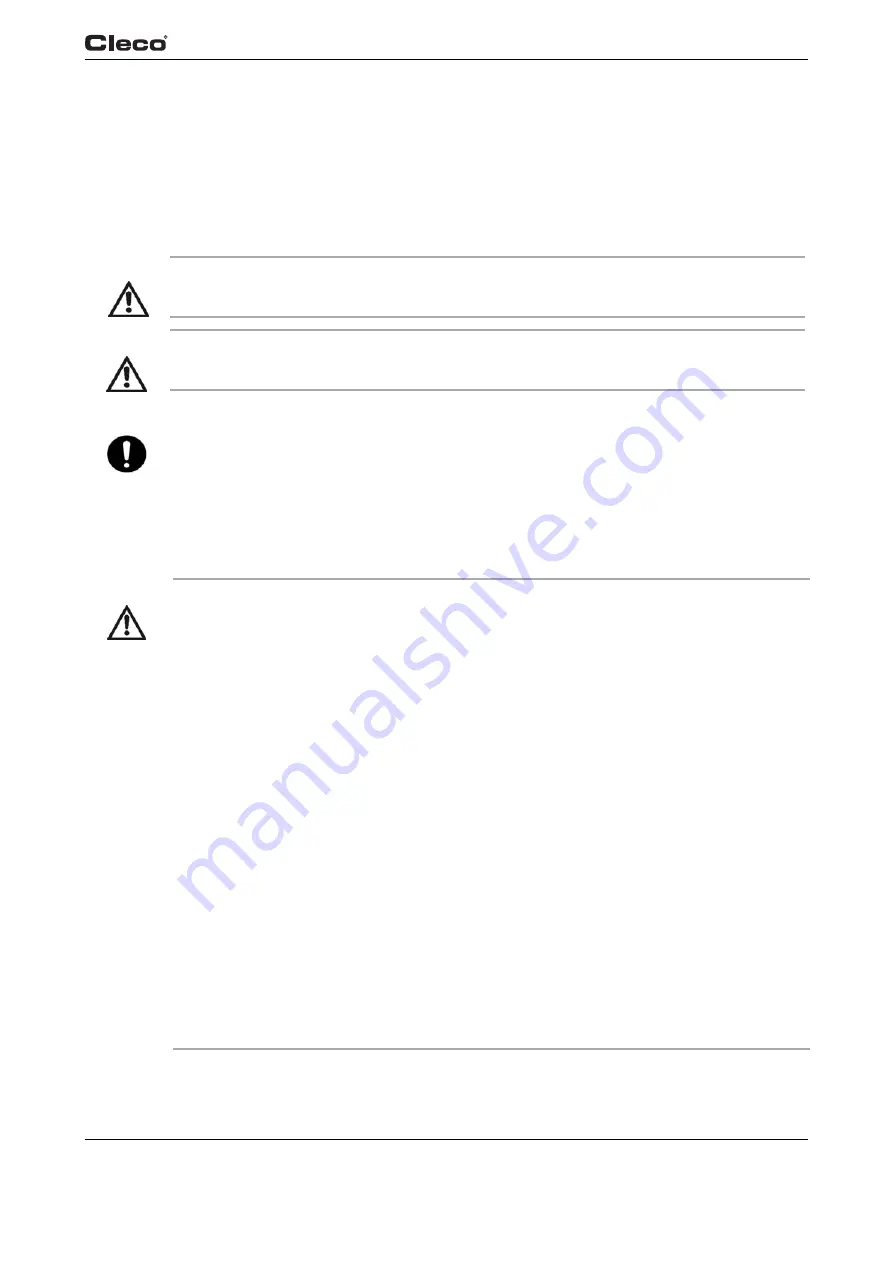
1994b_1_5_en-bedingt.fm, 11.06.2014
P1994BA/EN 2014-06
5
Safety
1
1
Safety
1.1
Warnings and notes
Warning notes are identified by a signal word and a pictogram:
•
The signal word describes the severity and the probability of the impending danger.
•
The pictogram describes the type of danger.
1.2
Basic requirements for safe working practices
All instructions must be read carefully. Failure to observe the instructions listed below can result in serious
injuries.
WARNING!
Potentially hazardous
situation for health and safety.
If this warning is not observed, death or serious injury may occur.
CAUTION!
Potentially hazardous
situation to health and safety, or risk of material and environmental damage. If this
warning is not observed, injuries or damage to materials or the environmental could occur.
NOTE
General notes
include application tips and particularly useful information but no hazard warnings.
CAUTION!
Work with a maximum working pressure of 101.5 psi (700 kPa) (measured at the air inlet tube of the
tool).
Before initial operation, check that the suspension bail is properly fastened to the balancer.
55PHHA: Before using the air inlet from above, make sure that the pipe plug is correctly fitted in the
lower air inlet.
If you hear unusual noises or vibrations, switch off the tool immediately.
Cut off the air supply immediately.
Before carrying out repairs, adjusting the torque or replacing screw bits, disconnect the tool from the
compressed air line.
The compressed air line must be depressurized before disconnecting it.
Never use the air hose to hold, raise or lower the tool.
Air hoses, the suspension bail and fittings must be regularly checked for damage and wear. Renew as
necessary.
Always carry out assembly according to Chapter 8 Spare parts, page 25.
Use only accessory parts authorized by Apex Tool Group (see product catalog).
Only use screw bits for machine-controlled fastening tools.
Make sure that the screw bits are securely inserted.
Inspect screw bits for visible damage and cracks.
Renew damaged bits immediately.
The operation, maintenance and repair conditions set forth in the instruction manual must be observed.
Follow generally valid and local safety and accident prevention rules.