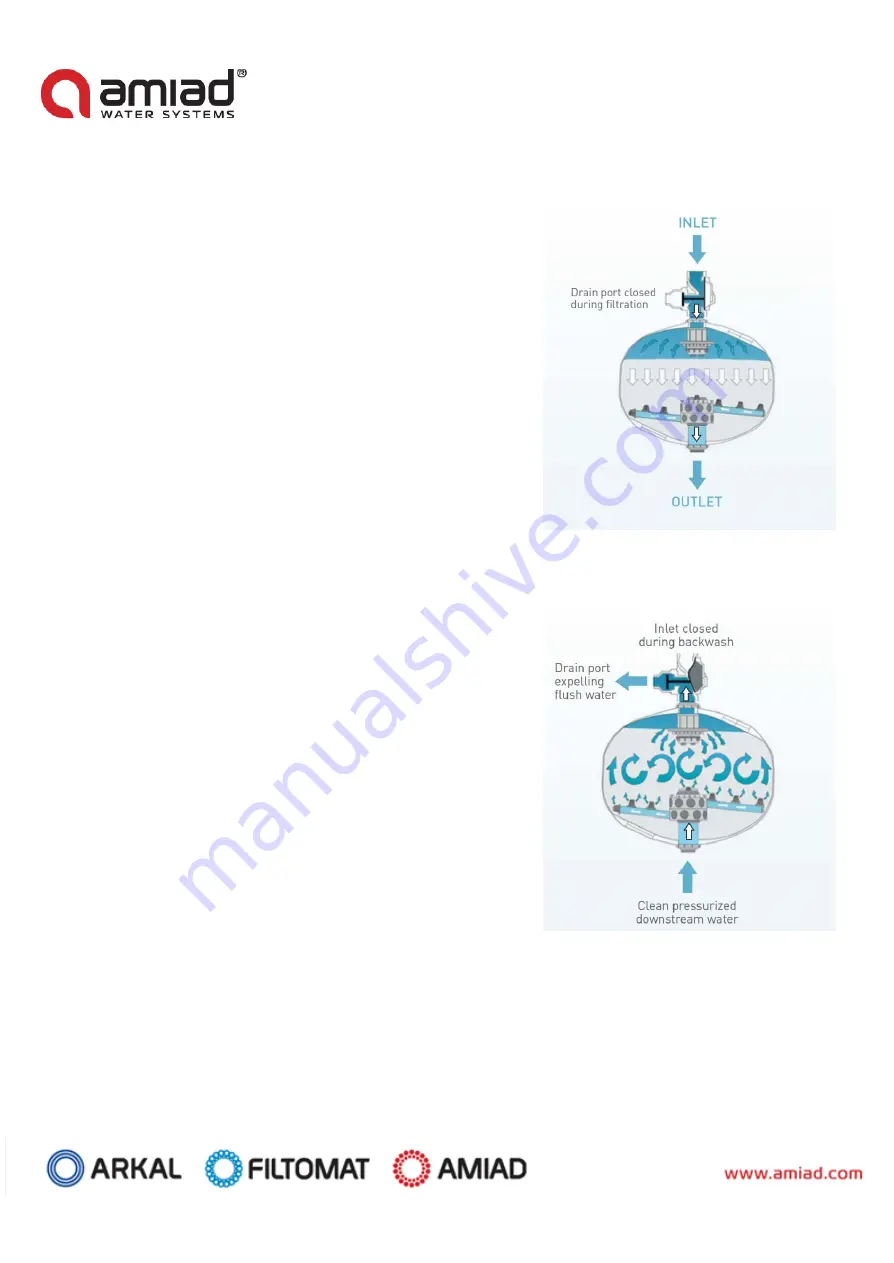
48" AGF 910101-001049 / 01.2020
Page 12 of 21
3.
The Filtration Process
Filtration with media filters, also known as depth filtration, is done by
filtering water through a thick layer of graded particles, called the filter bed.
These particles can be sand, gravel or other granular materials. The filtration
degree depends on the effective size of the bedding and the water velocity
through the filter.
Raw water enters from the filter inlet and percolates through the filter bed.
Suspended materials come into contact and attach to the media particles.
Filtered water flows through the filtration nozzles and out through the filters
outlet.
4.
The Backwash Process
Cleaning is done by backwashing; pressurized water flows in reverse
direction – from the nozzles upwards, causing suspension of the filter bed,
thus releasing the suspended matter from the bedding. The dirt particles are
then washed out of the filter through the backwash valve. In automatic
media filters installations, the cleaning process is initiated by the system’s
controller. When the pressure differential switch senses that the differential
pressure across the system reached a pre-set value, a signal is sent to the
backwashing controller and the self-cleaning process begins.
The restriction control flow valve on the drain manifold needs to be adjusted
properly. This is essential so debris will be backwashed out of the filter while
the media will remain in the filter tank.