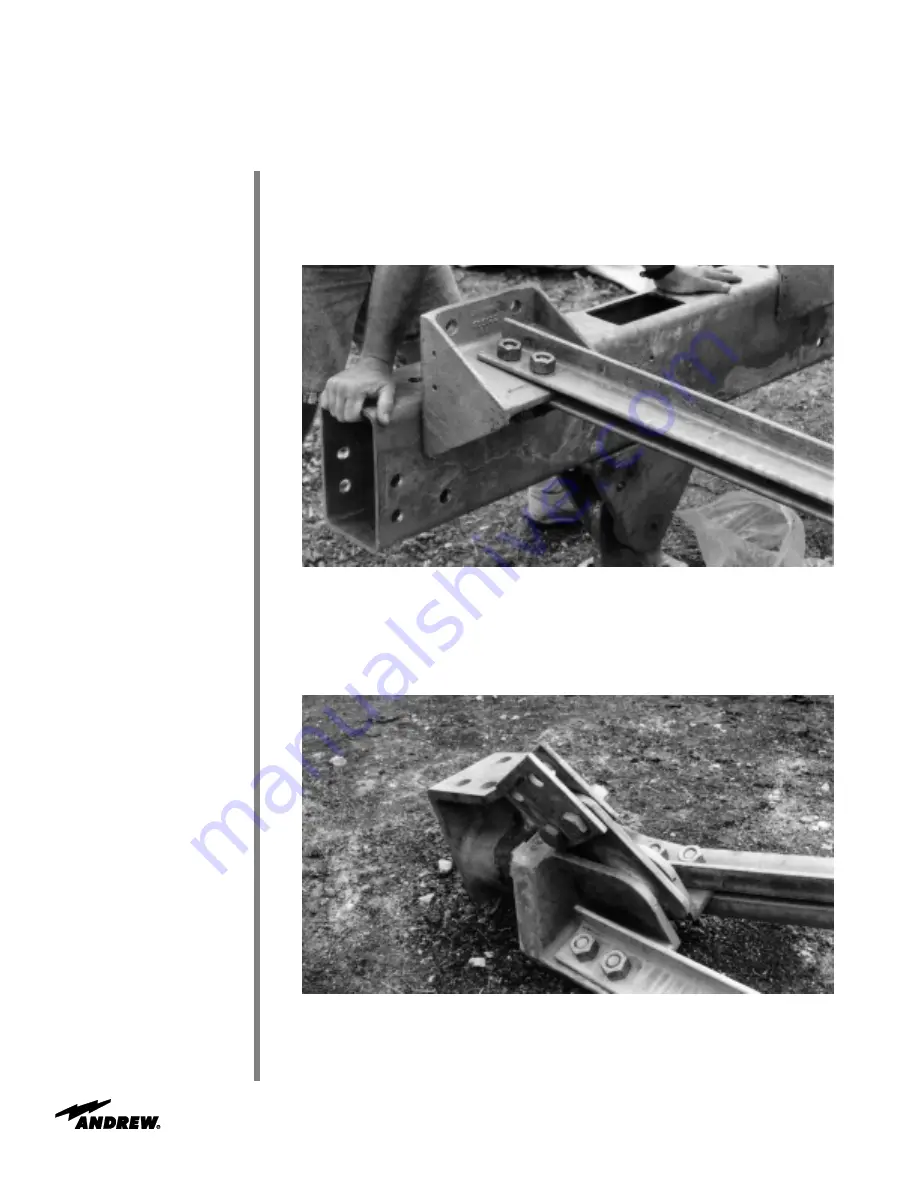
Step 3
Step 4
18
Attach 201316 support pairs to 221608 joint assemblies as shown in Figure 15.
•
Place supports back-to-back with edges out and flat of angle inward
•
Install 45967 spacer at midpoints of support pairs
•
Use 7/8 x 2-1/4 in (57 mm) hardware for each connection
Installation Procedures
Figure 15
Attach 221345 azimuth pivot assembly to 201316 support pairs. Attach 201596 mount-
ing plates to 201458 azimuth pivot assembly tab as shown in Figure 16.
•
Use 7/8 x 2-1/4 in (57 mm) hardware for each connection
•
Insert bolts from rear of pivot assembly to connect supports
Figure 16
Summary of Contents for 7.6-Meter ESA
Page 30: ...30 Installation Procedures...
Page 31: ...31 Installation Procedures...
Page 32: ...32 Installation Procedures...
Page 33: ...33 Installation Procedures...
Page 34: ...34 Installation Procedures...
Page 35: ...35 Installation Procedures...
Page 36: ...36 Installation Procedures...
Page 37: ...37 Installation Procedures...
Page 38: ...38 Installation Procedures...
Page 39: ...39 Installation Procedures...
Page 40: ...40 Installation Procedures...
Page 41: ...41 Installation Procedures...
Page 42: ...42 Installation Procedures...
Page 43: ...43 Installation Procedures...
Page 44: ...44 Installation Procedures...
Page 45: ...45 Installation Procedures...
Page 46: ...46 Installation Procedures...
Page 47: ...47 Installation Procedures...
Page 48: ...48 Installation Procedures...
Page 49: ...49 Installation Procedures...
Page 50: ...50 Installation Procedures...
Page 51: ...51 Installation Procedures...
Page 52: ...52 Installation Procedures...
Page 53: ...53 Installation Procedures...