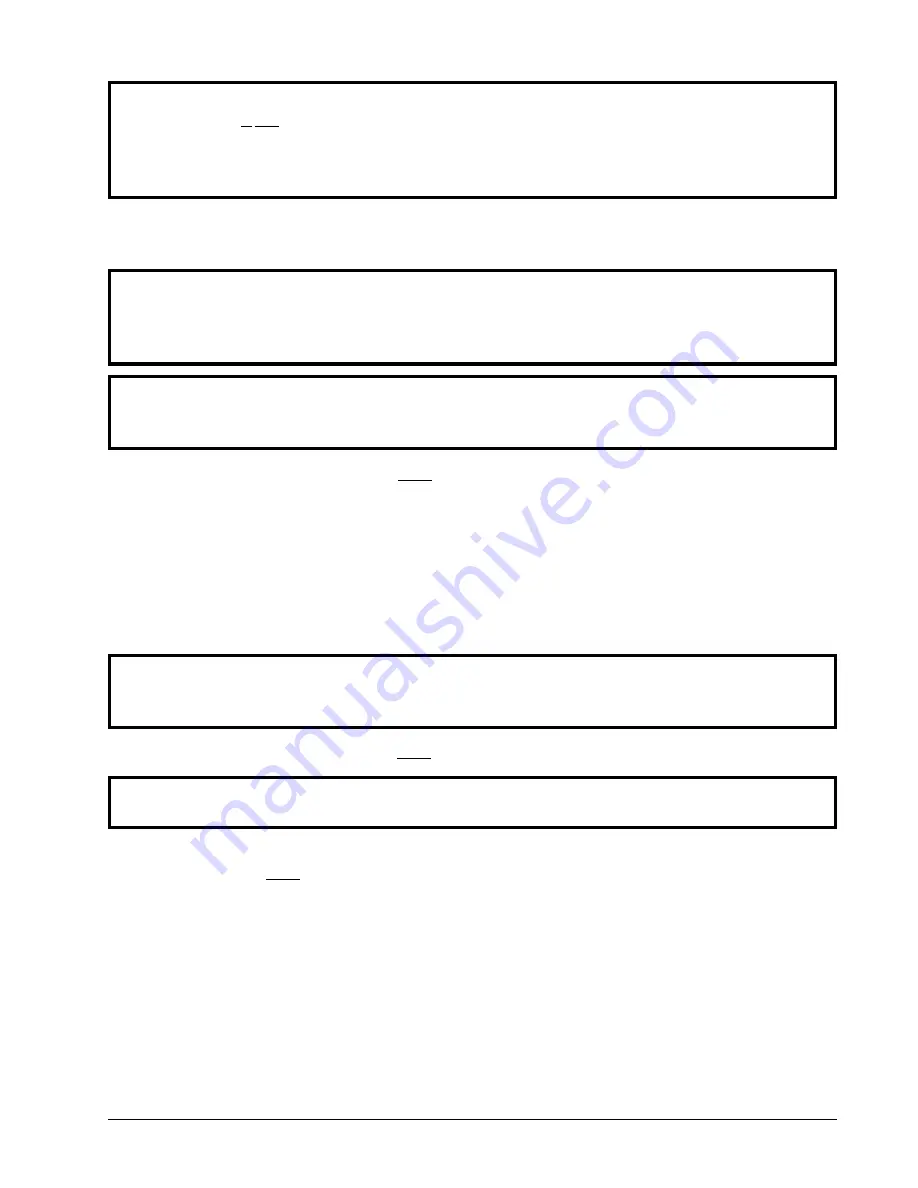
113222 - 5
www.amdry.com
25
NOTE:
Gas model dryers are equipped with an ignition system, which has internal diagnostics. If
ignition
is not
established after one (1) time, the heat circuit in the ignition module will attempt
two (2) more ignitions (total of three [3] ignition attempts). If there is no flame after the third
ignition attempt, the module will lock out until it is manually reset. To reset the ignition system,
open and close the main door and restart the dryer.
b. A gas pressure test
should be
taken at the gas valve pressure tap of each dryer to ensure that the water
column (W.C.) pressure is correct and consistent.
NOTE:
Water column pressure requirements (measured at the pressure tap of the gas valve body):
Natural Gas ----------------------- 3.5 inches (8.7 mb) water column.
Liquid Propane (L.P.) Gas ------ 10.5 inches (26.1 mb) water column.
IMPORTANT:
There is no regulator provided in an L.P. dryer. The water column pressure
must be
regulated at the source (L.P. tank) or an external regulator
must be
added to each
dryer.
4. Make a complete operational check of
ALL
safety related circuits:
a. Door Switch(es)
b. Hi-Limit Thermostats
c. Cycling Thermostats
d. Sail Switch
NOTE:
The sail switch can be checked for proper operation by opening the lint door while the heating
circuit (gas burner/electric oven) is active (on). The heating unit should shut off within a few
seconds. If not, make necessary adjustments to the sail switch.
5. Make a complete operational check of
ALL
operating controls.
NOTE:
If computer program changes are required, refer to the computer programming section of the
manual supplied with the dryer.
6. The dryer
should be
operated through one (1) complete cycle to ensure that no further adjustments are
necessary and that
ALL
components are functioning properly.
BASKET (TUMBLER) COATING
The basket (tumbler) is treated with a protective coating. We suggest dampening old garments or cloth material
with a solution of water and nonflammable mild detergent and tumbling them in the basket (tumbler) to remove
this coating.
7. Check the electric service phase sequence (3-phase [3ø] models only). While the dryer is operating, check
to see if the blower wheel (impellor/fan) is rotating in the proper direction. Looking from the front, the
blower wheel (impellor/fan) should spin in the clockwise (CW) direction. If it is, the phasing is correct. If
the phasing is incorrect, reverse the two (2) leads at connections L1, L2, or L3 of the power supply to the
dryer.