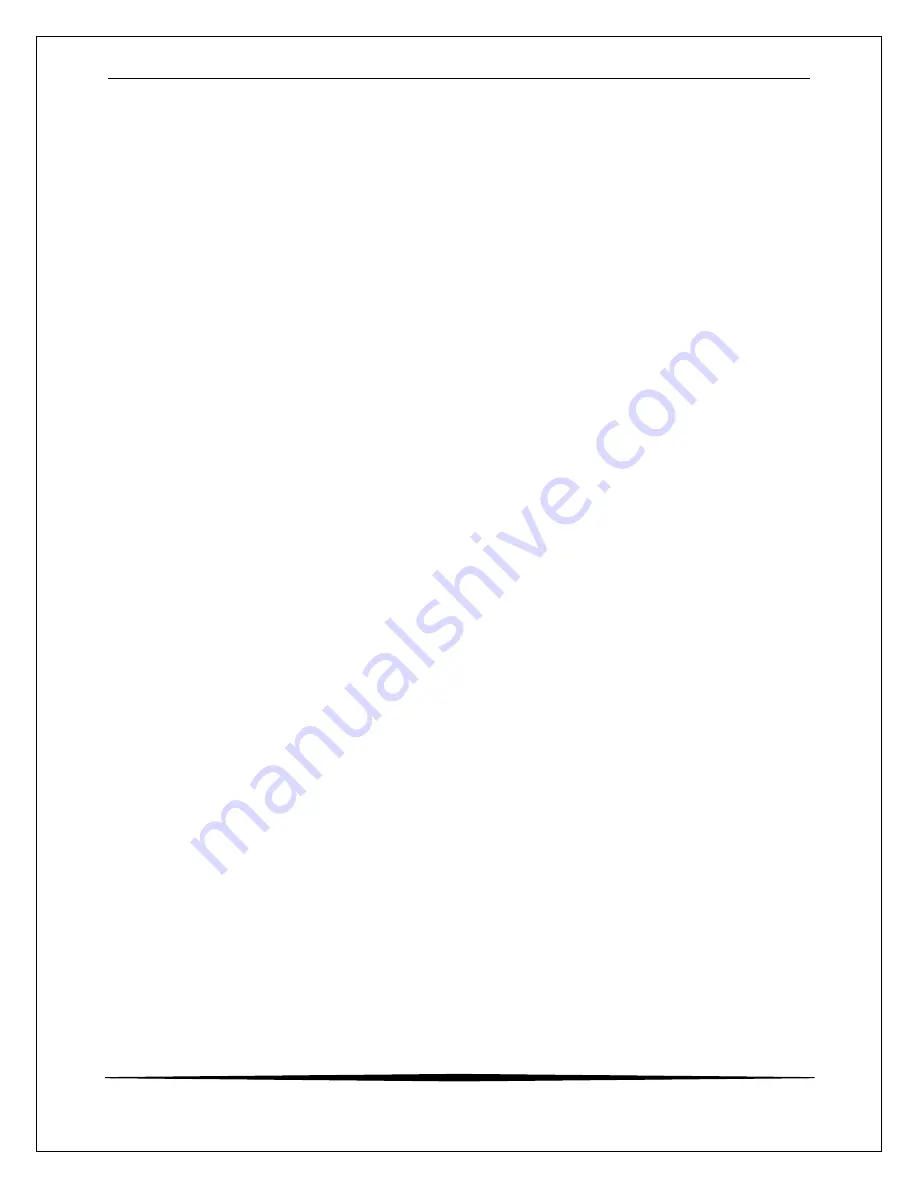
ATI
Q46D-ODO Optical D.O. System
Part 5 – Configuration
38
O&M Manual
Rev-J (8/17)
Temp Units
This function sets the display units for temperature
measurement. Press ENTER to initiate user entry mode,
and the entire value will flash. Use the UP arrow key to
modify the desired display value. The choices are
°F
and
°C
. Press ENTER to store the new value.
5.25 Control Menu [CONTROL]
The Control Menu contains all of the output control user settings. Note that PID
menu items will not appear unless output 1 is configured for PID mode in the
CONFIG menu.
Set PID 0%
Set PID 100%
[Iout1=PID]
If the PID is enabled, this function sets the minimum and
maximum controller end points. Unlike the standard 4-20
mA output, the controller does not “scale” output values
across the endpoints. Rather, the endpoints determine
where the controller would normally force minimum or
maximum output in an attempt to recover the setpoint (even
though the controller can achieve 0% or 100% anywhere
within the range.)
If the 0% point is lower than the 100% point, then the
controller action will be “reverse” acting. That is, the output
of the controller will increase if the measured value is less
than the setpoint, and the output will decrease if the
measured value is larger than the setpoint. Flipping the
stored values in these points will reverse the action of the
controller to “direct” mode.
The entry value is limited to a value within the range
specified in “Set Range”, and the 0% and the 100% point
must be separated by at least 1% of this range Use the
LEFT arrow key to select the first digit to be modified. Then
use the UP and LEFT arrow keys to select the desired
numerical value. Press ENTER to store the new value.
PID Setpnt
[Iout1=PID]
The measured value which the controller is attempting to
maintain by adjusting output value. It is the nature of the
PID controller that it never actually gets to the exact value
and stops. The controller is continually making smaller and
smaller adjustments as the measured value gets near the
setpoint.