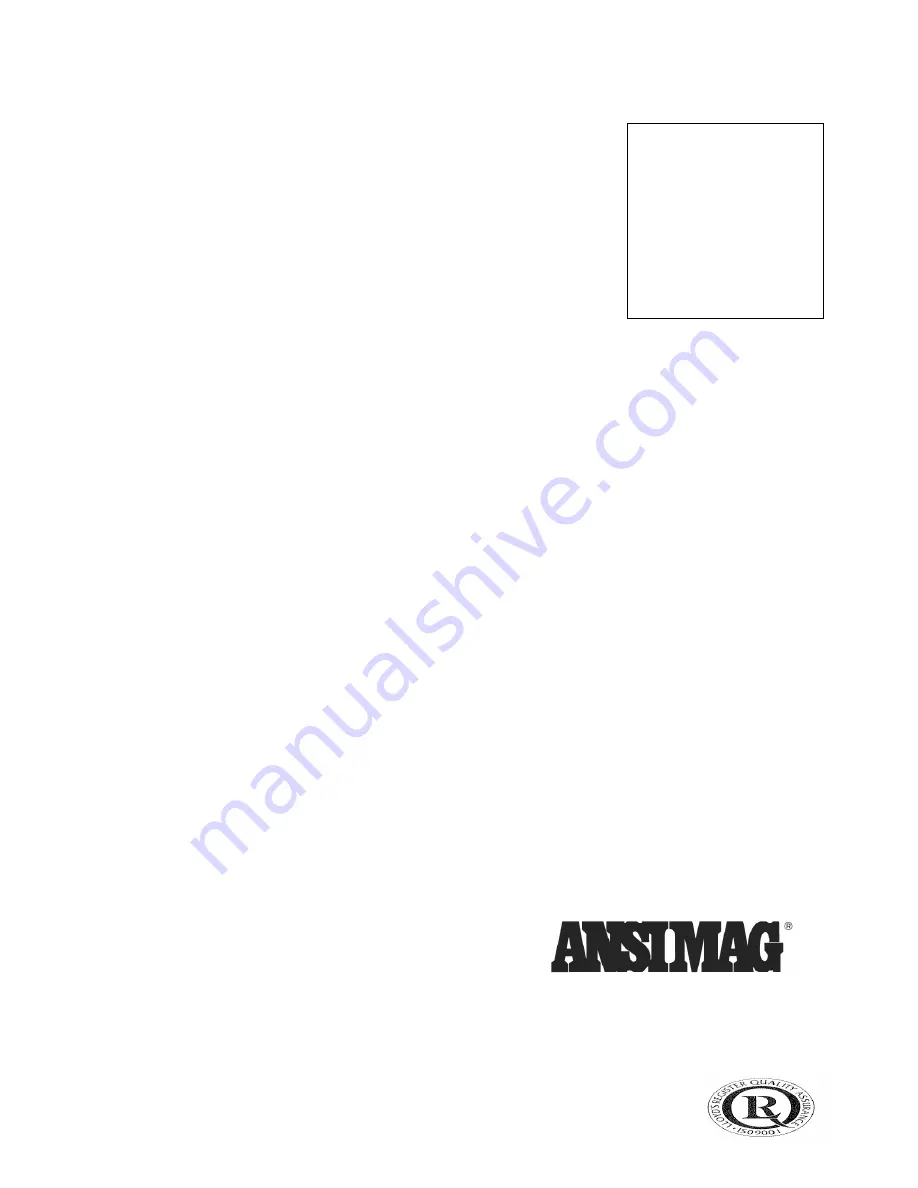
Sundyne Corporation is ISO 9001-2000 compliant is certified by Lloyd’s Register Quality Assurance Limited.
INSTALLATION &
MAINTENANCE MANUAL
K+
ANSI
ISO
HORIZONTAL END-SUCTION PUMPS
ANSI MODELS: K+1516, K+326, K+326s, K+3156, K+436, K+1518 and
K+3158
ISO MODELS: K+i32160, K+i50160, K+i65160, K+i32200 and
K+i40200
JIS MODELS: K+j40160, K+j40200, K+j50200, K+j50160, and
K+j65160
Issued January, 2007
T.S.U.
♦♦♦♦
Do not run dry
♦♦♦♦
This pump is NOT self-priming. The pump
must be filled with liquid before starting
otherwise severe damage may occur.
“Simple by Design”