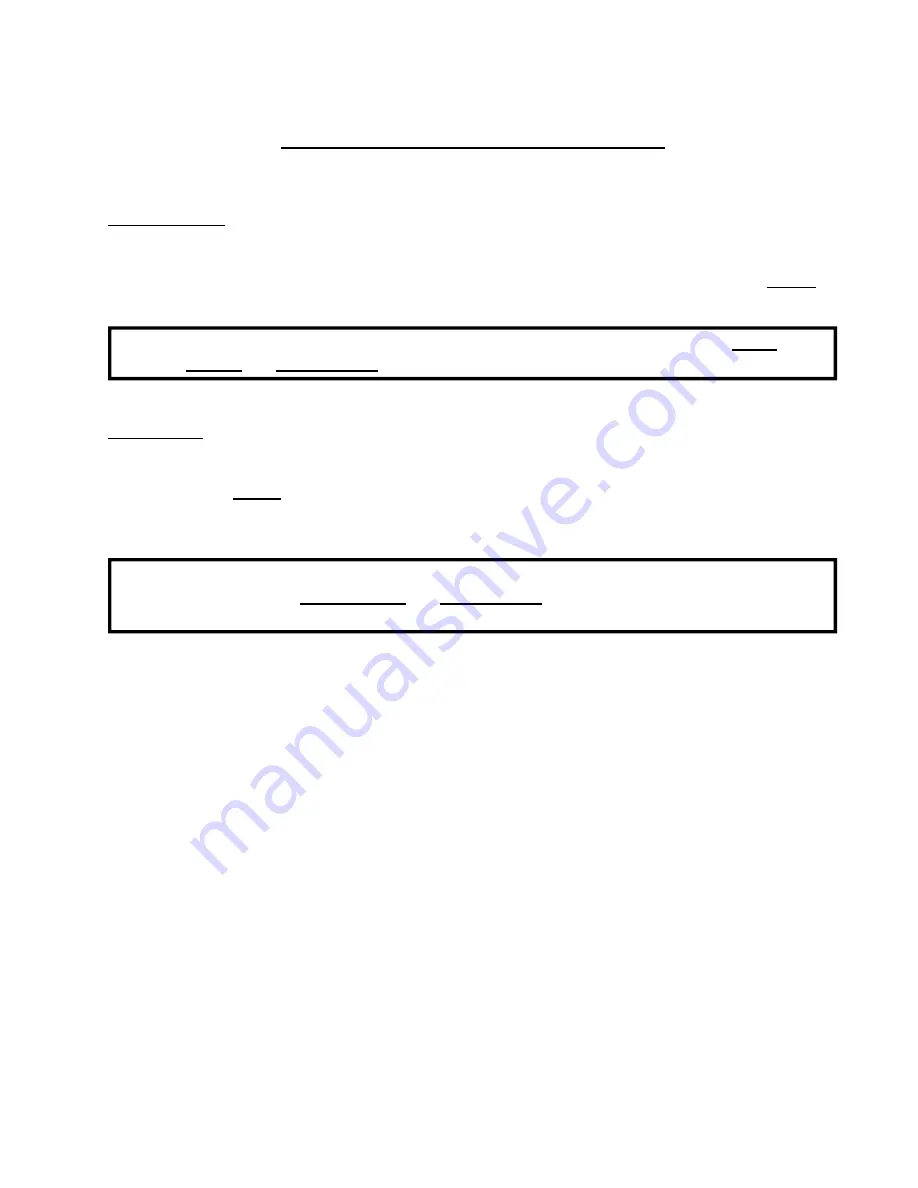
35
SECTION IV
SERVICE/PARTS INFORMATION
A. SERVICE
1. Service
must be
performed by a qualified trained technician, service agency, or gas supplier. If service is
required, contact the reseller from whom the
ADC
equipment was purchased. If the reseller
cannot
be
contacted or is unknown, contact the
ADC
Service Department for a reseller in your area.
NOTE:
When contacting the
ADC
Service Department, be sure to give them the correct
model
number
and
serial number
so that your inquiry is handled in an expeditious manner.
B. PARTS
1. Replacement parts
should be
purchased from the reseller from whom the
ADC
equipment was purchased.
If the reseller
cannot
be contacted or is unknown, contact the
ADC
Parts Department for a reseller in your
area. Parts may also be purchased directly from the factory by calling the
ADC
Parts Department at (508)
678-9000 or you may FAX in your order at (508) 678-9447.
NOTE:
When ordering replacement parts from the
ADC
reseller or the
ADC
factory, be sure to give
them the correct
model number
and
serial number
so that your parts order can be
processed in an expeditious manner.
Summary of Contents for AD-81 II
Page 23: ...19 ...