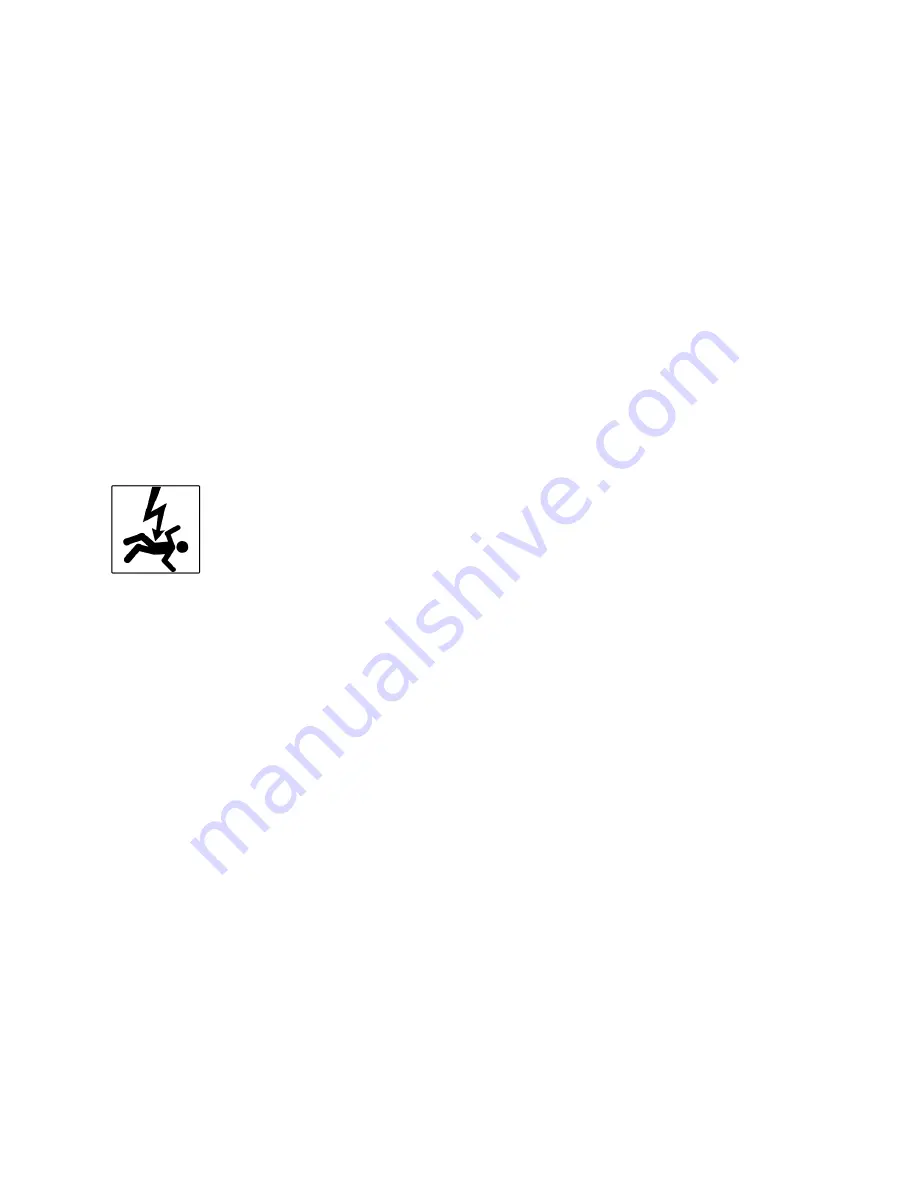
6
should
be
checked
initially
and
periodically
thereafter
to
maintain
applicable
OSHA
PEL
and
ACGIH
TVL
limits.
In
a
poorly
ventilated
area,
it
is
necessary
to
wear
an
approved
air-supplied
respirator.
Always
read
and
understand
the
Safety
Data
Sheets
(SDSs)
and
the
manufacturer
’
s
instructions
for
adhesives,
coatings,
cleaners,
consumables,
coolants,
degreasers,
fluxes,
and
metals.
Always
have
a
trained
watchperson
nearby.
Welding
and
cutting
fumes
and
gases
can
displace
air
and
lower
the
oxygen
level
causing
injury
or
death.
Be
sure
the
breathing
air
is
safe.
Do
not
weld
or
cut
in
locations
near
degreasing,
cleaning,
or
spraying
operations.
The
heat
and
rays
of
the
arc
can
react
with
vapors
to
form
highly
toxic
and
irritating
gases.
Do
not
weld
or
cut
on
coated
metals,
such
as
galvanized,
lead,
or
cadmium
plated
steel,
unless
the
coating
is
removed
from
the
weld
area,
the
area
is
well
ventilated,
and
while
wearing
an
air-supplied
respirator.
The
coatings
and
any
metals
containing
these
elements
can
give
off
toxic
fumes
if
welded.
ELECTRIC
SHOCK
CAN
KILL
WARNING
‐
ELECTRICAL
SHOCK
CAN
KILL.
DO
NOT
TOUCH
LIVE
ELECTRICAL
PARTS
AND/OR
USE
IN
DAMP
LOCATIONS.
The
electrode
and
work
(ground)
circuit
are
electrically
“
HOT
”
whenever
the
welding
equipment
is
on.
Do
not
touch
these
electrically
live
parts
with
your
bare
skin
or
wet/damp
clothing.
Wear
dry,
hole-free
gloves.
Incorrectly
installed
or
improperly
grounded
equipment
is
a
hazard.
Insulate
yourself
from
work
and
ground
using
dry
insulating
mats
or
covers
big
enough
to
prevent
any
physical
contact
with
the
work
or
ground.
Additional
safety
precautions
are
required
when
any
of
the
following
electrically
hazardous
conditions
are
present:
in
damp
locations
or
while
wearing
wet
clothing;
on
metal
structures
such
as
floors,
gratings,
or
scaffolds;
when
in
cramped
positions
such
as
sitting,
kneeling,
or
lying;
or
when
there
is
a
high
risk
of
unavoidable
or
accidental
contact
with
the
workpiece
or
ground.
For
these
conditions,
use
the
following
equipment
in
order
presented:
1)
a
semi-
automatic
DC
constant
voltage,
2)
a
DC
manual
(stick)
welder
or
3)
an
AC
welder
with
reduced
open-circuit
voltage.
In
most
situations,
use
of
a
DC
constant
voltage
wire
welder
is
recommended
and
do
not
work
alone!
Disconnect
input
power
or
stop
engine
before
installing
or
servicing
this
equipment.
Lockout/tag
out
input
power
according
to
OSHA
29
CFR
1910.147
(see
Safety
Standards).
Properly
install
ground
and
operate
this
equipment
according
to
its
Owner
’
s
Manual
and
national,
state/provincial,
and
local
codes.
Always
verify
the
suppl
ground.
Make
sure
that
input
power
cord
ground
wire
is
properly
connected
to
ground
terminal
in
disconnect
box
or
that
cord
plug
is
connected
to
a
properly
grounded
receptacle
outlet.
Keep
cords
dry,
free
of
oil
and
grease
and
protected
from
hot
metal
and
sparks.
Frequently
inspect
input
power
cord
for
damage
or
bare
wiring.
Replace
cord
immediately
if
damaged.
Bare
wiring
can
kill.
Turn
off
all
equipment
when
not
in
use.