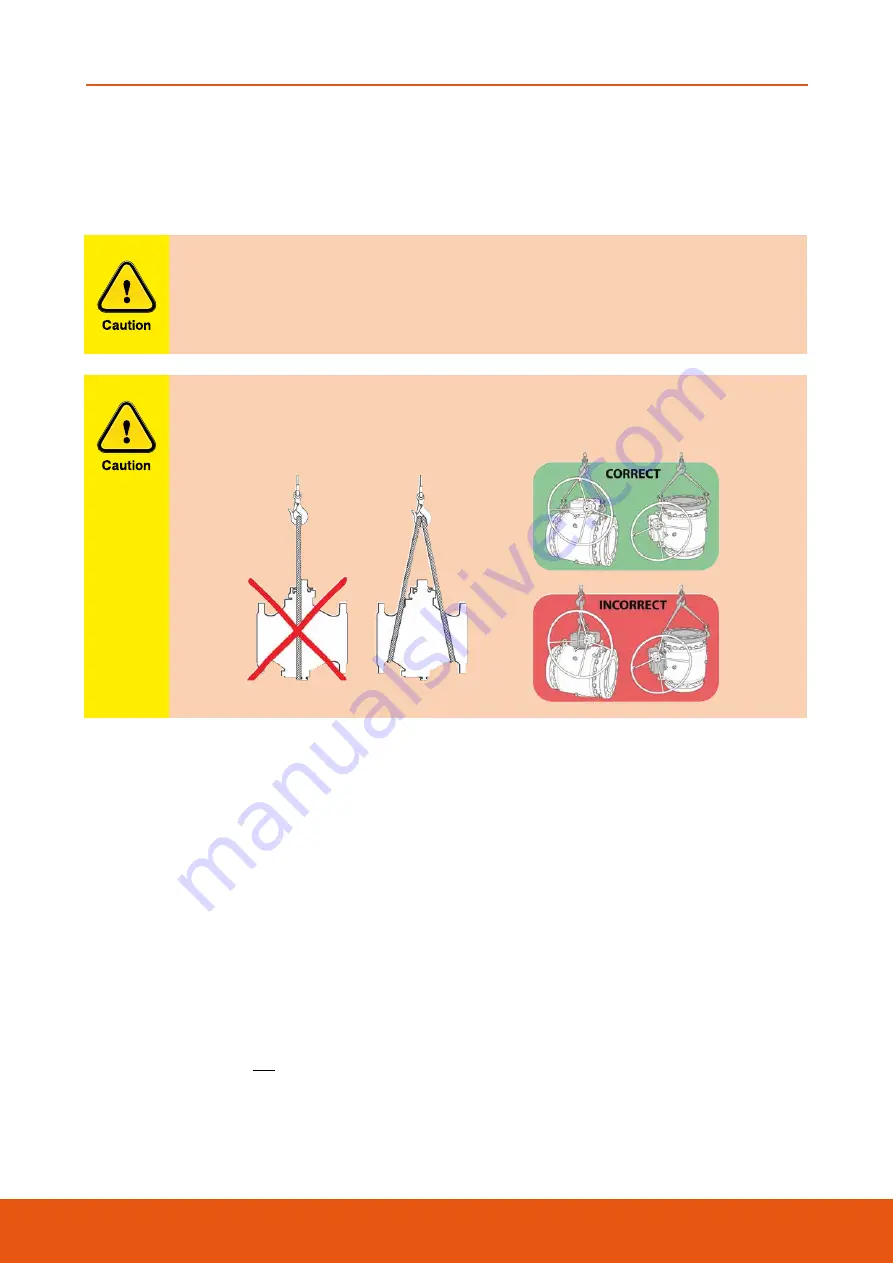
f- Plug valves are usually bi-directional, and therefore may be installed in either direction. In some cases,
ball valves such as ‘metal to metal’ and low temperature valves may be unidirectional, in which case
the direction of flow will be indicated on the valve body.
2.3 MAINTENANCE PRIOR TO FLUSHING
a- If the period between installation and flushing of the of the pipeline is longer than six months a
preventative maintenance operation is suggested.
• Lubricate the stem with fluid protective oil through the stem injector (if applicable). Do not grease
lubricate seats as grease may attract debris and damage seats.
• Remove valve from line and remove any debris and reflush.
2.4 FLUSHING THE PIPELINE
Flushing washes away all welding slag, dirt, sand, solids and debris collected in the pipelines during
construction prior to turning the valve and potentially damaging the seat. Flushing where deemed
necessary is the most dangerous activity for the valve, and it happens before they are put into service.
Ball valves are normally not lubricated, however, should it be required to flush potential debris (or
lubricate sticky valves) a different practise to the lubrication of either a gate valve or plug valve should
be employed. We recommend the following: -
1. Find a good grease for natural gas or your service. The grease must be insoluble. It must be resistant to
Australian Pipeline Valve - Installation, Operation and Maintenance Manual
10
EXPANDING SEAL PLUG VALVE DOUBLE BLOCK & BLEED API6D - TWIN SERIES
Local safety regulations must be complied with for transport to the place of
installation. Make sure that the valves cannot tilt or slip in any way (see figure
below).
If the ball valve is equipped with a test connection port, make sure that it is fully
closed before pressurising the valve.