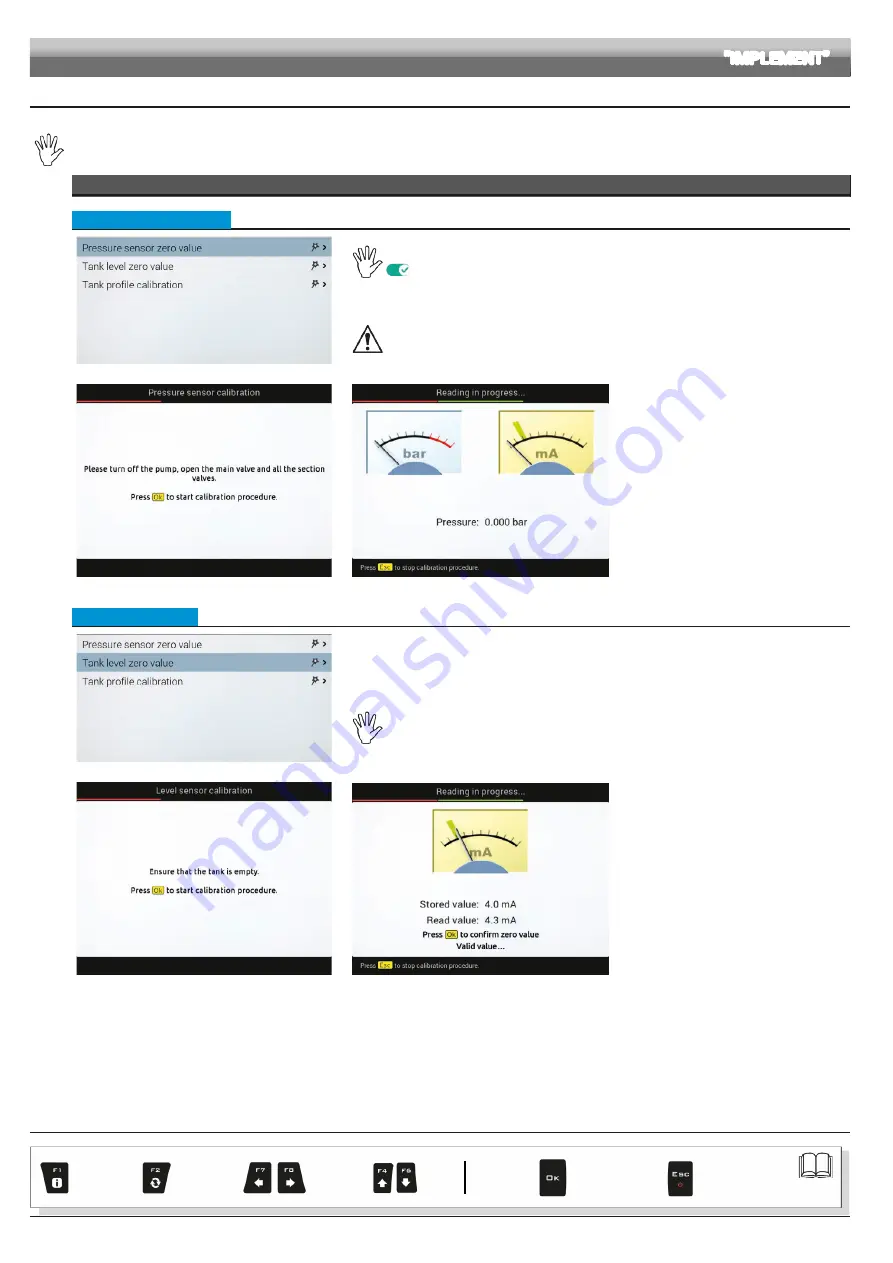
36
Exit the function
or data change
Confirm access
or data change
Scroll
(LEFT /
RIGHT)
Delete
selected
character
Data
decrease
of data
Scroll
(UP /
DOWN)
Enter
selected
character
Par.
11.4.12 Device calibration
Allows starting calibration for the devices connected to the monitor.
THE BASIC SETTINGS (CHAP. 10) AFFECT WHICH AND HOW MENU ITEMS ARE DISPLAYED, HENCE WHICH ADVANCED SETTING
IT IS POSSIBLE TO CONTROL.
SENSORS
• Pressure sensor zero value
Fig. 74
To access this menu, the pressure sensor must be enabled
(
, par. 11.4.4)
In case a pressure value other than zero is displayed
despite the absence of pressure inside the circuit
,
it is necessary to perform zero calibration of the sensor.
Before carrying out any operation disable the pump by disconnecting it from the power
supply.
Make sure that the pump is correctly disabled, then open the main valve and all section
valves.
Fig. 75
Fig. 76
1
Select
Pressure sensor zero value
(Fig. 74) and press
OK
.
2
The message in Fig. 75 is displayed: follow
the instructions, then start the procedure by
pressing
OK
.
3
Press
OK
to reset the pressure sensor
residual signal.
Value out of range!
If this alarm is displayed, faulty pressure
values have been detected: check the
sensor operation.
If the problem persists, check for residual
pressure in the system.
• Tank level zero value
Fig. 77
In these cases it is necessary to perform the level sensor zero adjustment.
1
The monitor displays the presence of fluid inside the tank,
even when it is empty
;
2
A tank profile has been loaded (par. 11.4.9).
To use this menu the level sensor must be active
(
Tank level source
, chap. 10). Perform the adjustment with empty tank
Fig. 78
Fig. 79
1
Select the item
Tank level zero value
(Fig.
77) and press
OK
.
2
The message in Fig. 78 is displayed: follow
the instructions, then start the procedure by
pressing
OK
.
3
Press
OK
to reset the level sensor residual
signal.
Value out of range!
If this alarm is displayed, faulty values have
been detected: check the sensor operation.
If problem persists, check for residual fluid
in the tank.
ADVANCED SETTINGS
"IMPLEMENT"
CONTINUES > > >