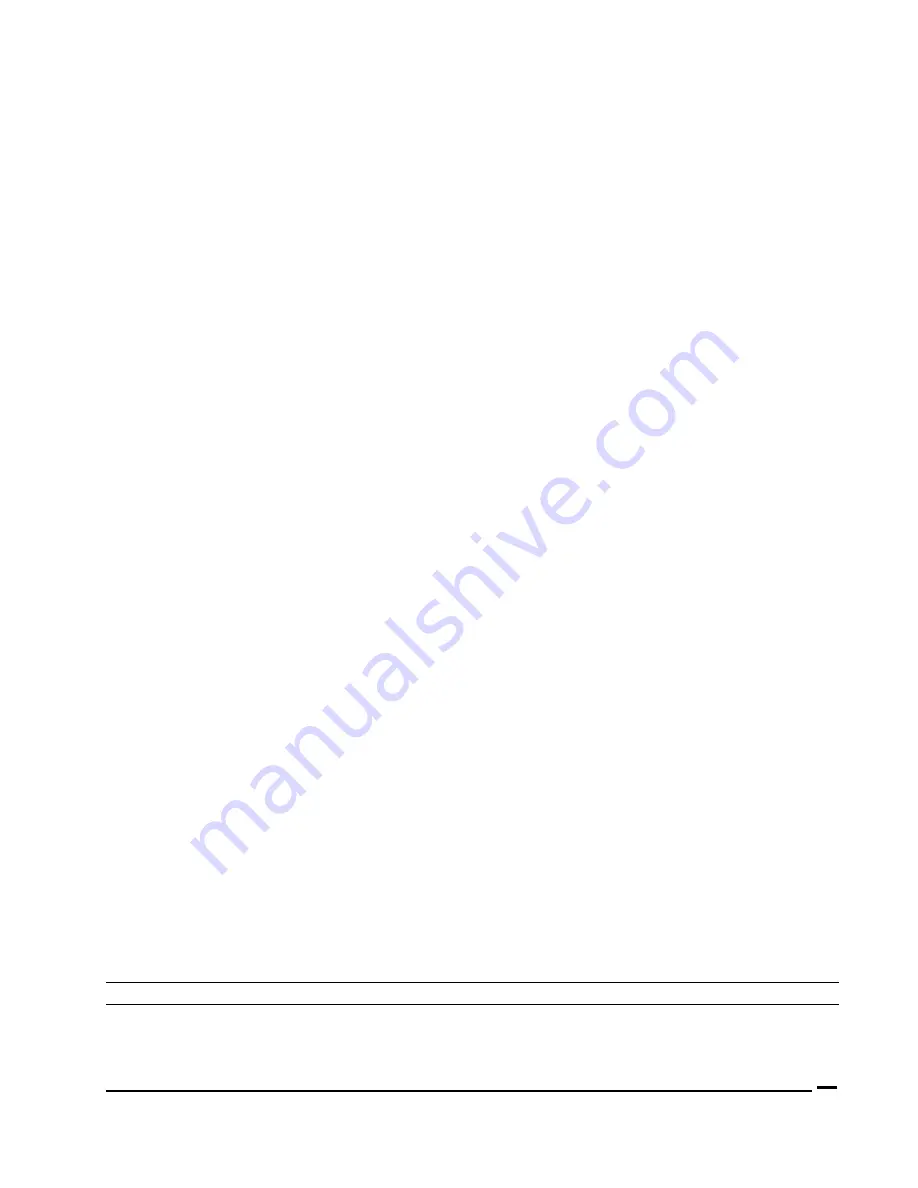
AMI Analyzer Manual
Maintenance and troubleshooting
••••
15
Troubleshooting
All oxygen applications
Analyzer does not power up.
1.
Check that the power is connected correctly, and the switch on the power entry module is on.
2.
Check that the power supply voltage is 24VDC only.
Analyzer reads too low
1.
Sensor is not calibrated. Flow span gas through it and span the analyzer until the analyzer reads appropriately.
2.
If you cannot adjust the span enough to accomplish this, replace the sensor.
3.
If the new sensor still reads too low, check its calibration with air and read the span gas - the span gas may be
incorrect.
4.
If the sensor seems to die quickly, it may be getting poisoned by acid or sulfur bearing gases such as H
2
S. These
should be scrubbed from the sample stream by a scrubber.
5.
Verify that the cell block connectors are in fact making contact with the cell. Clean them gently with a Q tip, and
bend them slightly straighter so that they make a good contact. Once this is done the cell should have some
resistance to being removed from the block.
Analyzer reads too high
1.
Verify that there is no flow restriction in the vent line of the analyzer.
2.
Increase the flow rate through analyzer by increasing the sample pressure - if the reading goes down it indicates a
leak in the incoming sample line or the cell block. Use “Snoop
” or equivalent to check all the fittings back to the
gas source.
3.
Leak test all external fittings with “Snoop
” soap solution or equivalent.
4.
Verify that the gas flow rate is correct. (0.1 to 2 SCFH)
5.
Oxygen diffusion can be a serious problem. Verify that no plastic tubing or other plastic components are used in a
trace gas system, including diaphragms of pressure regulators, packing of valves etc. For percent applications,
similar problems may be experienced with silicone tubing. Use Teflon
or Tygon
or similar high quality
tubing.
6.
Verify the analyzer calibration using air as the span gas.
7.
Flow zero gas through the analyzer for a while until the reading is stable: shut off the incoming flow with the
sample valve and then immediately seal the vent tightly with a tube plug or equivalent (don’t pressurize the cell!).
Monitor the reading and see if it increases significantly over a 5 minute period. Such an increase indicates a leak
in the cell block or internal sample system.
8.
Remove the cell (and short it out!) and verify that the analyzer reads zero - if not, there is moisture or corrosion
between the sensor contacts in the cell block; clean the contacts and the area around them with isopropyl alcohol,
dry with dry compressed air or nitrogen, then replace the cap on the cell block again. Pressurize the system to no
more than 10 psig and leak check all the fittings and tubing including the sensor block penetrations such as the
sensor wire seals (nylon plugs and epoxy seals on the top of the cell block).
NOTE: Be careful not to get soap solution on the PC board!