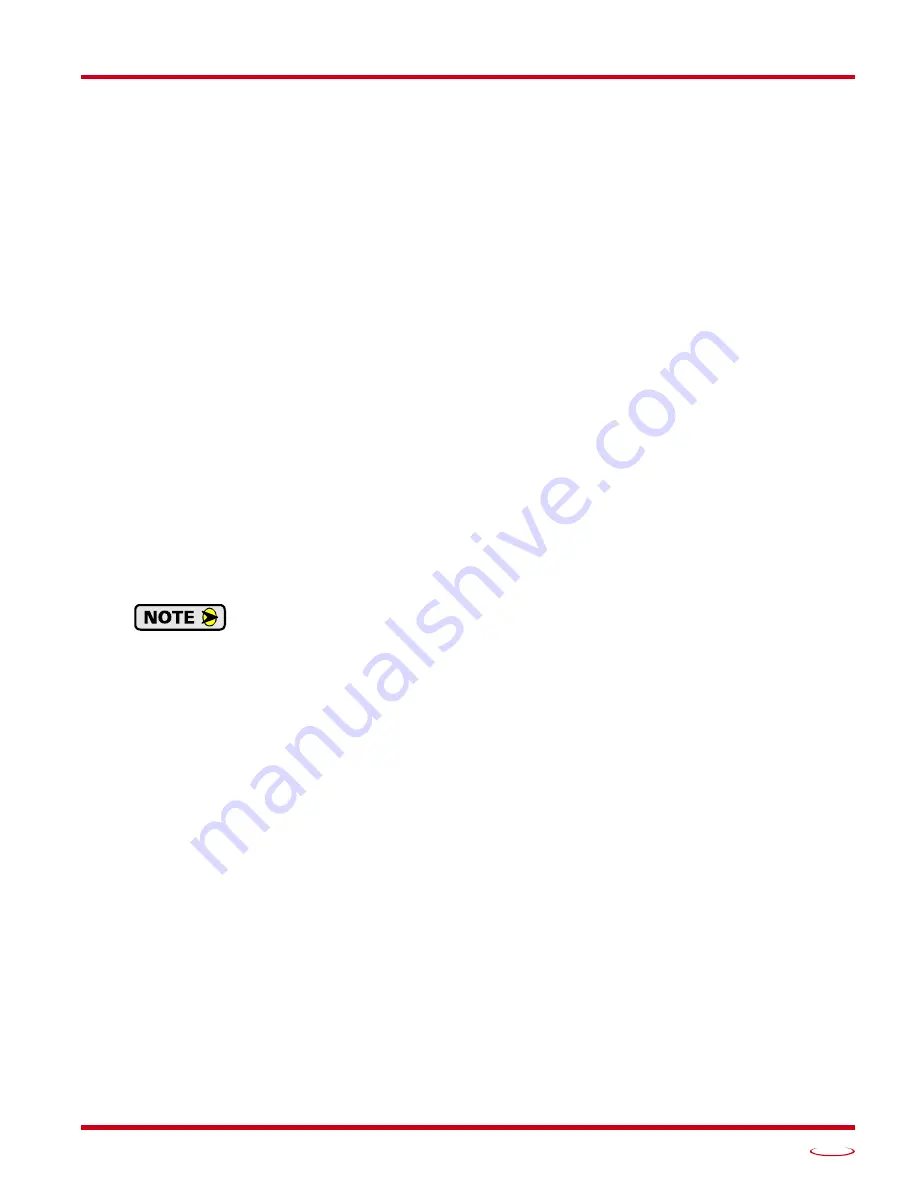
20 Gear Drive, Plymouth Ind. Park, Terryville, CT 06786
Tel: (860) 585-1254 Fax: (860) 584-1973 http://www.amci.com
SMD34K User Manual
SMD34K S
PECIFICATIONS
11
The SMD34K Family (continued)
General Functionality (continued)
The SMD34K units have three DC inputs that can used by the indexer. In some network configurations,
described below, only two inputs are available for use by the indexer. Configuration data from the host sets
how many inputs are available, and the function of these inputs.
Each input can be individually configured as a:
CW or CCW Limit Switch
Home Limit Switch
Capture Position Input (Will capture encoder position on units with the internal encoder.)
Stop Jog or Registration Move Input
Start Indexer Move
Emergency Stop Input
General Purpose Input
Input 3 and Distributed Clock Functionality
By default, the SMD34K is configured to use the SyncManager 2 event of the EtherCAT network to control
the transfer of data from the EtherCAT Slave Controller (ECS) to the microprocessor that controls motion. This
allows the SMD34K to execute commands as soon as new data arrives. If two axes are to start simultaneously,
the actual delay between the two will be equal to the network delay between the two nodes. With a typical
delay of four microseconds plus the transit time between nodes, the delay between starts is inconsequential for
most machines.
On very fast machines, or large machines that require more than one transfer to update all axes, the EtherCAT
Distributed Clock (DC) functionality can be used to closely synchronize motion over multiple axes if using
the SyncMaster2 event proves to be ineffective. When using the DC functionality data transfer between the
ECS and the main processor is controlled with the SYNC0 signal.
In order to minimize delays in reacting to the SYNC0 signal, this signal is brought into the
main processor using the same processor pin used by DC Input 3.
When the Distributed Clock
functionality is enabled on the SMD34K, Input 3 is unavailable as sensor input at the I/O
connector
.
The input must be left disconnected. If a cordset is used, wires for Input 3 must be
electrically isolated.
Encoder Functionality
All SMD34K units can be ordered with an internal incremental or absolute multi-turn encoder. Incremental
encoders can be programmed to 1,024, 2,048, or 4,069 counts per turn. Absolute encoders have a fixed reso-
lution of 2,048 counts per turn and encode a total of 2
21
turns. (32 bits total.) Using an encoder gives you the
ability to:
Verify position during or after a move
Detect motor stall conditions
Maintain machine position when power is removed if using an absolute encoder.
The motor position can be preset to the encoder position with a single command. SMD34K units with abso-
lute encoders allow you to preset the encoder position and save the resulting offset in Flash memory.
Summary of Contents for SMD34K
Page 1: ...MICRO CONTROLS INC ADVANCED U s e r M anual Manual 940 0S280 ...
Page 6: ...TABLE OF CONTENTS SMD34K User Manual ADVANCED MICRO CONTROLS INC 6 Notes ...
Page 50: ...CALCULATING MOVE PROFILES SMD34K User Manual ADVANCED MICRO CONTROLS INC 50 Notes ...
Page 62: ...CONFIGURATION DATA FORMAT SMD34K User Manual ADVANCED MICRO CONTROLS INC 62 Notes ...
Page 80: ...COMMAND DATA FORMAT SMD34K User Manual ADVANCED MICRO CONTROLS INC 80 Notes ...
Page 100: ...LEADERS IN ADVANCED CONTROL PRODUCTS ADVANCED MICRO CONTROLS INC ...