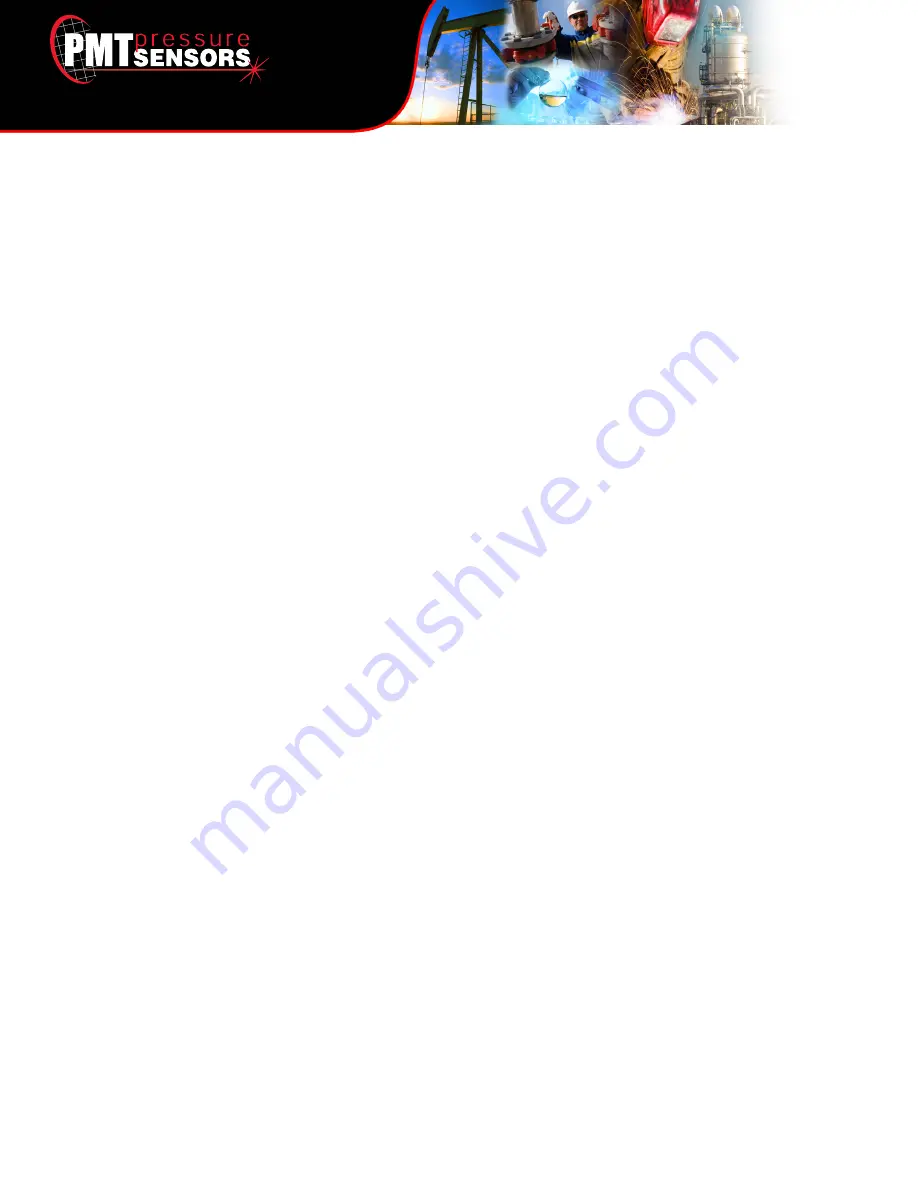
User Manual
3
PROCESS CONNECTION
(See Fig. 2 thru Fig. 9)
BEFORE APPLYING PROCESS REFER TO
PRESSURE LIMIT LABEL ATTACHED TO
INSTRUMENT.
Pressure connection is ¼" NPT (std).
For corrosive fluids which would attack the
process element it is desirable to use a chemical
seal which isolates the measuring element from
the corrosive medium. If seal is installed at
different elevation from instrument, correction
must be made. SEE ELEVATION ADJUSTMENT.
ELEVATION ADJUSTMENT
INSTRUMENT SHOULD BE FREE OF TRAPPED
AIR OR VAPOR BEFORE MAKING ELEVATION
ADJUSTMENT
When a correction is necessary the process and
setting pointers must be moved upscale when
the instrument is above the process line and
downscale when below until it reads line pressure
instead of pressure at instrument level. The
correct amount is 1 PSI for 27.7” H2O (6,9kPa)
and is proportional to the specific gravity of other
liquids. For remote chemical seal attachment
(S.P. of filling fluid is 0.9). The correction is 1 PSI
for 30.8” of fill fluid.
PRINCIPLE OF OPERATION
LOW BLEED RELAY (Fig. 10)
The low bleed relay is in equilibrium (neither
feeding nor exhausting air) as long as the process
is not changing. At equilibrium the force exerted
by the nozzle diaphragm equals the force exerted
by the output diaphragm. A change in the
process causes a change in the flapper nozzle
gap, thus producing a change of nozzle back
pressure which changes the force exerted by
the diaphragm. The force exerted by the nozzle
diaphragm is not equal to the force exerted by
the output diaphragm, causing the valve stem to
move to a new position either opening the inlet
port allowing supply air to enter the output or
opening the exhaust port exhausting output air.
Either of these changes continue until the force
developed by the output diaphragm balances the
force of the nozzle diaphragm and equilibrium is
restored.
SET POINT (Fig. 10)
Control point setting is accomplished by turning
the set point knob to swing the entire outer
movement up or down around pivot S. The
setting motion is fed to the indicating movement
by link EF and is shown by set pointer (red).
PROPORTIONAL CONTROLLER
(Fig. 10 – shown in reverse action)
With a decrease in process pressure the following
occurs:
1. Process pointer (Black) rotates
counterclockwise (ccw) from a downward
motion of GH.
2. Lever BCD rotates clockwise (cw) from a
downward motion of AB.
3. Arbor PP rotates ccw causing flapper to
restrict nozzle flow.
4. Supply pressure feeding thru restrictor
expands nozzle diaphragm.
5. Inlet port opens and exhaust port closes.
6. Output pressure on output gauge increases.
7. Feedback capsule expands moving link JL to
the left.
8. Proportional link NM pivoting about M causes
link JK to move upward.
9. Lever KC rotates cw about P causing lever
BCD to rotate ccw about B producing flapper
motion off-setting input motion.
10. Equilibrium is reached with the change in
output proportional to the change in input.
Proportionality factor or band adjustment is
determined by the angle LNM producing the
necessary amount of feedback.
DIFFERENTIAL GAP CONTROLLER (Fig. 10)
With M in line with JK negative feedback is
reduced to zero and essentially on-off action
results. If proportional dial is rotated to other
quadrant, (position M’) feedback motion becomes
positive adding to input from “A” with on and
off points separated by the amount of feedback
motion.
Summary of Contents for PMT 40
Page 1: ...Model 40 PNEUMATIC INDICATING CONTROLLER K796131 REV F 06 2021...
Page 12: ...User Manual 7...
Page 42: ...User Manual 37 MULTI MODE FEEDBACK ASSEMBLIES...
Page 45: ...User Manual 40 REPLACEMENT PARTS KITS...
Page 47: ...User Manual 42...
Page 48: ...User Manual 43 INDICATING CONTROLLER OUTLINE DIMENSIONS...