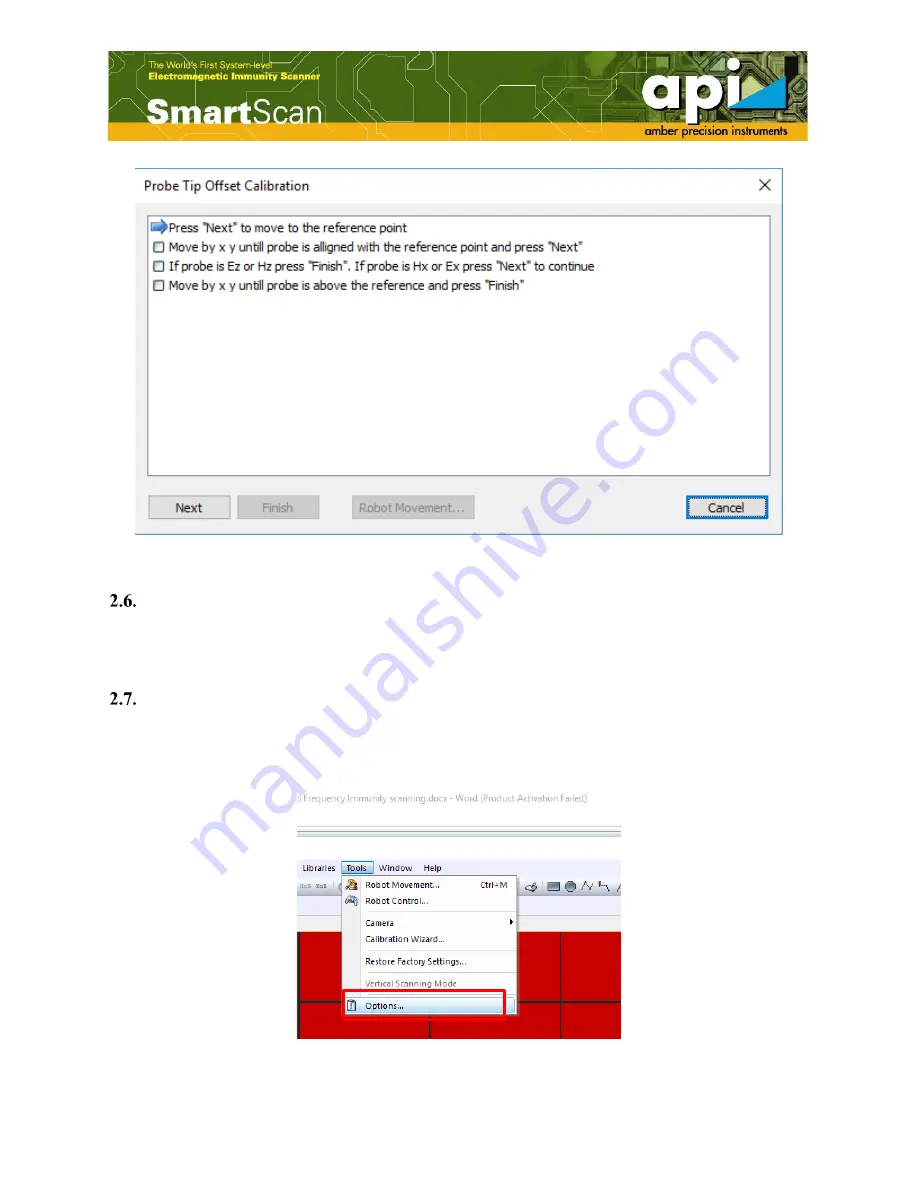
11
Figure 14: Probe XY offset calibration window.
Define scan area and scan height
Please refer to “API SmartScan V5.0 Operation Manual (Common Part)” for detailed
information.
Check instrument and SmartScan software connection
Build connection between SmartScan and instrument. Select the corresponding signal generator
model, communication port and click on “Test Connection” to verify the connection.
Figure 15: Open “Options” window.
Summary of Contents for api SmartScan V5.0
Page 1: ...1 Radio Frequency Immunity Measurement Setup V 5 0 Amber Precision Instruments Inc Dec 2017 ...
Page 6: ...6 Figure 3 Create a new workspace Figure 4 Name the workspace and save in a directory ...
Page 7: ...7 Figure 5 Create a new RFI project Figure 6 Name the RFI project ...
Page 13: ...13 Run measurement Click the Run button to run scanning Figure 18 Run measurement ...