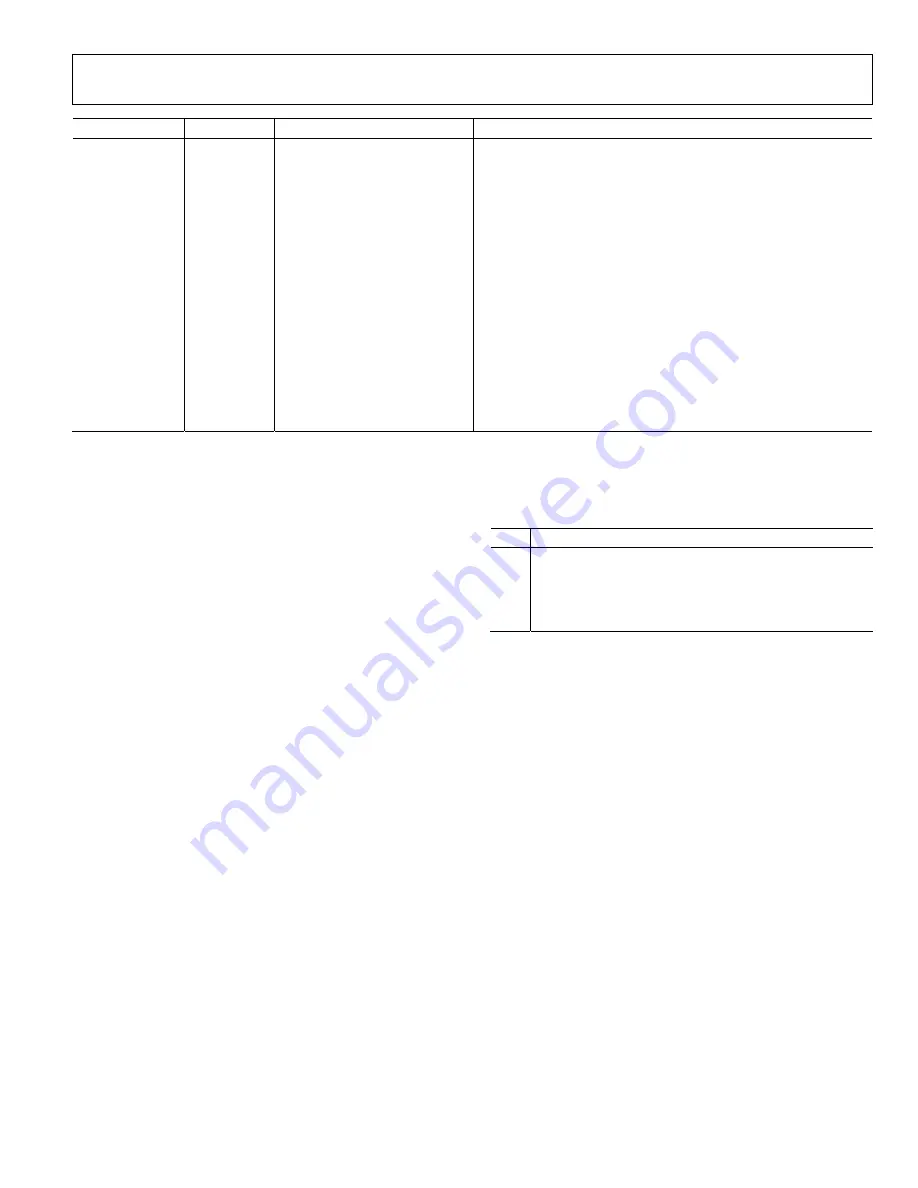
ADXL180
Rev. 0 | Page 35 of 56
Decimal Hex Data
Type
Description
−497
0x20F
Nybble Number
Device Data Nybble 16
−498
0x20E
Nybble Number
Device Data Nybble 15
−499
0x20D
Nybble Number
Device Data Nybble 14
−500
0x20C
Nybble Number
Device Data Nybble 13
−501
0x20B
Nybble Number
Device Data Nybble 12
−502
0x20A
Nybble Number
Device Data Nybble 11
−503
0x209
Nybble Number
Device Data Nybble 10
−504
0x208
Nybble Number
Device Data Nybble 9
−505
0x207
Nybble Number
Device Data Nybble 8
−506
0x206
Nybble Number
Device Data Nybble 7
−507
0x205
Nybble Number
Device Data Nybble 6
−508
0x204
Nybble Number
Device Data Nybble 5
−509
0x203
Nybble Number
Device Data Nybble 4
−510
0x202
Nybble Number
Device Data Nybble 3
−511
0x201
Nybble Number
Device Data Nybble 2
−512
0x00
Nybble Number
Device Data Nybble 1
PHASE 3: SELF-TEST DIAGNOSTIC
The ADXL180 has two self-test modes, internal and external. In
both modes the ADXL180 applies an internally generated electro-
static force to the sensor, simulating an acceleration force. This
force causes the sensor proof-mass to displace. This displacement
is transduced by the sensor interface electronics and passed
through the signal chain to the ADC. When in external self-test
mode, the ADXL180 transmits sensor data while activating the
self-test signal several times. When in internal self-test mode,
the ADXL180 transmits data dependent on the setting of the
Phase 2 Mode select bits. While doing so, the ADXL180 activates
the self-test signal several times. It then examines the results
and either continues the start-up initialization sequence or
reports an error. The detailed operation of the two self-test
modes is described in the following sections.
Concept of Self-Test
The fixed plates in the forcing cells are normally kept at the
same potential as that of the movable frame. When self-test is
activated, the voltage between the fixed plates and the moving
plates in the forcing cells is changed. This creates an attractive
electrostatic force, which causes the frame to move toward one
set of fixed plates. The entire signal channel is active; therefore,
the sensor displacement causes a signal change at the output of
the ADC.
Internal and External Self-Test Option
There are two selectable modes of operation for self-test. The
self-test modes are internal and external. The self-test mode is
toggled by selecting or deselecting the STI configuration bit, as
shown in Table 35.
Table 35. Self Test Internal (STI) Options
STI Definition
0
External self-test. User must monitor self-test data to
verify proper operation. Device does not monitor its own
response to the self-test stimulus. (Default.)
1
Internal self-test. The device internally monitors self-test
data to determine proper operation.
External Self-Test
The external self-test mode applies an electrostatic force to the
sensor (simulating an acceleration force) and transmits the
sensor data to the control module. This allows the control
module to measure the subsequent change in the sensor output
value. The signal path low-pass filter of the ADXL180 has a
slower response time than the rise time of the internal self-test
control (STC) signal. Therefore, the sensor data transmitted
during the external self-test sequence follows the rise and fall
times of the low pass filter in response to the internal STC
signal. The state vector (if enabled) provides the relative timing
information indicating when the internal STC signal is applied
to the sensor.
The STC signal activates six times during the self-test state of
the ADXL180 (see Figure 26). During external self-test, an
average of the zero self-test value is computed and subsequently
used to provide an initial offset correction value for the auto-
zero function. See the Phase 4: Auto-Zero Initialization section
for more information.