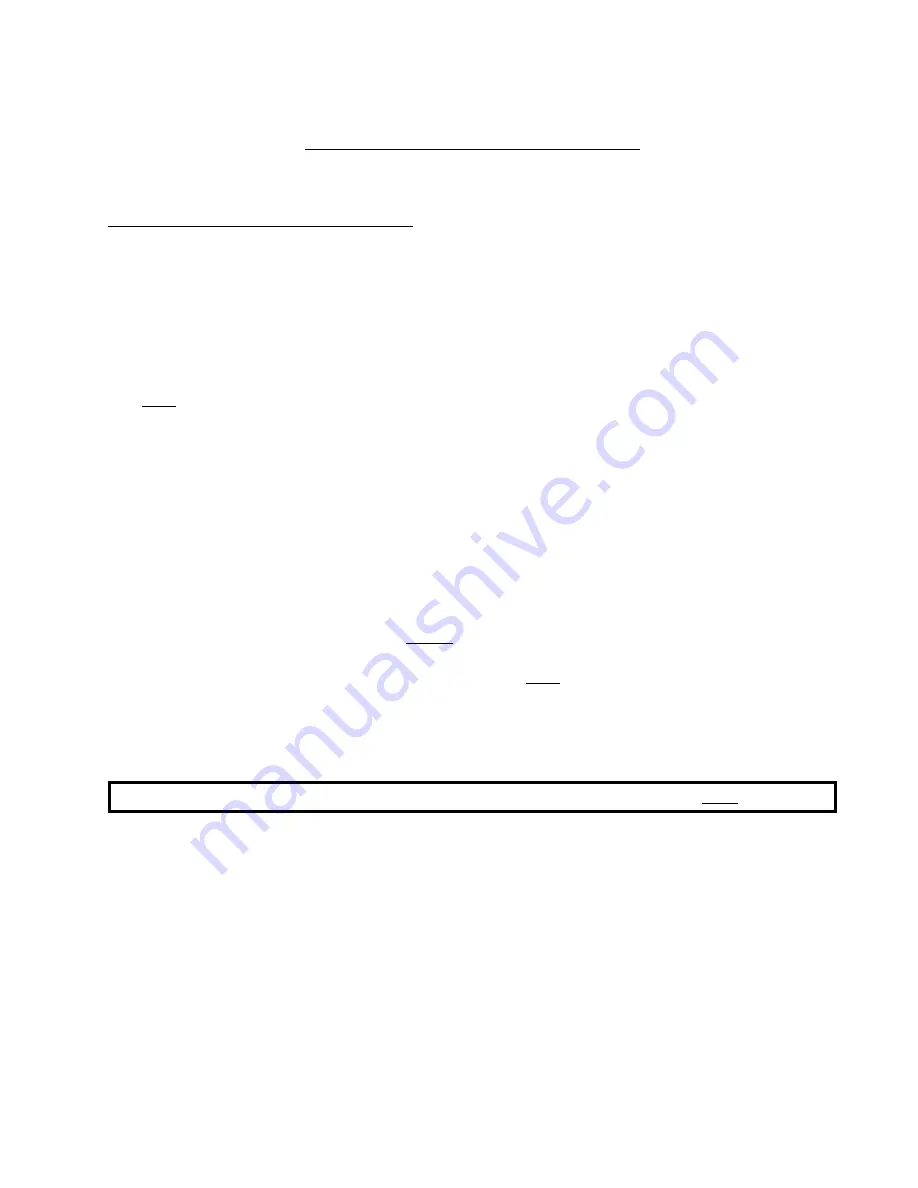
3
SECTION I
IMPORTANT INFORMATION
A. RECEIVING AND HANDLING
The dryer is shipped in a protective stretch wrap cover with protective cardboard corners and top cover (or
optional box) as a means of preventing damage in transit. Upon delivery, the dryer and/or packaging, and
wooden skid
should be
visually inspected for shipping damage. If any damage whatsoever is noticed, inspect
further before delivering carrier leaves.
Dryers damaged in shipment:
1.
ALL
dryers
should be
inspected upon receipt and before they are signed for.
2. If there is suspected damage or actual damage, the trucker’s receipt
should be
so noted.
3. If the dryer is damaged beyond repair, it
should be
refused. Those dryers which were not damaged in a
damaged shipment
should be
accepted, but the number received and the number refused
must be
noted
on the receipt.
4. If you determine that the dryer was damaged after the trucker has left your location, you should call the
delivering carrier’s freight terminal immediately and file a claim. The freight company considers this
concealed damage. This type of freight claim is very difficult to get paid and becomes extremely difficult
when more than a day or two passes after the freight was delivered. It is your responsibility to file freight
claims. Dryer/parts damaged in transit
cannot
be claimed under warranty.
5. Freight claims are the responsibility of the consignee, and
ALL
claims
must be
filed at the receiving end.
ADC
assumes no responsibility for freight claims or damages.
6. If you need assistance in handling the situation, please contact the
ADC
Traffic Manager at (508)
678-9000.
IMPORTANT:
The dryer
must be
transported and handled in an upright position at
ALL
times.