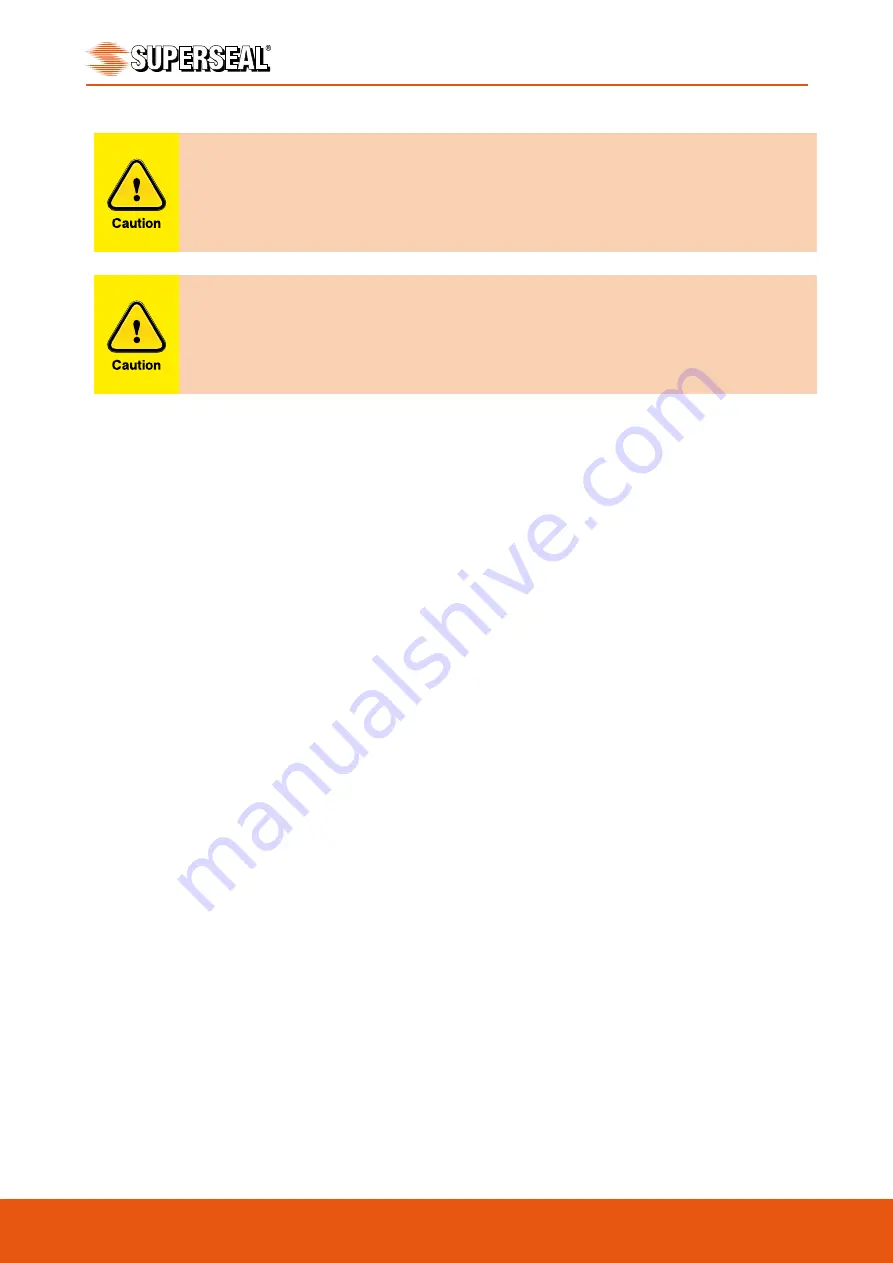
Australian Pipeline Valve - Installation, Operation and Maintenance Manual
6
LINED BUTTERFLY VALVES - MODEL 2014 & 2016 SERIES
13. Lever-lock handles are not recommended for use on 200 NB (8”) and larger valves unless very low
pressures.
3 . 0 G E N E R A L I N S T A L L A T I O N
1. Make sure the pipeline and pipe flange faces are clean. Any foreign material such as pipe scale, metal
chips, welding slag, welding rods, etc., can obstruct disc movement or damage the disc or seat.
2. Elastomer seats often have integral moulded O-ring ribs on the face of the seat (where required in
harder compunds). As a result, no gaskets are required as these O-ribs serve the function of a gasket.
Softer rubber compounds do not have integral moulded O-rings but do not require them due to the
pressure rating of valve.
3. Align the piping and then spread the pipe flanges a distance apart so as to permit the valve body to
be easily dropped between the flanges without contacting the pipe flanges (see Figure 4).
4. Check to see that the valve disc has been positioned to a partially open position with the disc edge
about 6.3 mm to 9.5 mm from the face of the seat, approximately 10° open (see Figure 4).
5. Insert the valve between the flanges as shown below, taking care not to damage the seat faces.
Always pick the valve up by the locating holes or by using a nylon sling on the neck of the body. Never
pick up the valve by the actuator or operator mounted on the top of the valve.
6. Place the valve between the flanges, centre it, and then span the valve body with all flange bolts, but
do not tighten the bolts, Carefully open the disc to the full open position, making sure the disc does
not hit the adjacent pipe I.D. Now systematically remove jack bolts or other flange spreaders and hand
tighten the flange bolts as shown in Figure 7. Very slowly close the valve disc to ensure disc edge
clearance from adjacent pipe flange I.D. now open the disc to full open and tighten all flange bolts per
specification as shown in Figure 6. Finally, repeat a full close to full open rotation of the disc to ensure
proper.
7. 2014 and 2016 series butterfly valves are bi-directional.
8. Superseal butterfly valves are designed to operate between two flanges. For ‘dead end service’ a
lugged style valve is recommended. The valve should still be placed between two flanges, except the
end flange should be an open flange not a blind. Otherwise a special dead end service design valve is
required.
Lined valves are not recommended for steam service or for service where a firesafe
valve is required.
Do not install EPDM liner in compressed air lines or in lines containing any
hydrocarbons. Viton liners are not recommended for hot water.