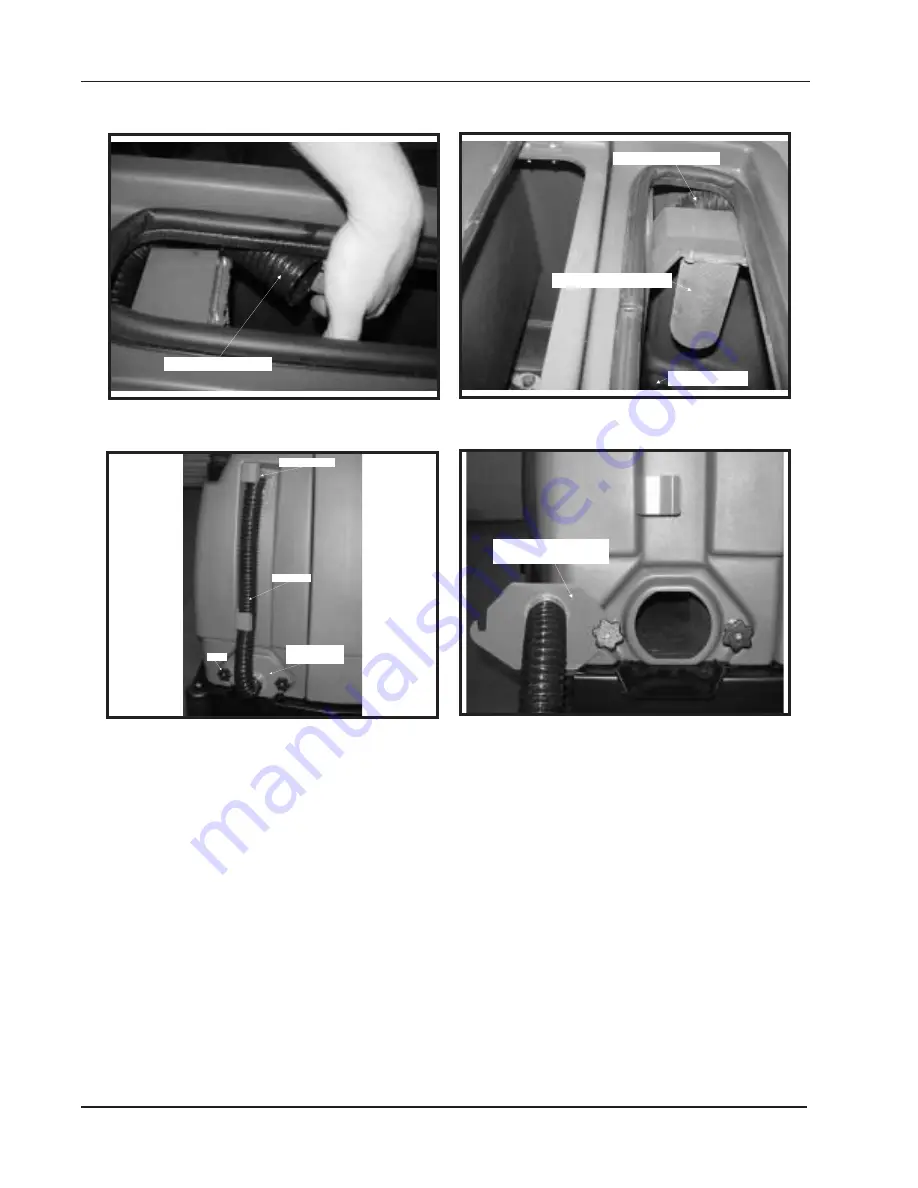
1-40
AMERICAN-LINCOLN
SMART
RECOVERY TANK HOSE
RECOVERY TANK
RECOVERY TANK HOSE
RECOVERY TANK SCREEN
DRAIN HOSE
RECOVERY TANK
CLEAN OUT DOOR
KNOB
DRAIN HOSE PLUG
RECOVERY TANK
CLEAN OUT DOOR OPEN
When the draining operation is complete, open the recovery tank clean out door as shown in figure 49 and flush
the recovery drain hose as shown in figure 46. Clean the recovery tank and recovery tank screen as shown in
figure 47. Close the recovery tank clean out door, drain hose plug, the recovery tank lid and clip the drain hose
into place as shown in figure 48.
Fig. 46
Fig. 47
Fig. 48
Fig. 49
OPERATING INSTRUCTIONS