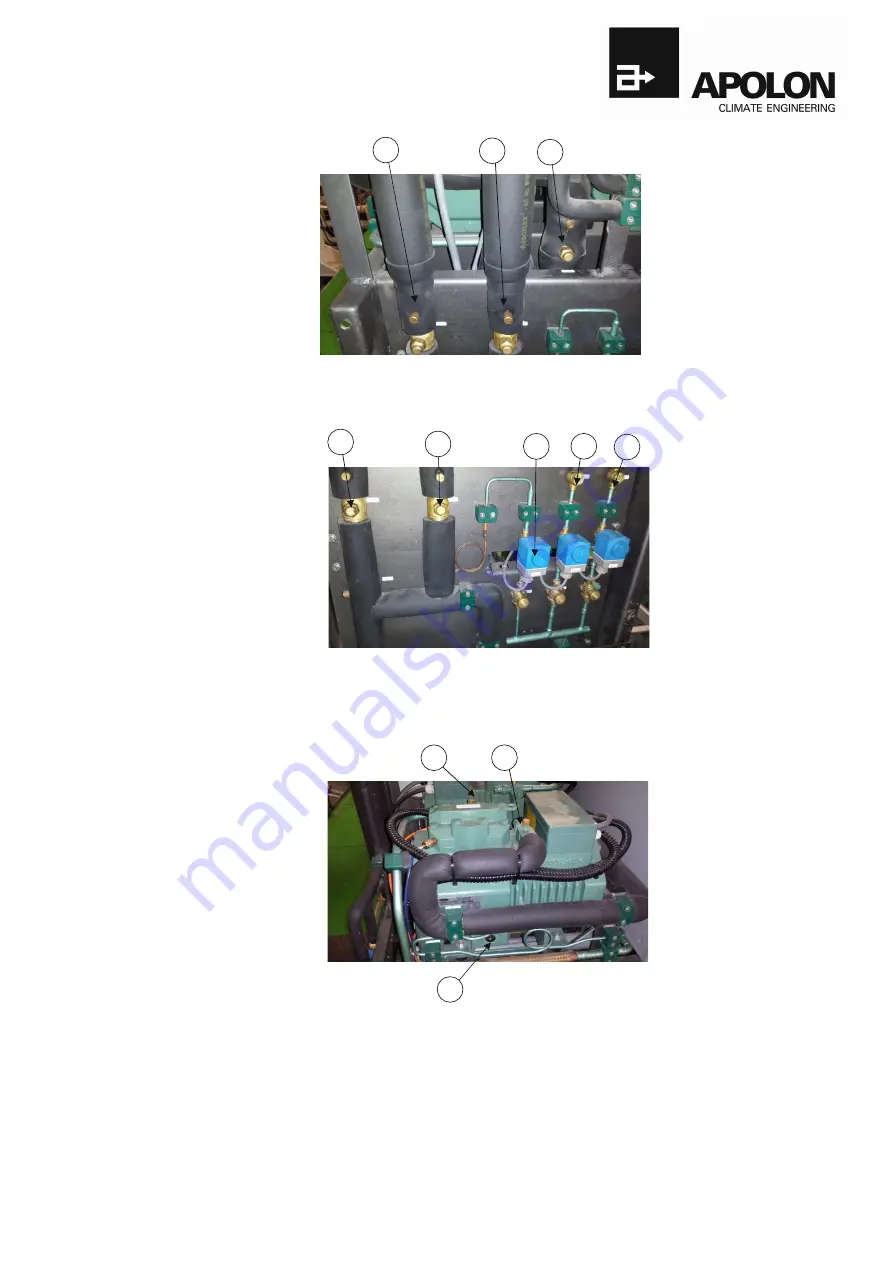
Operation manual RCWC-04D11
OM-RCWC-04D11
2014 7
11.
Ball valve gas pipe cooler (V11)
12.
Ball valve gas pipe freezer (V10)
13.
Ball valve gas pipe compressor 2 (V6)
14.
Ball valve gas pipe cooler (V11)
15.
Ball valve gas pipe freezer (V10)
16.
Liquid injection solenoid (EV3 + V7)
17.
Liquid cooler ball valve+ssight glass (EV2+V8+SG2)
18.
Liquid freezer ball valve+ssight glass (EV1+V9+SG1)
19.
Suction rottalock valve
20.
Discharge rottalock valve
21.
Compressor oil sight glass
11
12
13
14
15
16
17
18
19
20
21