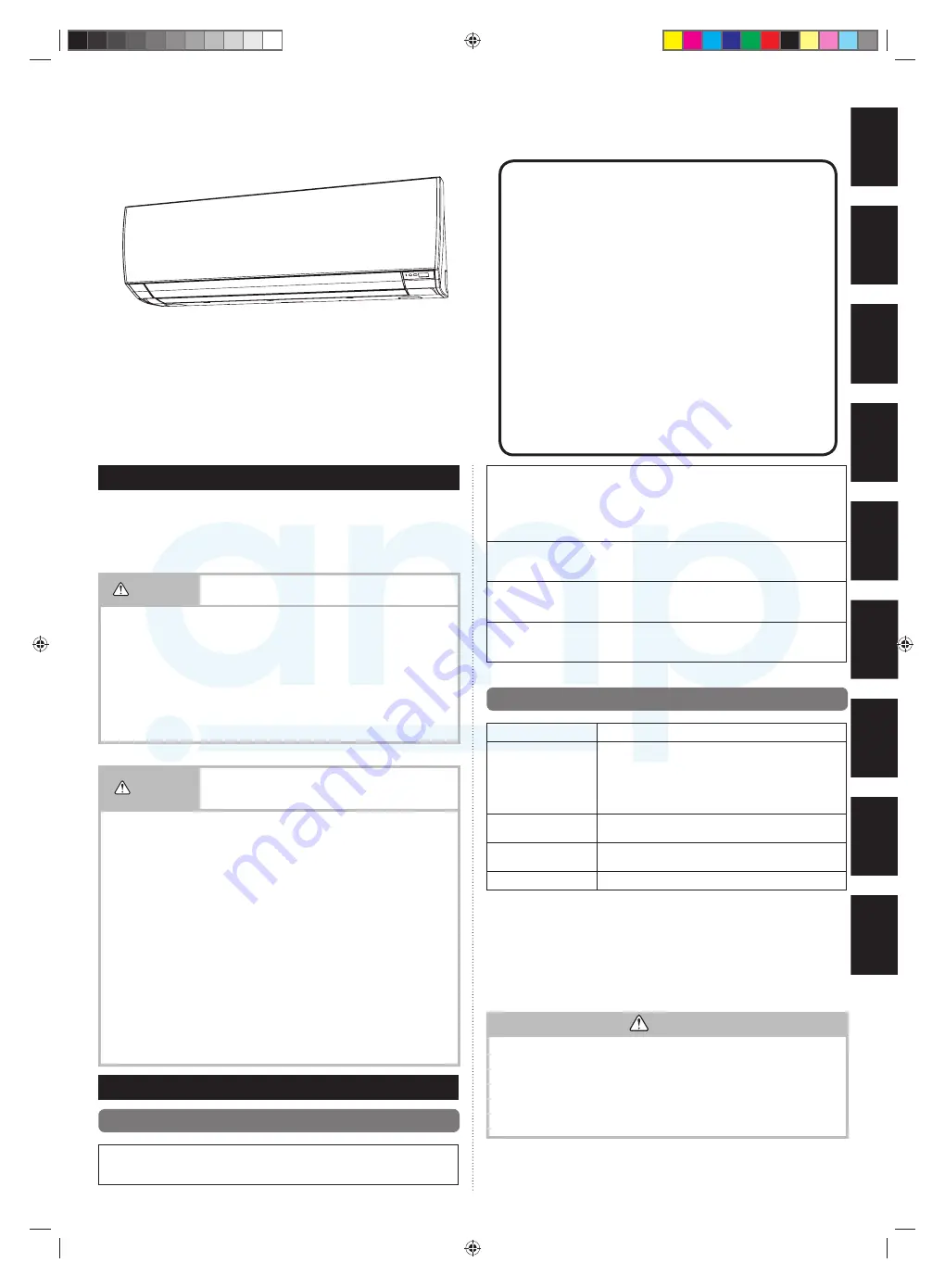
En-1
1. SAFETY PRECAUTIONS
Be sure to read this Manual thoroughly before installation.
•
The warnings and precautions indicated in this Manual contain important information
•
pertaining to your safety. Be sure to observe them.
Hand this Manual, together with the Operating Manual, to the customer. Request the
•
customer to keep them on hand for future use, such as for relocating or repairing the
unit.
WARNING
This mark indicates procedures which, if improperly per-
formed, might lead to the death or serious injury of the user.
• Request your dealer or a professional installer to install the indoor unit in accordance
with this Installation Manual. An improperly installed unit can cause serious accidents
such as water leakage, electric shock, or fi re. If the indoor unit is installed in disregard
of the instructions in the Installation Manual, it will void the manufacturer’s warranty.
• Do not turn ON the power until all work has been completed. Turning ON the power
before the work is completed can cause serious accidents such as electric shock or
fi re.
• If refrigerant leaks while work is being carried out, ventilate the area. If the refrigerant
comes in contact with a fl ame, it produces a toxic gas.
• Installation work must be performed in accordance with national wiring standards by
authorized personnel only.
CAUTION
This mark indicates procedures which, if improperly
performed, might possibly result in personal harm to the user,
or damage to property.
• Read carefully all security information before use or install the air conditioner.
• Do not attempt to install the air conditioner or a part of the air conditioner by yourself.
• This unit must be installed by qualifi ed personnel with a capacity certifi cate for han-
dling refrigerant fl uids. Refer to regulation and laws in use on installation place.
• The installation must be carried out in compliance with regulations in force in the
place of installation and the installation instructions of the manufacturer.
• This unit is part of a set constituting an air conditioner. It must not be installed alone
or with non-authorized by the manufacturer.
• Always use a separate power supply line protected by a circuit breaker operating on
all wires with a distance between contact of 3mm for this unit.
• The unit must be correctly grounded and the supply line must be equipped with a
differential breaker in order to protect the persons.
• The units are not explosion proof and therefore should not be installed in explosive
atmosphere.
• Never touch electrical components immediately after the power supply has been
turned off. Electric shock may occur. After turning off the power, always wait 5 min-
utes before touching electrical components.
• This unit contains no user-serviceable parts. Always consult authorized service
personnel to repairs.
• When moving, consult authorized service personnel for disconnection and installation
of the unit.
2. ABOUT THE UNIT
2.1. Precautions for using R410A refrigerant
The basic installation work procedures are the same as conventional refrigerant (R22)
models.
However, pay careful attention to the following points:
Since the working pressure is 1.6 times higher than that of conventional refrigerant
(R22) models, some of the piping and installation and service tools are special. (See
the table below.)
Especially, when replacing a conventional refrigerant (R22) model with a new refrigerant
R410A model, always replace the conventional piping and flare nuts with the R410A piping
and fl are nuts.
Models that use refrigerant R410A have a different charging port thread diameter to pre-
vent erroneous charging with conventional refrigerant (R22) and for safety. Therefore,
check beforehand. [The charging port thread diameter for R410A is 1/2 inch.]
Be more careful that foreign matter (oil, water, etc.) does not enter the piping than with
refrigerant (R22) models. Also, when storing the piping ,securely seal the opening by
pinching, taping, etc.
When charging the refrigerant, take into account the slight change in the composition of
the gas and liquid phases. And always charge from the liquid phase where refrigerant
composition is stable.
2.2. Special tools for R410A
Tool name
Contents of change
Gauge manifold
Pressure is high and cannot be measured with a conven-
tional (R22) gauge. To prevent erroneous mixing of other
refrigerants, the diameter of each port has been changed.
It is recommended the gauge with seals -0.1 to 5.3 MPa
(-1 to 53 bar) for high pressure.
-0.1 to 3.8 MPa (-1 to 38 bar) for low pressure.
Charge hose
To increase pressure resistance, the hose material and base
size were changed.
Vacuum pump
A conventional vacuum pump can be used by installing a
vacuum pump adapter.
Gas leakage detector
Special gas leakage detector for HFC refrigerant R410A.
Copper pipes
It is necessary to use seamless copper pipes and it is desirable that the amount of residual
oil is less than 40 mg/10 m. Do not use copper pipes having a collapsed, deformed or
discolored portion (especially on the interior surface). Otherwise, the expansion value or
capillary tube may become blocked with contaminants.
As an air conditioner using R410A incurs pressure higher than when using R22, it is neces-
sary to choose adequate materials.
WARNING
Do not use the existing (for R22) piping and fl are nuts.
If the existing materials are used, the pressure inside the refrigerant cycle will rise and
cause failure, injury, etc. (Use the special R410A materials.)
When installing and relocating the air conditioner, do not mix gases other than
the specifi ed refrigerant (R410A) to enter the refrigerant cycle.
If air or other gas enters the refrigerant cycle, the pressure inside the cycle will rise to
an abnormally high value and cause failure, injury, etc.
Português
E
λλη
vIk
ά
Italiano
Español
Français
Deutsch
English
Türkçe
Русский
AIR CONDITIONER
Wall Mounted Type
INSTALLATION MANUAL
Contents
1. SAFETY
PRECAUTIONS
.................................................................. 1
2. ABOUT
THE
UNIT
............................................................................. 1
3. GENERAL
SPECIFICATION
............................................................. 2
4. ELECTRICAL
REQUIREMENT
......................................................... 2
5.
SELECTING THE MOUNTING POSITION ....................................... 2
6. INSTALLATION
WORK
..................................................................... 3
7. ELECTRICAL
WIRING
..................................................................... 5
8. FINISHING
........................................................................................ 5
9.
FRONT PANEL REMOVAL AND INSTALLATION ............................. 6
10. TEST
RUN
......................................................................................... 6
11.
REMOTE CONTROLLER INSTALLATION ........................................ 6
12. OPTIONAL KIT INSTALLATION (OPTION) ....................................... 6
13. INSTALLATION
WORK
..................................................................... 7
14. FUNCTION
SETTING........................................................................ 9
15. CUSTOMER
GUIDANCE
................................................................ 10
16. ERROR
CODES
...............................................................................11
PART No. 9333005003-04
9333005003-04_IM.indb 1
9333005003-04_IM.indb 1
2013-3-6 14:51:30
2013-3-6 14:51:30
AMP Air Conditioning
www.ampair.co.uk | [email protected]