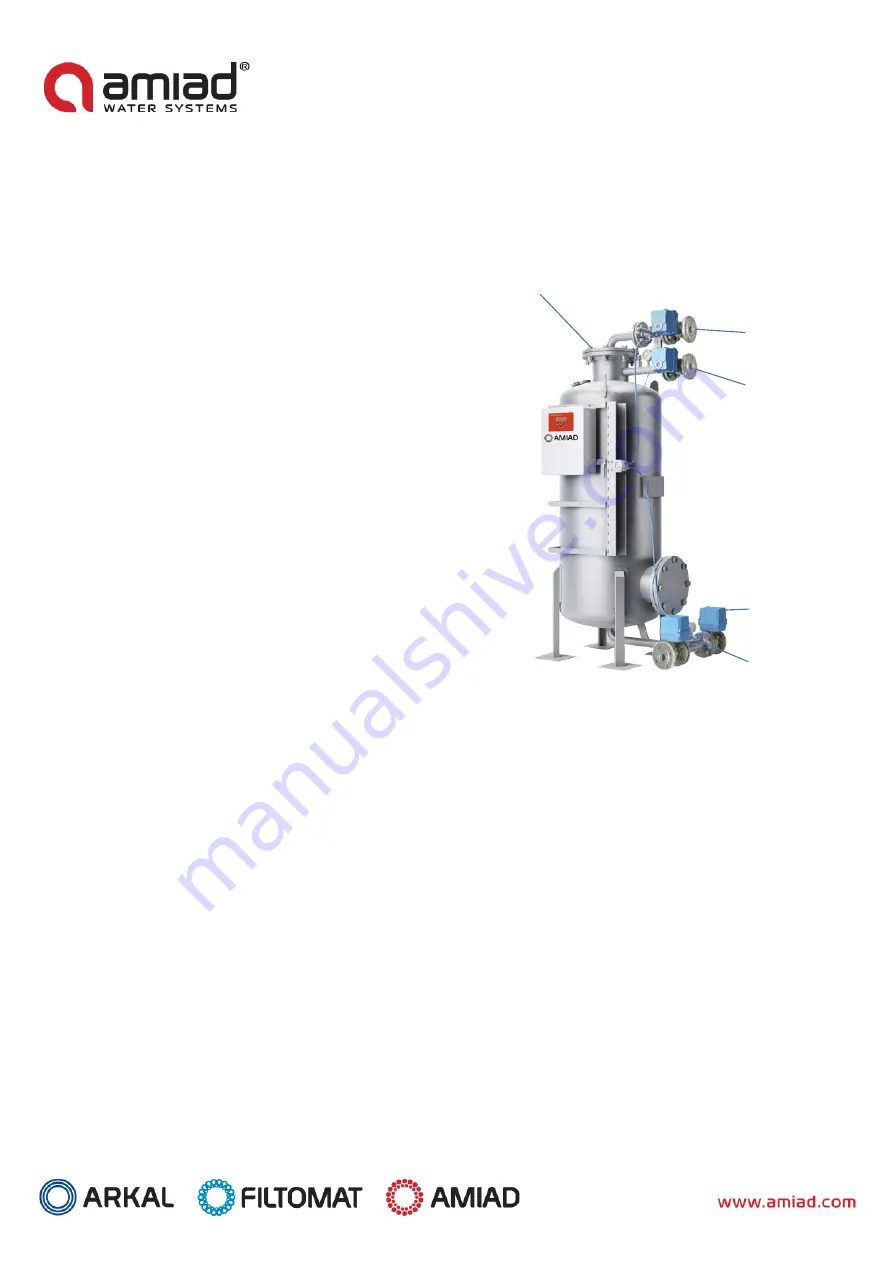
910101-001048
12/2019
Page 15 of 42
Media Filling Process
Before filling the vessel, please follow these steps:
•
Visually inspect the inside of the vessel to ensure all
the media retaining nozzles are present and fixed in
place.
•
When performing this inspection:
o
Ensure that you are wearing the correct PPE.
o
Locate the top flange – see fig. A.
o
Now carefully remove the bolts on the top flange.
This will release the blind flange and gasket. Care
should be taken not to damage the flange, flange
gasket, or drop the bolts inside the vessel.
o
Carefully remove the flange and internal pipe-work,
which has the Dual Vortex Generator attached. This
will expose the nozzles for inspection. Make sure all
nozzles are in place.
o
If any nozzles are missing, please contact Amiad
Water Systems before proceeding further.
DO NOT FILL THE VESSEL IF NOZZLES ARE MISSING.
Make sure vessel interior is free from any debris
before following the media filling procedure below.
•
It is strongly recommended to use correct PPE during
media installation. (See media data sheets which can
be found on the bags, and further in this document).
o
First ensure that the valves on the backwash inlet
V3 and process outlet V2 are closed.
o
Now, via the top flange, fill half the vessel with clean, fresh water. This is to ensure no damage occurs to the
backwash nozzles located within the vessel base.
o
Load the base media in the correct order (beginning with the largest size first – i.e. Grade 3) with the applicable
quantities, as shown in the Media Data table below. The depth guide is in mm and given as a guideline only.
o
Level each layer before moving on to the next layer.
o
Once the loading is complete, the media should be within approximately 20mm of the base of the vortex
generator. Check this with the length of the vortex inlet pipe as you are filling the vessel to avoid overfilling.
o
Place the top flange with the gasket back onto the vessel in the same orientation as it was removed,
remembering to securely screw the feed pipe via union.
•
The media bags are marked for the grade size.
Fig. A.
Top
Flange
V1
Process Inlet
Valve
V4
Backwash
Outlet Valve
V3
Backwash
Inlet Valve
V2
Process
Outlet Valve
Summary of Contents for DVF
Page 20: ...910101 001048 12 2019 Page 20 of 42 DVF Filter P ID Drawing ...
Page 21: ...910101 001048 12 2019 Page 21 of 42 DVF 300 Filter GA Drawing ...
Page 22: ...910101 001048 12 2019 Page 22 of 42 DVF 300 Filter Parts Drawing ...
Page 24: ...910101 001048 12 2019 Page 24 of 42 DVF 600 Filter GA Drawing ...
Page 25: ...910101 001048 12 2019 Page 25 of 42 DVF 600 Filter Parts Drawing ...
Page 27: ...910101 001048 12 2019 Page 27 of 42 DVF 900 Filter GA Drawing ...
Page 28: ...910101 001048 12 2019 Page 28 of 42 DVF 900 Filter Parts Drawing ...
Page 30: ...910101 001048 12 2019 Page 30 of 42 DVF 1200 Filter GA Drawing ...
Page 31: ...910101 001048 12 2019 Page 31 of 42 DVF 1200 Filter Parts Drawing ...
Page 35: ...910101 001048 12 2019 Page 35 of 42 Annex A Media Safety Data Sheet 7 pages ...
Page 36: ...910101 001048 12 2019 Page 36 of 42 ...
Page 37: ...910101 001048 12 2019 Page 37 of 42 ...
Page 38: ...910101 001048 12 2019 Page 38 of 42 ...
Page 39: ...910101 001048 12 2019 Page 39 of 42 ...
Page 40: ...910101 001048 12 2019 Page 40 of 42 ...