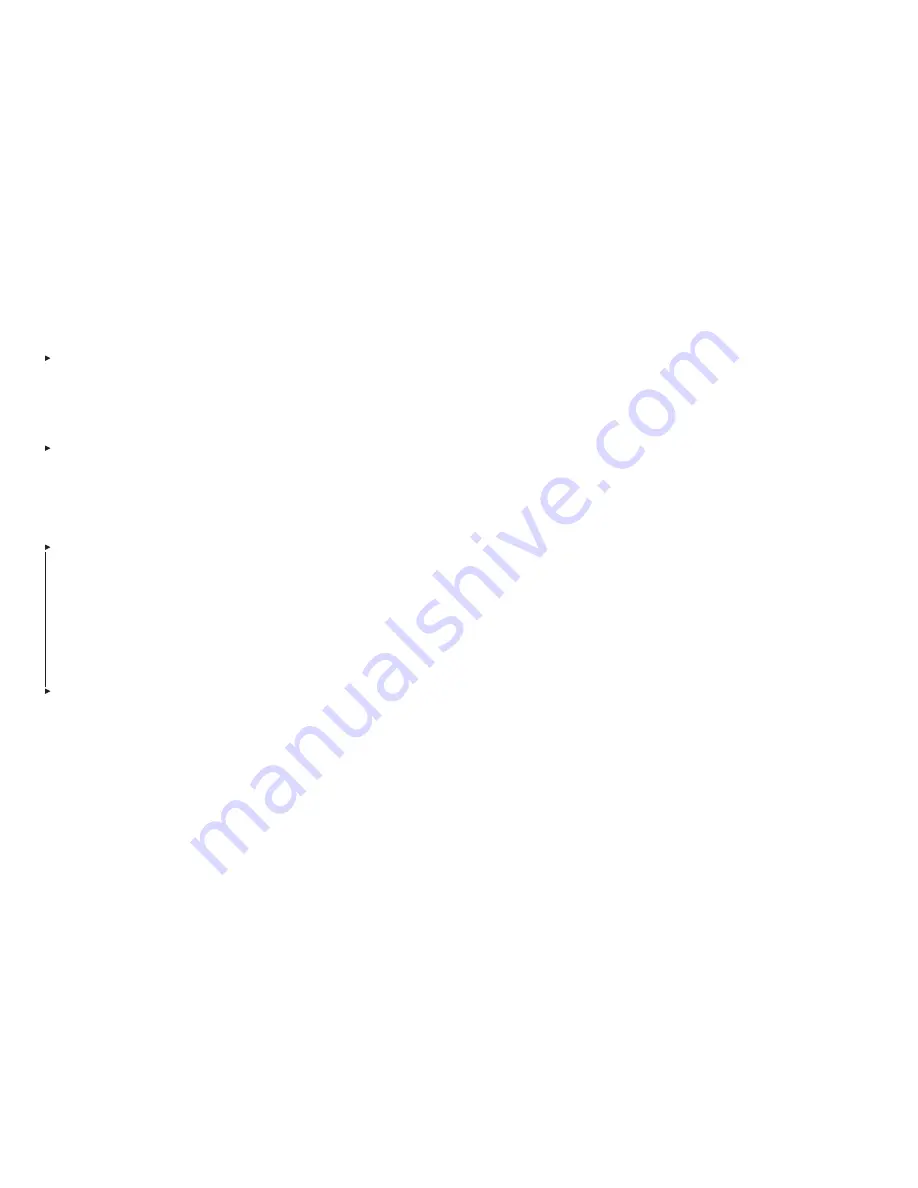
MAINTENANCE INSTRUCTIONS
7-1-07
Page 14
REV. 1
9
MAINTENANCE INSTRUCTIONS
9.1 SCOPE
This chapter deals with preventive maintenance, describes possible faults in detector operation and indicates corrective measures.
Ignoring these instructions may cause problems with the detector and may invalidate the warranty. Whenever a unit requires service,
please contact the manufacturer or its authorized distributor for assistance.
9.2 MAINTENANCE INSTRUMENTATION AND PERSONNEL
The detectors’ maintenance requires ordinary tools and qualified personnel who should be familiar with local codes and practices.
9.3 PREVENTIVE MAINTENANCE PROCEDURES
The detector must be kept as clean as possible. The viewing window and the reflector of the Model 20/20MI-32-S-F Flame Detector
must be cleaned on a periodic basis. The frequency of cleaning operations depends upon the environmental conditions and specific
applications. The fire detection system designer will give recommendations.
1. Disconnect power to the detector before proceeding with any maintenance including lens cleaning.
2. To clean the detector viewing window and reflector, use water and detergent, rinse with clean water.
NOTE: Do not use high
pressure wash to clean detectors and connectors of cabling system.
3. Where dust, dirt, or moisture accumulate on the window, clean first with a soft optical cloth and detergent, then rinse with clean
water.
9.4 PERIODIC MAINTENANCE PROCEDURES
9.4.1 Disconnect detector and interconnect cable connections and inspect for any debris such as dirt, moisture, other contaminents,
or corrosion inside the connectors. If there is any debris present, clean with electrical contact cleaner and re-apply electrical
insulating paste (such as Dow Corning #4) to the connections. If corrosion is present, replace effected components. Before
reconnecting cables, make certain insulating paste is present. If not, re-apply.
9.4.2 Reconnect all detection and cable interconnections. Then perform a manual/automatic built-in test for each optical flame
detector in the system. Refer to Manual/Automatic Built-In Test (BIT) Instructions, 3.4, Page 8, and Power-Up/Functional
Testing Procedure, 8.2, Page 13.
Note:
The power-up/functional testing procedure will initiate the manual/automatic BIT in the detectors. Disconnect power and
re-apply power for each detector to be checked.
9.5 MAINTENANCE RECORDS
It is recommended that maintenance operations performed on a detector be recorded in the system Logbook. The record should
include information which identifies the unit, the installation date, contractor, and entries including the description of the operation,
date and personnel ID for each maintenance operation performed. If a unit is sent to the manufacturer or distributor for service, a
copy of the Maintenance records should accompany it.
9.6 TROUBLESHOOTING
9.6.1 Fault Indication
1. Check power supply for correct voltage, polarity and wiring.
2. Check detector window and reflector for cleanliness. If necessary, clean the window as indicated in paragraph 9.3 above
and repeat the test.
9.6.2 False Alarm or Warning Indication
1. Disconnect the power supply from the system and check wiring.
2. Reconnect power supply and wait approximately 60 seconds. If indication remains, the unit requires service.