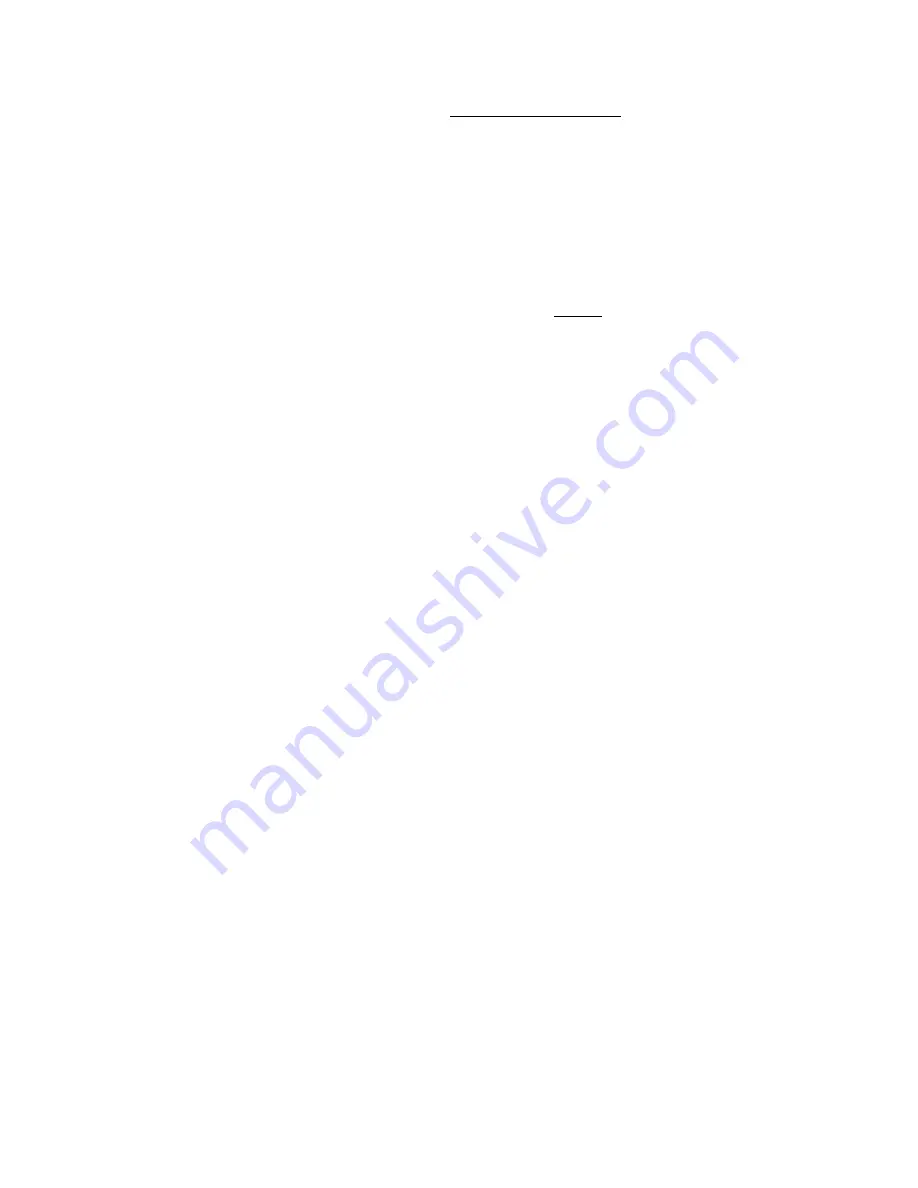
50
3. No (external) compressed air to steam damper (80 psi (552 KPa) required).
4. Failed steam damper 24 VAC pneumatic solenoid switch.
5. Failed piston.
6. Steam damper stuck closed.
Q. Dryer operates but is taking too long to dry...
1. Exhaust duct work run too long or is undersized...back pressure
cannot
exceed .3 inches water column
(0.75 mbar).
2. Restriction in exhaust ...
a. Exhaust back draft damper is sticking partially closed.
b. Restriction in duct work...check duct work from dryer all the way to the outdoors.
3. Low and/or inconsistent gas pressure
(for GAS MODELS ONLY)
.
4. Insufficient make-up air.
5. Poor air/ gas mixture at burner...yellow or poor flame pattern; adjust gas burner air adjustment shutters
(for GAS MODELS ONLY)
.
6. Lint screen not being cleaned on a regular basis or often enough.
7. Extractors (washers) not performing properly.
8. Sail switch is fluttering...restriction in exhaust
(for GAS MODELS ONLY)
.
9. Failed microprocessor controller (computer)...temperature calibration is inaccurate.
10. Failed microprocessor temperature sensor...calibration is inaccurate.
11. Tripped burner/oven hi-limit
(for GAS and ELECTRIC MODELS ONLY)
.
12. Tripped manual reset lint compartment hi-limit thermostat.
13. Steam damper system not functioning properly
(for STEAM MODELS ONLY)
...
a. Damper sticking closed.
b. Leak in pneumatic (air) system.
14. Failed electric oven element(s)
(for ELECTRIC MODELS ONLY)
.
R. Condensation on main door glass...
1. Too long, undersized, or improperly installed duct work.