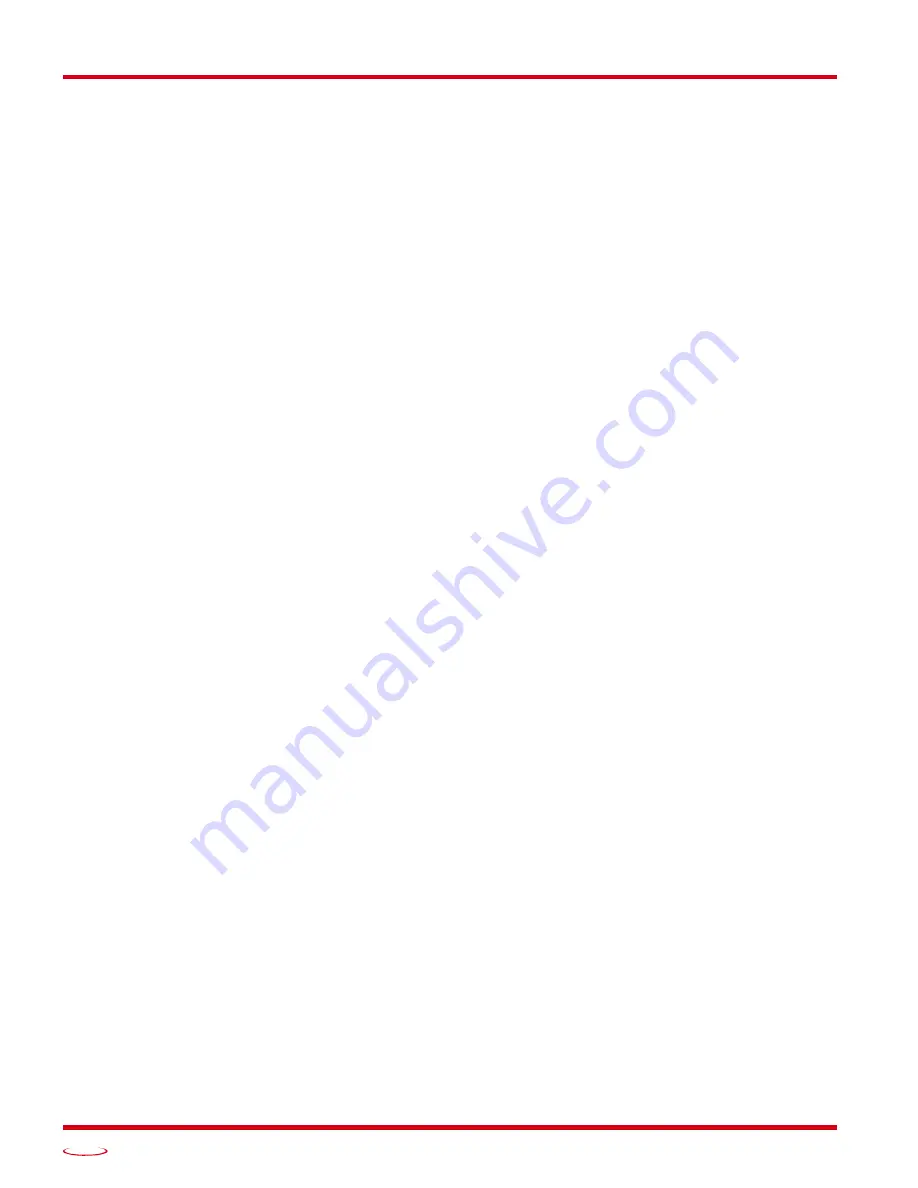
M
OVE
P
ROFILES
SD4840EK User Manual
ADVANCED MICRO CONTROLS INC.
36
Electronic Gearing
The final form of motion control available with the SD4840EK is Electronic Gearing. A quadrature encoder
is required but it is not mounted on the motor controlled by the SD4840EK. The encoder is typically mounted
on a second motor, but it can be mounted anywhere, including on something as simple as a hand crank.
This mode is sometimes referred to as
encoder following
, because the motor will change position in response
to a change in position of the encoder. AMCI refers to it as Electronic Gearing because the SD4840EK has
three parameters that allow you to set any turns ratio you want between the encoder and the motor.
Motor Steps/Turn
This is the same parameter explained at the beginning of this chapter. In Electronic Gearing mode, this
parameter sets the number of encoder counts required to complete one rotation of the shaft of the motor
driven by the SD4840EK. It has a range of 200 to 32,767. This parameter is programmed when you configure
the module and cannot be adjusted while a move is in progress.
ELGearing Multiplier and Divisor
The ratio of these two parameters is applied to the number of encoder pulses read by the SD4840EK before it
determines the number of motor steps to move. Each parameter has a range of 1 to 255. These two parameters
can be adjusted while a move is in progress which allows you to adjust the tracking speed and position of the
motor.
How It Works
The SD4840EK always uses 4X decoding when counting pulses from the encoder. If you set both of your
ELGearing Multiplier and Divisors to 1 and set the Motor Steps/Turn to four times the number of encoder
lines, then the motor will complete one rotation for every rotation of the encoder’s shaft.
Once placed in Electronic Gearing mode, the SD4840EK monitors the Jog Move command bits in the Net-
work Output Registers. When either of these bits is set, the encoder inputs are monitored for a change in posi-
tion. When a change is sensed, the SD4840EK will begin to turn the motor within 50 microseconds. An
increase in encoder counts will result in clockwise rotation. A decrease in encoder counts will result in coun-
ter-clockwise rotation.
The values of the ELGearing Multiplier and Divisor can be changed while electronic gearing motion is occur-
ring. The SD4840EK will accelerate or decelerate the motor to match the new ratio.
Encoder position data can be trapped while in Electronic Gearing mode by configuring one of the discrete DC
input as a Capture Encoder Position input.
Controlled Stops
The encoder stops moving.
Both of the Jog Move command bits equal zero.
Electronic Gearing moves cannot be brought to a controlled stop by using the Hold Move control bit in
the Network Output Registers.
Immediate Stops
The Immediate Stop bit makes a 0
1 transition in the Network Output Data.
A positive transition on an input configured as an E-Stop Input.
A CW or CWW Limit Switch is reached.
Summary of Contents for SD4840EK
Page 1: ...MICRO CONTROLS INC ADVANCED U s e r M anual Manual 940 0S310...
Page 6: ...TABLE OF CONTENTS SD4840EK User Manual ADVANCED MICRO CONTROLS INC 6 Notes...
Page 38: ...MOVE PROFILES SD4840EK User Manual ADVANCED MICRO CONTROLS INC 38 Notes...
Page 48: ...CALCULATING MOVE PROFILES SD4840EK User Manual ADVANCED MICRO CONTROLS INC 48 Notes...
Page 78: ...COMMAND DATA FORMAT SD4840EK User Manual ADVANCED MICRO CONTROLS INC 78 Notes...
Page 94: ...INSTALLING THE SD4840EK SD4840EK User Manual ADVANCED MICRO CONTROLS INC 94 Notes...
Page 104: ...LEADERS IN ADVANCED CONTROL PRODUCTS ADVANCED MICRO CONTROLS INC...