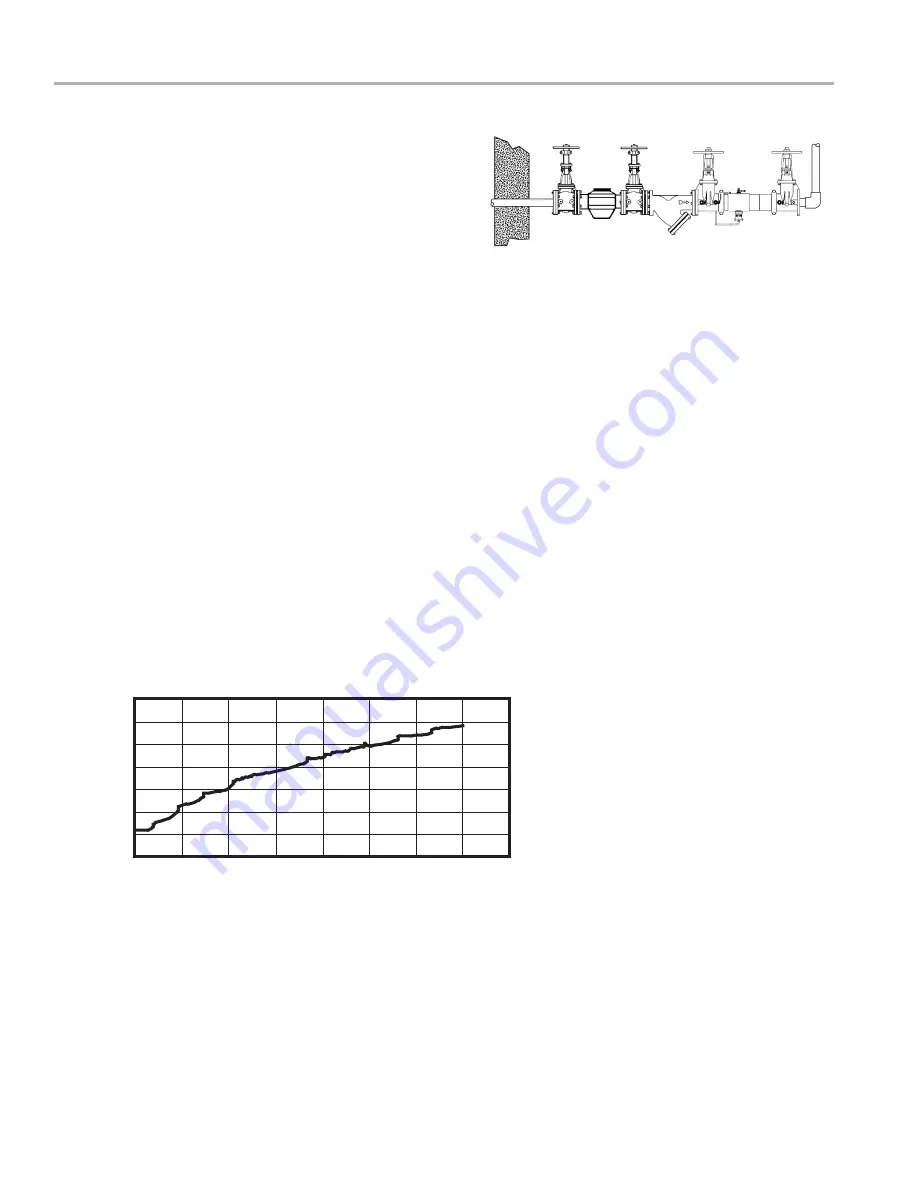
2
Guidelines
1.
Most field problems occur because dirt and debris present
in the system at the time of installation becomes trapped in
the #1 check.
The system should be flushed before the
valve is installed.
If the system is not flushed until after the
valve is installed, remove both check modules from the
valve and open the inlet shutoff to allow water to flow for a
sufficient time to flush debris from the water line. If debris in
the water system continues to cause fouling, a strainer can
be installed upstream of the backflow assembly.
2.
The Series C400 and C500 may be installed in either
horizontal, “N” pattern, or “Z” pattern position as long as the
backflow assembly is installed in accordance with the direc-
tion of the flow arrow on the assembly and the local water
authority approves the installation.
3.
The assembly should be installed with adequate clearance
around the valve to allow for inspection, testing and servicing.
12" (300mm) should be the minimum clearance between the
lower portion of the assembly and the floor or grade. The
valve should be protected from freezing.
4.
Installing a backflow preventer in a pit or vault is not
recommended.
5.
Normal discharge and nuisance spitting are accommodated
by the use of an Ames air gap fitting and a fabricated indirect
waste line. Floor drains of the same size must be provided in
case of excessive discharge.
6.
The C400 and C500 backflow preventer should be tested by
a certified tester at the time of installation.
Note: Assembly body should not be painted.
Horizontal Installation
Basic Installation Instructions
Relief Valve Discharge Rates
2
1
⁄
2
" – 10" (65-250mm) C400 and C500
lpm gpm
1330 350
1140 300
950 250
760 200
570 150
380 100
190
50
0
0
0
20
40
60
80 psi
0
138
276
413
551 kPa
Rate of Flow
Pressure