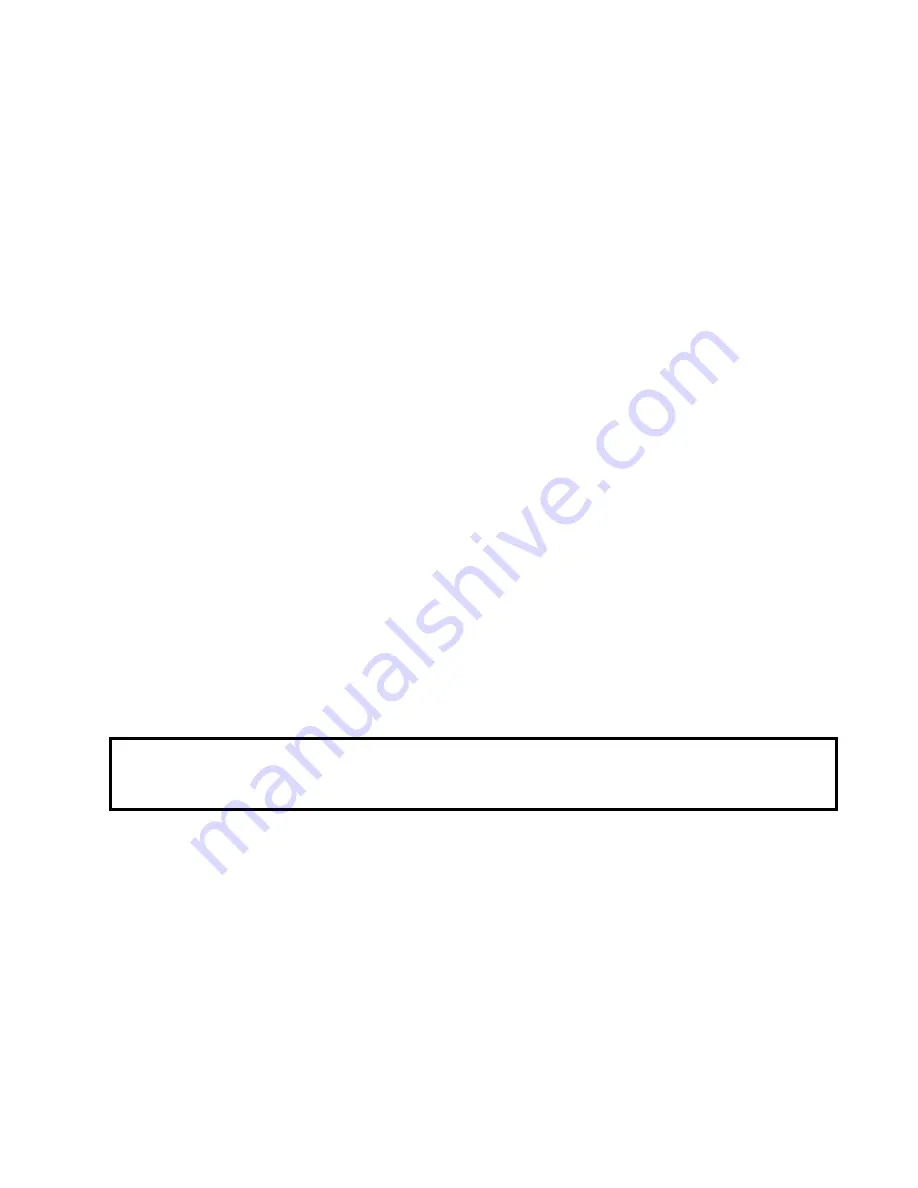
43
e. Failed 24 VAC step down transformer.
2. Microprocessor controller (computer) “door” input LED is on ...
a. Failed microprocessor controller (computer).
H. The dryer does not start (COIN MODELS ONLY)...coin(s) inserted and the LED display
continues to read “FILL” and/or “Amount to Start” (does not read “PUSH”)...
1. Coin acceptor is not adjusted properly or is dirty with lint.
2. Failed coin acceptor switch.
3. Parameter in Program Location 01 (
PL01
) set incorrectly.
a. Bad coin program should be set for “bCrS” and not “bCLO”.
I. Microprocessor controller (computer) LED display reads “dSFL”...
1. LED display consistently reads “dSFL” and will not clear ...
a. Microprocessor controller (computer) 1/8-Amp (Slo Blo) fuse is blown.
b. Failed microprocessor controller (computer) temperature sensor.
c. Broken wire and/or termination in sensor harness somewhere between the sensor bracket and the
Microprocessor Controller (computer).
d. Failed microprocessor controller (computer).
2. LED display reads “dSFL” for a short period of time (30 seconds or less) and then returns to the normal stop
“FILL” mode ...
NOTE
: Once the microprocessor controller (computer) detects a problem, it updates every thirty (30)
seconds so that if a problem was a loose connection in this circuit which corrected itself, the
“dSFL” display condition would automatically be canceled.
a. Loose wire and/or termination in sensor harness somewhere between the sensor bracket and the
microprocessor controller (computer).
b. Failed microprocessor controller (computer) temperature.
J.
Microprocessor controller (computer) LED display reads “Hot”...
The “Hot” display condition indicates a possible overheating condition. The microprocessor controller (com-
puter) monitors the temperature in the dryer at all times. If the microprocessor controller (computer) detects that
the temperature in the dryer has exceeded 220º F (104º C), it will disable
ALL
of the dryer outputs (shut the dryer
down), the buzzer (tone) will sound for approximately 5 seconds, and the LED display will read “Hot”. The LED
display will continue to read “Hot” until the temperature has dropped to 220º F (104º C) or lower and the
microprocessor (computer) is manually reset by closing and opening the program switch (PS).
Summary of Contents for AD-530HS
Page 20: ...16 ...