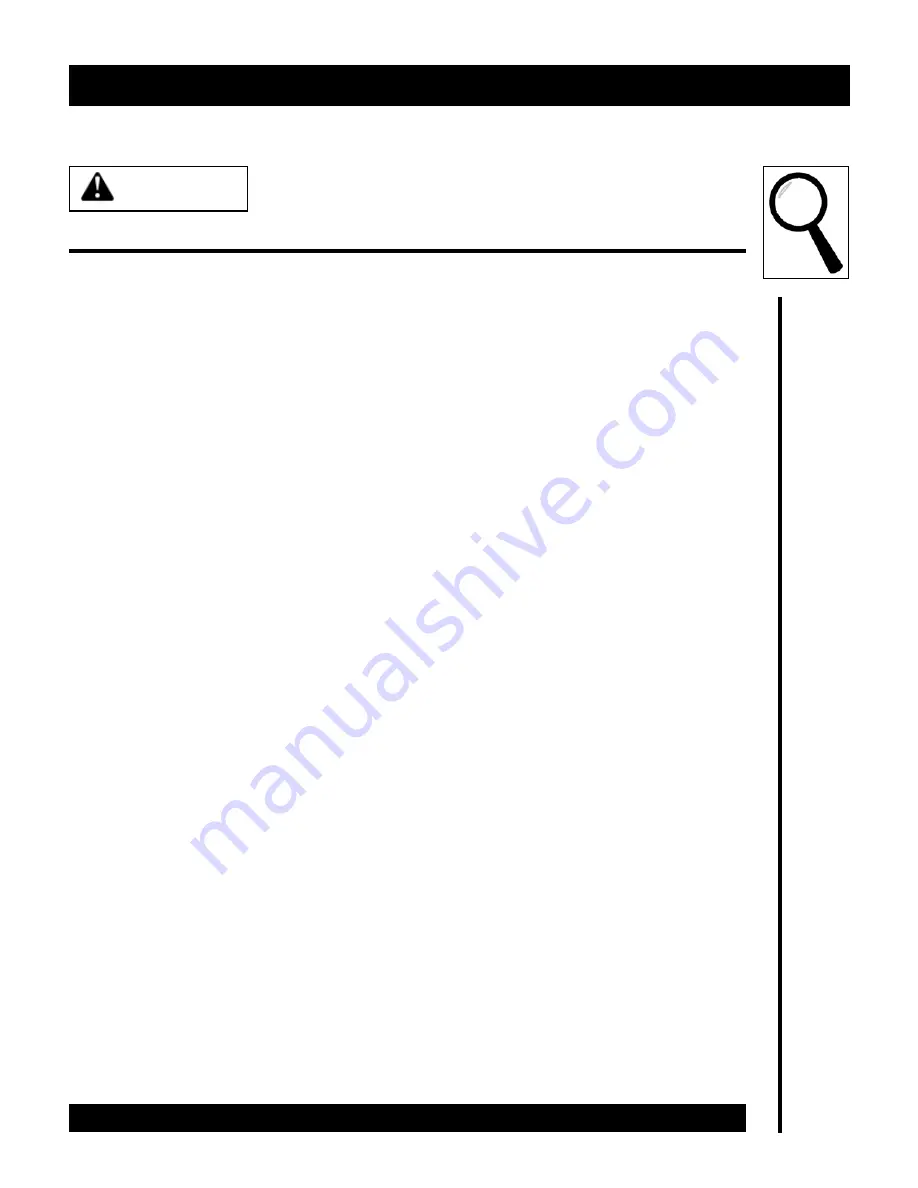
12
Contact Your Sales Representative for Further Assistance.
t
roubleShootinG
(
cont
.)
BEFORE INSPECTION AND /OR SERVICE,
DISCONNECT AND LOCK OUT POWER SOURCE.
WARNING
5. No Fog
A.)
The self-priming system will usually take about 10 seconds before you see fog output.
Check to see if the flow control valve is open. The valve is open when the handle is down.
B.)
Check the pre-set flow rate valve located inside the tank (refer to page 6 Factory
Pre-set Flow Valve). Having the pre-set flow rate valve in either a fully closed or fully open
position will result in no fog output. If the positioning is incorrect, refer to
page 6
for
instructions on calibrating the pre-set flow rate valve.
C.)
Check for sediment clogs. Flush the inline strainer and check for sediment build-up
around the base of the pump. Spray around the pump with a hose and drain the tank.
D.)
The pump may not be operating. Check by removing the Inline strainer cap and turning
system On. If no fluid flows from the strainer, the pump may need to be replaced.
6. Poor Quality Fog
A.)
The liquid feed tube (Part #575) may not be properly positioned. The feed tube is located
behind the blade assembly and should be inserted approximately 1/4" into the slot
between the motor shaft and the stainless steel face plate. Centered in the slot area and
aimed slightly downward, free from any rotational contact.
B.)
Liquid not traveling through the fan blades. This can be diagnosed by viewing the back
of a blade assembly during operation (using a bright flashlight). If system is clogged,
liquid can be seen spinning out of the slot area between the motor shaft and stainless
steel face plate (Part #573). If confirmed, replace fan blade assembly (Part #571-assy).
Cleaning the internal passageways of a blade assembly is feasible with the aid of some
speciality
tools.
7. Unusual Noise
Squealing at start-up or during operation may be caused by the motor shaft's bearing seal.
Spray with lubricant at the front of the motor where the shaft exits the motor's frame.
8. Fan Motor Becomes Excessively Hot
The main fan motor normally becomes very hot to the touch. However, it should not get so
hot that it begins to smell or smoke, nor should the power cord become hot. Discontinue
operation and consult an electrician to properly evaluate the problem.
9. Electrical Breaker Tripping
If the electrical breaker trips off, there is an overload in the system and there may be a
serious motor problem. Turn off all other devices connected to the same circuit. If the
breaker continues to trip, the motor is probably in need of repair. Consult an electrician for
evaluation.