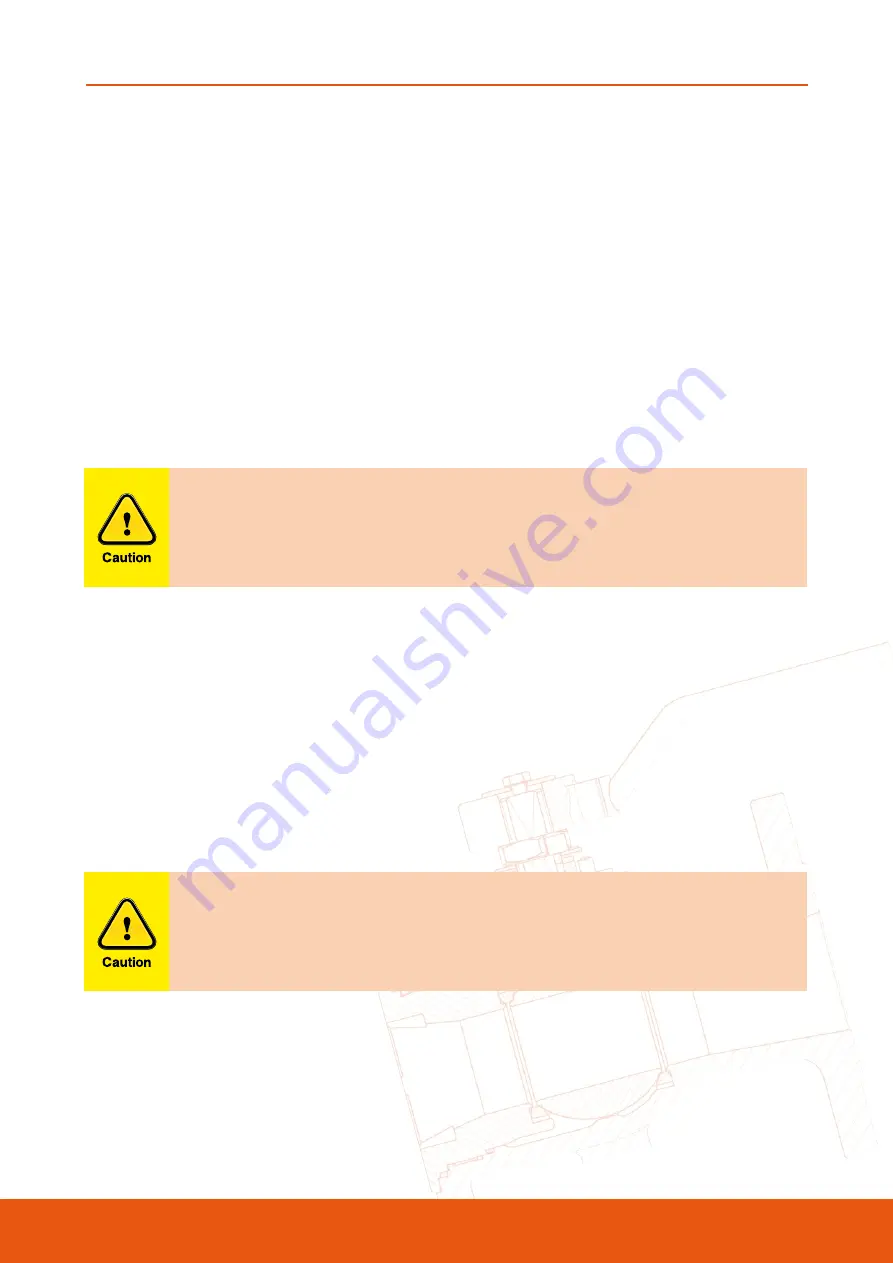
Australian Pipeline Valve - Installation, Operation and Maintenance Manual
7
FLOATING BALL VALVES - SLFSBV02 & SLBV02 SERIES
2.1 INSTALLATION POSITIONS
Ball valves are usually bi-directional, and therefore may be installed in either direction. In some cases,
ball valves such as metal to metal seated and low temperature valves may be unidirectional, in which
case the direction of flow will be indicated on the valve body.
2.2 PREPARATION FOR INSTALLATION
• Remove protective end caps or plugs and inspect valve ends for damage to threads, weld ends or
flange faces.
• Thoroughly clean adjacent piping system to remove any foreign material that could cause damage to
seating surfaces during valve operation.
• Verify that the space available for installation is adequate to allow the valve to be installed and to be
operated.
Ensure sufficient clearance for the stem in the full open position. Inadequate
clearance for valves may add mechanical loading to the valve ends.
2.3 END CONNECTIONS
2.3.1 Threaded Ends
Check condition of threads on mating pipe. Apply joint compound to the male end of joint only. This will
prevent compound from entering the valve flowpath.
2.3.2 Flanged Ends
Check to see that mating flanges are dimensionally compatible with the flanges on the valve body ensure
sealing surfaces are free of debris. Install the correct studs and nuts for the application and place the
gasket between the flange facings.
Stud nuts should be tightened in an opposing criss-cross pattern in equal increments
to ensure even gasket compression.
The responsibility for welding of the valves into piping systems is that of those performing the welding.
Refer to ASME B31.1, B31.3 etc. Written welding procedures covering all attributes of the process and
materials to be welded shall be in accordance with Section IX of the ASME Boiler and Pressure Vessel Code
and any additional requirements from the applicable piping code including any possible necessary
localised post weld heat treatment depending on material specifications.