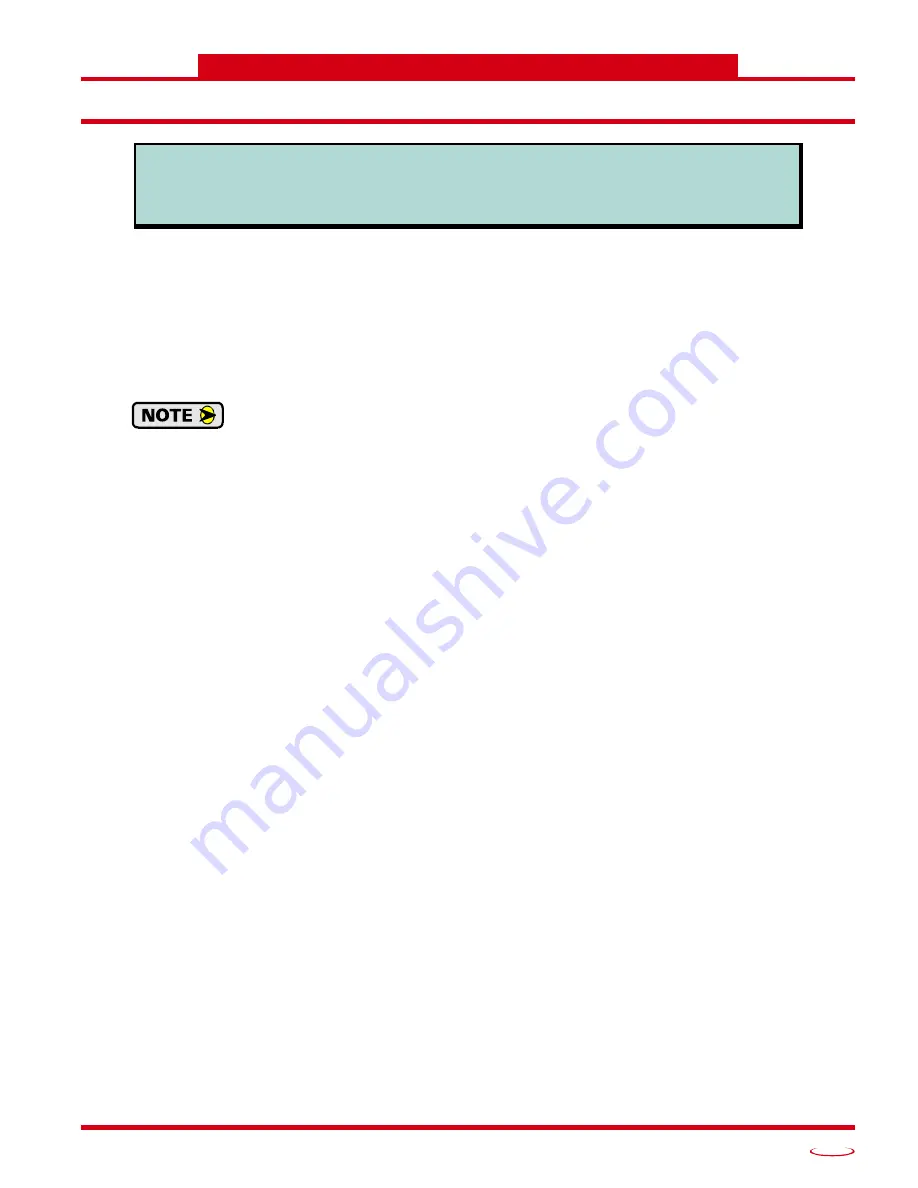
20 Gear Drive, Plymouth Ind. Park, Terryville, CT 06786
Tel: (860) 585-1254 Fax: (860) 584-1973 http://www.amci.com
11
CHAPTER 2
MOTION CONTROL
Motor Position
Commutators are used in motor designs to switch current to the windings of the motor to achieve rotation.
Stepper motors do not have commutators. Instead, the windings of the motor are brought out and attached to
a stepper drive such as the SD17060E. The SD17060E directly controls the current through each winding to
achieve motion. This gives the SD17060E the ability to control not only the speed the motor rotates at, but
also the position that the motor stops at. Therefore we can talk about the position of the motor (angle of the
shaft) and moving the motor from one position to another (rotating the shaft n degrees). This is open loop
positioning control.
This manual assumes that you, the reader, know how a stepper motor works. If you don’t
know, or need a refresher, further information on stepper motors can be found in the Tech
Tutorial section of our website at http://www.amci.com/tech-tutorials.asp.
The number of steps required to achieve one complete rotation of the motor shaft is fully programmable on
the SD17060E. This parameter is called Steps per Turn and can be programmed to any value between 200
and 32,767.
Motor Speed
The rotational speed of the motor shaft is controlled by the SD17060E by controlling how fast the currents
through the windings change. The speed of the shaft is determined by a parameter called Programmed Speed
and the units of this parameter is steps per second.
The Steps per Turn parameter has an effect on the actual rotational speed of the shaft. If you program the
Steps per Turn to 500 and perform a move with a Programmed Speed of 5,000 steps per second, the shaft will
rotate at 5,000/500 = 10 revolutions per second while running at the programmed speed.
There is a Starting Speed parameter in addition to the Programmed Speed parameter that is also defined in
terms of steps/sec. The Starting Speed is the speed at which all moves begin and end. A low Starting Speed
is needed to prevent the motor from stalling when moving a large inertial load. A higher starting speed can be
used on small inertial loads to minimize the time required to accelerate to the Programmed Speed.
The Starting Speed parameter has a range of 1 to 1,000,000 steps/sec.
Acceleration & Deceleration
Like all motor systems, a stepper motor must usually accelerate to its Programmed Speed and decelerate
before coming to a complete stop. The rates of acceleration and deceleration are completely programmable
on the SD17060E as well as the type of acceleration used.
Accelerations and decelerations are programmed in units of steps per millisecond per second (steps/ms/sec)
and have a range of 1 to 5000. When determining the acceleration and deceleration values of your move you
will most likely determine them in terms of revolutions/sec
2
. To convert to steps/ms/sec, multiply your revo-
lutions/sec
2
value by the value of the Steps per Turn parameter and divide by 1,000.
The function of the SD17060E is to control the position and speed of a stepper motor. This chap-
ter outlines the parameters used by the SD17060E to achieve this control and the types of moves
available. Once you are done with this chapter you will have a solid understanding of how the
SD17060E operates.