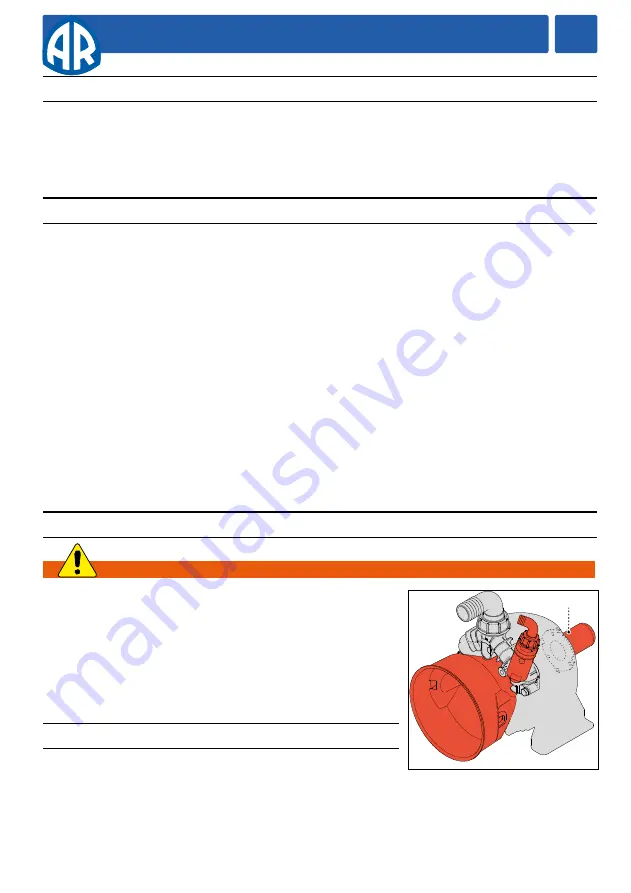
IMPORTANT SAFETY
INFORMATION
Intended uses
The pump is designed and constructed for incorporation in plants and machinery (spraying machines for the
protective treatment of agricultural crops and garden plants).
All other uses constitute misuse unless ap-
proved by the manufacturer's technical service
The pump must be used in a manner appropriate to its technical data (see “Technical Data”), and must not be
modified or improperly used.
Misuses
Do not
put the pump into service until the plant or machinery in which it is incorporated has been declared
compliant with the relevant national and local legal requirements.
Do not
use the pump in a potentially explosive atmosphere.
Do not
use the pump for
flammable
, toxic or corrosive liquids or liquids with unsuitable density, especially
s
eawater, adhesives, bitumens, asphalt sealers, two-step curing compounds, concrete sealers, liquefied
gases or solvents
of any kind, paints of any kind or liquids containing solids in suspension, and in all cases
do
not
use with any liquid unless certain that it is compatible with the materials used in the pump circuit.
Do not
draw in liquids at temperatures above 50°C or below 5°C.
Do not
use the pump in drinking water supply systems.
Do not
use the pump on products for human consumption.
Do not
use the pump on pharmaceutical products.
Do not
use the pump without first checking that the intake and delivery circuit pipelines are correctly secured
and free from leaks.
Do not
use the pump without the safety devices provided: guards for shafts and drive couplings and suitably
rated relief valve on the delivery circuit.
Do not
use the pump to wash or spray: people, animals or delicate items, live electrical equipment or chemicals
whose characteristics are not known.
Safety devices
Danger - Warning
Never tamper with or by-pass the safety devices. Maintain all safe-
ty devices regularly to ensure they all work efficiently.
The drawing shows the position of the safety devices mounted on the
machine.
Additional safety devices must be added as necessary during the de-
sign phase (see “Installation information”).
A) Fixed guard
: provides protection against accidental contacts with
the drive shaft when in operation.
Residual risks
Even if the safety regulations and information provided in the manual
are complied with, the residual risks described in the declaration of
incorporation still apply when the pump is in operation.
A