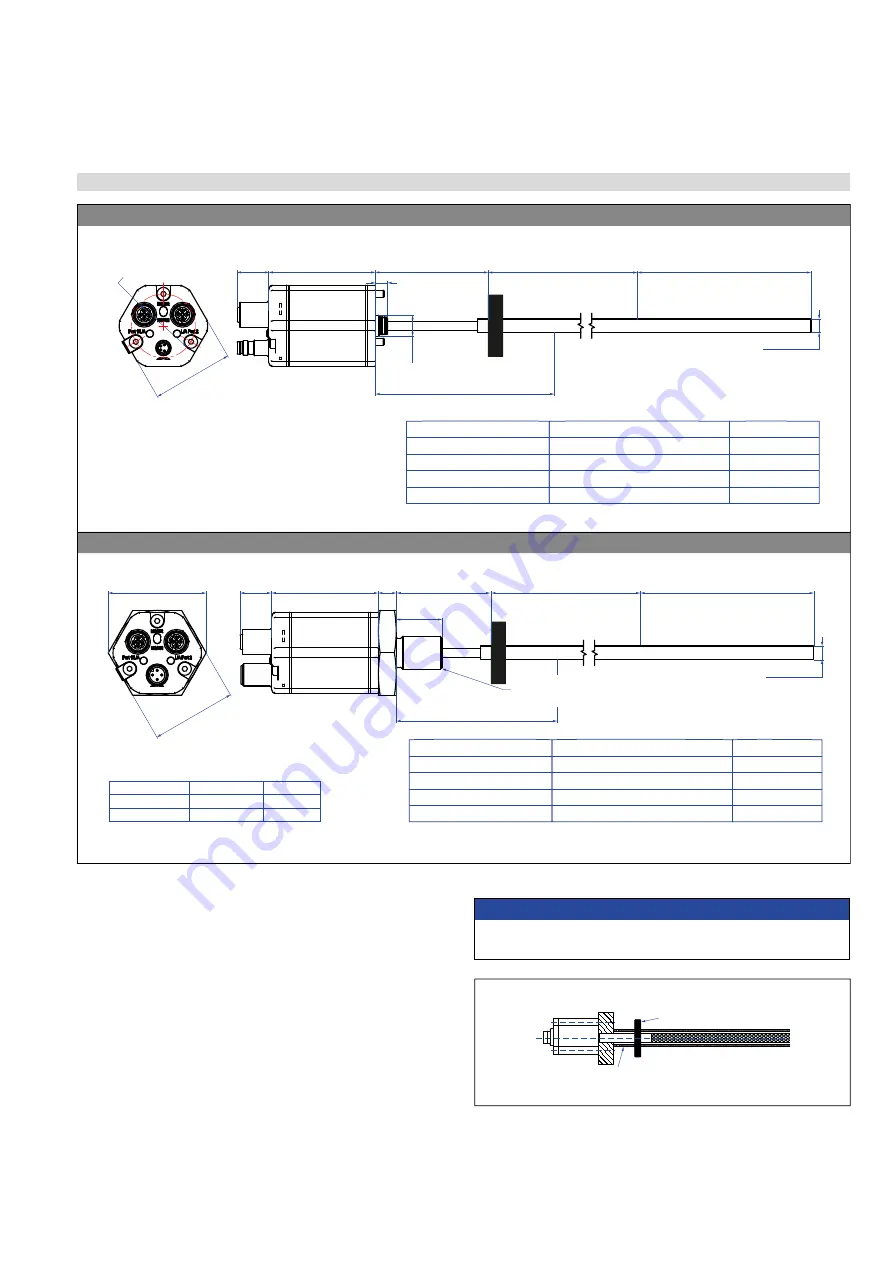
Temposonics
®
R-Series
V
POWERLINK
Operation Manual
I 15 I
4.4 Installation and design of Temposonics
®
RFV
Fig. 12: Temposonics
®
RFV with ring magnet
Fig. 13: Sensor with support tube
Installation of RFV
Note the following information when mounting and handling an RFV
sensor:
1. Always insert the flexible sensor rod in a support tube (e.g.
pressure rod HD/HL/HP or HFP profile). The support tube has
to be made of non-magnetic material and has to have an inside
diameter of minimum 9.4 mm (0.37 in.) (Fig. 13). The support
tube can be straight or bent.
2. Do never bend beyond the minimum bending radius of 250 mm
(9.84 in.).
3. Note the minimum distance to a spatial limitation of 300 mm
(11.81 in.), when mounting/dismounting the sensor. The
recommended distance is 500 mm (20 in.) (Fig. 15).
4. Note the non-flexible area of the sensor rod from the flange of
107 mm (4.21 in.) (for RFV-B) respectively 97 mm (3.82 in.) (for
RFV-M/-S).
NOTICE
Smaller radiuses < 250 mm (9.84 in.) cause damage to the flexible
sensor rod.
Position magnet
Non-magnetic support tube, inside Ø 9.4 (0.37)
Linear measurement
RFV-B – RFV base unit, example: Connection type D56 (connector outlet)
Magnet
Null zone
61
(2.4)
Dead zone
see table
17
(0.67)
7
(0.28)
11.4
(0.45)
Not flexible
107 (4.2)
Stroke length
150…20,000
(6…787)
Ø 8 ±0.23
(Ø 0.31±0.01)
Sensor electronics housing
58
(2.28)
Tolerance of total length
Dead zone
Stroke length
Up to 7620 mm (300.00 in.)
Up to 10,000 mm (393.70 in.)
Up to 15,000 mm (590.55 in.)
Up to 20,000 mm (787.00 in.)
+8 mm (0.31 in.)/−5 mm (0.20 in.)
+15 mm (0.59 in.)/−15 mm (0.59 in.)
+15 mm (0.59 in.)/−30 mm (1.18 in.)
+15 mm (0.59 in.)/−45 mm (1.77 in.)
94 mm (3.70 in.)
100 mm (3.94 in.)
120 mm (4.72 in.)
140 mm (5.51 in.)
Note:
Tolerance of total length has no influence on the stroke length.
44
(1.7)
Ø 34.6
(Ø
1.36)
RFV-M/-S – RFV with threaded fl ange M18×1.5-6g or ¾"-16 UNF-3A, example: Connection type D58 (connector outlet)
Magnet
Null zone
51
(2)
Dead zone
see table
10
17
(0.67)
b
Not flexible
97 (3.82)
Stroke length
150…20,000
(6…787)
Ø 8 ±0.23
(Ø 0.31 ±0.01)
Threaded flange
»M«
:
M18×1.5-6g
Threaded flange
»S«
:
¾"-16 UNF-3A
Sensor electronics housing
58
(2.28)
Tolerance of total length
Dead zone
Stroke length
Up to 7620 mm (300.00 in.)
Up to 10,000 mm (393.70 in.)
Up to 15,000 mm (590.55 in.)
Up to 20,000 mm (787.00 in.)
+8 mm (0.31 in.)/−5 mm (0.20 in.)
+15 mm (0.59 in.)/−15 mm (0.59 in.)
+15 mm (0.59 in.)/−30 mm (1.18 in.)
+15 mm (0.59 in.)/−45 mm (1.77 in.)
94 mm (3.70 in.)
100 mm (3.94 in.)
120 mm (4.72 in.)
140 mm (5.51 in.)
Note:
Tolerance of total length has no influence on the stroke length.
a
Threaded flange
»M«
»S«
a b
A/F 46 (1.81) 53
(2.09)
A/F 44.5 (1.75) 51.3 (2.02)
Controlling design dimensions are in millimeters and measurements in ( ) are in inches
Controlling design dimensions are in millimeters and measurements in ( ) are in inches