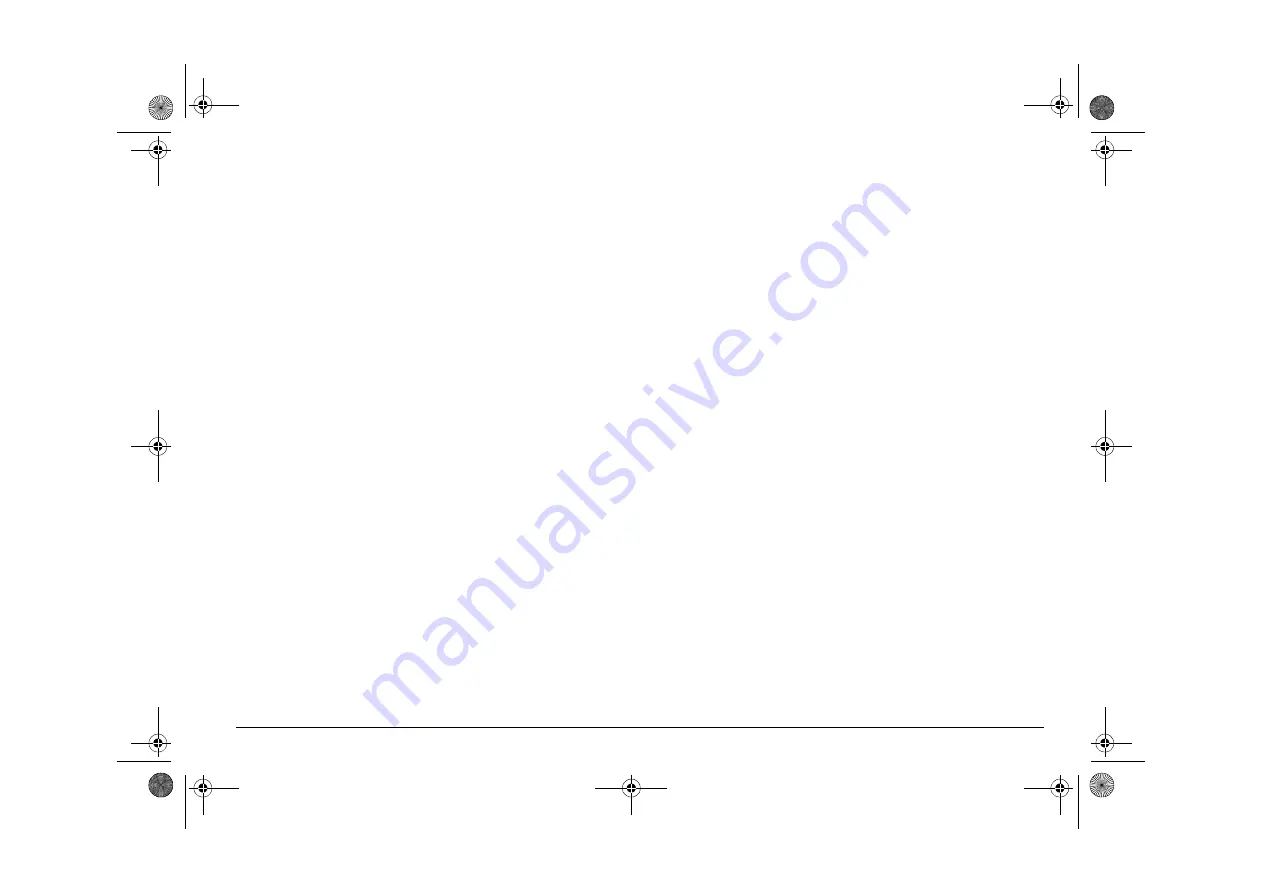
93
use and maintenance RSV mille Sport Production
TRANSMISSION
Type .......................................................................
mechanical, 6 gears with foot control on the left side of the engine
GEAR RATIOS
Ratio
Primary
Secondary
1
st
31/60 = 1 : 1.935
14/35 = 1 : 2.500
2
nd
16/28 = 1 : 1.750
3
rd
19/26 = 1 : 1.368
4
th
22/24 = 1 : 1.090
5
th
23/22 = 1 : 0.956
6
th
27/23 = 1 : 0.851
Final ratio
Total ratio
17 / 42 = 1 : 2.470
11,948
8,368
6,543
5,216
4,573
4,073
DRIVE CHAIN
Type .......................................................................
endless (with no connection link) with sealed links
Model .....................................................................
525
FUEL SUPPLY
SYSTEM
Type .......................................................................
electronic injection (Multipoint)
Choke.....................................................................
Ø 51 mm
FUEL SUPPLY
Fuel ........................................................................
premium grade unleaded petrol, min. O.N. 95 (N.O.R.M.) and 85 (N.O.M.M.).
FRAME
Type .......................................................................
double two-beam frame with light alloy cast elements and extruded elements
Steering inclination angle.......................................
24.2 °
Fore stroke.............................................................
95 mm
SUSPENSIONS
Front.......................................................................
upside-down telescopic adjustable fork with hydraulic operation, rod Ø 43 mm
Stroke.....................................................................
125 mm
Rear .......................................................................
light-alloy, oscillating rear fork with extruded arms and hydropneumatic adju-
stable mono-shock absorber
Wheel stroke ..........................................................
130 mm
BRAKES
Front.......................................................................
with double floating disc - Ø 320 mm, calipers with four pins with differenti-
ated diameter
Rear .......................................................................
disc brake - Ø 220 mm, caliper with double pin
WHEEL RIMS
Type .......................................................................
in light alloy with withdrawable pin
Front.......................................................................
3.50 x 17”
Rear .......................................................................
6.00 x 17”
FRONT TYRE
Type .......................................................................
120 / 70 ZR - 17
"
; 120 / 65 2R -17
"
Model .....................................................................
PIRELLI DRAGON EVO MTR21 CORSA
– Alternative ...........................................................
PIRELLI MTR 01A
Inflation pressure solo rider....................................
230 kPa (2,3 bar)
Ing-02.fm Page 93 Thursday, December 16, 1999 5:21 PM