, the cutting rod
should be held at a 45
°
to 80
°
drag
angle from the workpiece surface.
(See Section "Important Process
Variables", Paragraph "Electrode-to-
Work Angle") As the cut proceeds,
make slight contact between the
burning rod and the workpiece. This
placement requires two motions: first,
inward towards the workpiece as the
rod is consumed and, second, in the
12 VOLT BATTERY
(IGNITION SOURCE)
TORCH
STRIKER
CUTTING ROD
OXYGEN SUPPLY
1. CONNECT TORCH TO NEGATIVE LUG ON BATTERY.
2. CONNECT STRIKER TO POSITIVE LUG ON BATTERY.
3. SET OXYGEN PRESSURE TO 80 PSI.
4. TIGHTEN CUTTING ROD IN TORCH COLLET.
5. DEPRESS OXYGEN TRIGGER ON TORCH.
6. TOUCH CUTTING ROD TO STRIKER TO IGNITE ROD.
Summary of Contents for SLICE
Page 1: ...1 Instruction Manual For SLICE Exothermic Cutting Equipment...
Page 19: ......